Profilieranlagen: es ist einfacher im Lotto zu gewinnen, als eine Fachkraft zu finden
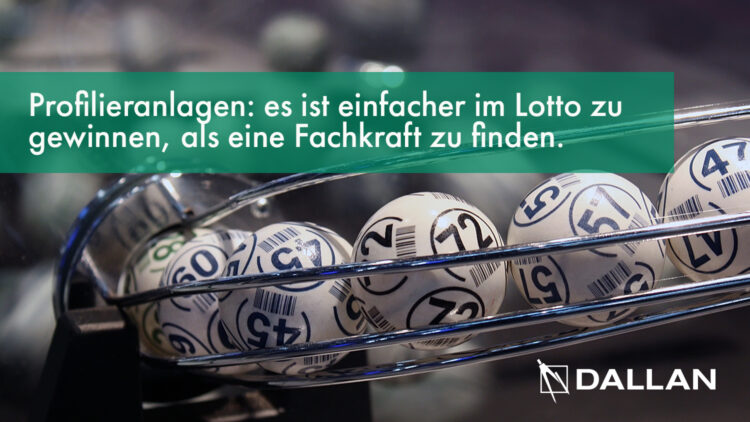
Die Schwierigkeit, Personal für die Produktion zu finden, wird insbesondere in Europa und in Nordamerika zu einem immer größeren Problem.
Dazu kommt das Bestreben, die Produktionskosten so gering wie möglich zu halten und zudem das Personal, das einfache oder sich ständig wiederholende Arbeiten durchführt, durch die Automatisierung zu ersetzen. Der Wunschtraum der Unternehmer und Unternehmen ist eine Produktion mit extrem wenig oder gar keinem Personal.
Ich sah mich deshalb mit einer doppelten Anforderung konfrontiert.
Auf der einen Seite stand das Bestreben der Unternehmen, hochgradig automatisierte Anlagen zu kaufen, die ausgehend vom Rohmaterial möglichst das bereits verpackte und versandbereite Produkt fertigten, und das mit minimalem Personaleinsatz. Dies hat zur Entwicklung von immer hochtechnologischeren Anlagen geführt.
Entnommen aus dem Buch „Die Revolution der Effizienz“
FORDERN SIE DAS BUCH KOSTENLOS AN
Auf der anderen Seite stand die Anforderung, immer anwenderfreundlichere Anlagen zu haben. Fachpersonal war zunehmend schwerer zu finden und die Unternehmen wollten sich nicht von hochspezialisierten Fachkräften abhängig machen, die die einzigen waren, die in das “Geheimnis” der Anlage eingeweiht waren, die sie bedienten.
Die Automatisierung und die Maschinen mussten auch für fachlich nicht qualifiziertes Personal einfach zu bedienen sein.
Wir haben bereits im letzten Kapitel gesehen, dass die automatisierten Coil-to-Pack Anlagen einen wertvollen Beitrag zur Erhöhung der Produktivität in der Fertigung von Trockenbauprofilen leisten.
Das konnte ich auch bei den Fertigungsanlagen für Trockenbauprofile vom Typ T-Bar feststellen, eine der Spezialisierungen unseres Unternehmens. Bei dem T-Bar-Profil handelt es sich um ein Profil in der Form eines umgekehrten T, das aus einem Mittelprofil aus verzinktem Blech und einem Deckprofil aus lackiertem Blech oder Aluminium besteht.
Für die Herstellung dieser Profile wollte ein deutscher Kunde eine Reihe von Fertigungsanlagen mit sehr hoher Kapazität in Betrieb nehmen. Seine Vorgabe war dabei, dass die Anlagen doppelt so viel wie die auf dem Markt verfügbaren Maschinen produzieren sollten, und das mit einem Viertel des Personals.
Die Analyse zeigte, dass nicht nur die Produktion des Profils berücksichtigt werden musste, sondern auch die Qualitätskontrolle und die Verpackung des Produkts. Wir prüften die Anlage unter vielen Aspekten, von den Abmessungen und der Länge der Coils über die Produktionsgeschwindigkeit bis zur Verbrauchsgeschwindigkeit der Materialien in der Anlage, der Qualität der Rohmaterialien, der Art der Verpackung und einer ergonomischen Studie zum Gewicht der Profile und der Installation eines Vision-Systems zur Durchführung der Qualitätskontrolle der Profile.
Das Ergebnis waren die ersten kompletten Coil-to-Box Anlagen, die ausgehend vom Coil das Endprodukt lieferten, das bereits in Kartons verpackt und auf Paletten zur Umreifung und für den Versand bereitstand.
Diese Anlagen produzierten diese dekorativen, sehr technischen und komplexen Profile mit einer Geschwindigkeit von mehr als 100 Metern pro Minute.
Dazu waren nur drei Bediener für jeweils zwei Anlagen erforderlich, deren Aufgabe hauptsächlich darin bestand, die Rohmaterialzufuhr zu den Maschinen sicherzustellen. Maschinen, die im wahrsten Sinne des Wortes Tonnen von verzinktem, beschichtetem Blech, hochwiderstandsfähigem Stahl für die Clips, sowie Karton und Kleber für die Verpackung verschlangen, um am Ende der Anlage Paletten mit perfekt gestapelten Kartons auszuspucken.
Auch die Coil-to-Window Anlagen, die wir bereits bei der Firma Profalux und der Unternehmensgruppe Stella angesprochen haben, sind optimal zur Einführung der Automatisierung in der Herstellung von Rollladenbehängen geeignet. In diesem Fall handelt es sich zwar auch um eine Automatisierung, aber wir sprechen nicht von der Verpackung, sondern von der Konfektionierung.
Die Coil-to-Window Anlagen gibt es auch für ein anderes Sonnenschutzprodukt, die außenanliegenden Raffstoren.
Bis vor einigen Jahren waren diese Produkte typisch für die Märkte Schweiz, Österreich und Deutschland. Die Nachfrage hat sich heute auf ganz Osteuropa und Frankreich ausgebreitet und erreicht mittlerweile auch Italien. Im Vergleich zur Rollläden haben außenanliegende Raffstoren den Vorteil, dass der Lichteinfall in den Raum durch Verstellung des Neigungswinkels der Lamellen reguliert werden kann.
Auch in diesem Fall ist genau wie bei den Rollläden jedes Fenster anders und dementsprechend unterscheiden sich auch die produzierten Behänge. Es ist deshalb von ausschlaggebender Bedeutung, die Produktion so zu steuern, dass eine manuelle Programmierung der Maschinen nicht erforderlich ist.
Die Raffstoren gliedern sich in zwei Hauptkategorien, und zwar in Raffstoren mit C-Lamellen bzw. mit Z-Lamellen. Im Vergleich zum Rollladen ist die Montage der Raffstoren komplexer, da sie das Anbringen der Führungsnippel an den Enden der Lamellen und die Seiten-Hacken für die Montage auf Leiterkordeln oder Schlaufenkordeln mit unterschiedlicher Form erforderlich machen.
Bis 2005 fertigten die Profiliermaschinen ausschließlich Profile, die von Hand auf den entsprechenden Leiterkordeln zu den Behängen zusammengesetzt wurden. Der Zeitaufwand hierfür war immer der größte, und nicht jener für die Produktion der Profile, die auch 60 Meter pro Minute erreichen konnte.
Auf diesem Markt war Dallan bereits vertreten, da es sich um Profile aus beschichtetem Dünnblech handelt, auf die Dallan spezialisiert ist. Unsere Kunden begannen, Anlagen bei uns anzufragen, die in der Lage wären, die Montage dieser Profile auf den Leiter- und Schlaufenkordeln durchzuführen. Wir begannen deshalb mit der Entwicklung und dem Bau der ersten Anlagen für die Anhakung und das Einfädeln, die wir dann auch patentierten.
Der Arbeitsaufwand für das manuelle Montieren des Behangs ist so hoch, dass sich die Automatisierung innerhalb von kürzester Zeit bezahlt machte.
Die Anlagen von Dallan für Raffstoren funktionieren mit der gleichen Logik wie die Anlagen für Rollläden. Sie bestehen aus verschiedenen Arbeits-und Montagestationen, die durch Förderer getrennt sind, die als Puffer fungieren und die Bearbeitungszeiten zwischen den einzelnen Stationen ausgleichen. Im Laufe der Zeit haben wir an der Synchronisation der Geschwindigkeiten der verschiedenen Maschinen gearbeitet, um Prozessengpässe zu vermeiden und den heutigen optimierten Stand zu erreichen.
Das Ergebnis? Eine Anlage für Raffstoren mit C-Lamellen wie in diesem Video:
Im ersten Teil der Anlage werden die Profile komplett mit Lochungen gefertigt. Das bearbeitete und geschnittene Profil wird an Transportbänder übergeben, die es zu der Maschine befördern, die die Führungsnippel einsetzt. Eine zweite Gruppe bringt die Profile zur letzten Montagestation, wo sie einzeln auf eine Leiterkordel aufgefädelt werden.
Der fertige Behang wird automatisch oder von einem Mitarbeiter entnommen und in der Regel auf einenWagen abgelegt, um zu den Endmontagestationen gebracht zu werden.
In diesen Stationen wird der Behang geöffnet und kontrolliert und die letzten Bauteile werden angebracht, wie die Unterschiene, die den Behang beschwert und spannt, die Aufzugsbänder und der Antrieb, der in die Kopfschiene eingesetzt wird.
Mit diesen Lösungen machen die Fertigung und Montage der Profile nur ein Minimum an Handarbeit und Zwischenlagern erforderlich und außerdem erlauben sie einen extrem schnellen Profilwechsel und Farbwechsel des Bandes.
Genau das gleiche System gibt es auch für Z-Profile, bei denen die Montage noch aufwändiger ist. Bei diesen Profilen werden seitliche Haken angebracht, die sich um die Schlaufenkordeln schließen. Wir mussten deshalb auch in diesem Fall eine Anlage mit unabhängigen Arbeitsstationen entwickeln, die die Montage vereinfacht und eine schnelle Fertigung ausgehend vom Coil bis zum konfektionierten Behang ermöglicht, der für die Endmontage bereit ist.
Diese Automatisierungen haben das Personal, das für die bisherige Fertigung erforderlich war, auf weniger als ein Drittel reduziert und noch weiter große Vorteile mit sich gebracht, wie die Reduzierung der unfertigen Erzeugnisse und die Einführung einer zentralen Produktionssteuerung mit parametrischer Programmierung, die das Laden der Auftragsdaten direkt aus dem betriebseigenen ERP-System erlaubt.
Die Abbildung zeigt, dass der Bediener mithilfe der Software, die in die Maschine integriert ist, die Form der Leiterkordel prüfen kann, bevor der Maschine der Produktionsauftrag erteilt wird.
Die Steuerungssoftware dieser Anlagen stellt einen wichtigen Aktivposten für das Unternehmen dar: Die neuesten Softwaresysteme erlauben eine Kontrolle der Aufträge in Produktion, das Senden der Joblisten und das Empfangen automatischer Rückmeldungen über die bereits erledigte Produktion sowie die Verwaltung der Produktion zusätzlicher Lamellen für eventuelle Reparaturen, wenn bei der nachgeschalteten manuellen Montage Probleme auftreten.
Bei der Fusion 2013 wurde auch die Fima Elda von Dallan übernommen, die auf die Herstellung von Schalttafeln und Software für die Anlagen von Dallan spezialisiert war. Über ein firmeninternes Team an Programmieren zu verfügen, das die Steuerungssoftware entwickelt, hat uns die Möglichkeit gegeben, gezielt auf die Marktanforderungen zu reagieren und Softwarelösungen zu entwickeln, die weit mehr bieten, als die Kunden normalerweise erwarten.
Heute sind die firmeninternen Programmierer von entscheidender Bedeutung, um durch die Automatisierung wichtiger Teile des Informationsflusses im Unternehmen einen enormen Wert an unsere Kunden weiterzugeben.
Wie wir bereits gesehen haben, ist es für eine LEAN PRODUCTION nicht ausreichend, nur die Materialverschwendung zu eliminieren, sondern es müssen auch die Informationsflüsse und Prozesse eliminiert werden, die nicht papierlos arbeiten und keinen Mehrwert für den Kunden schaffen!
Mit der Flexibilität eines Teams, das sich mit der Softwareentwicklung befasst, lassen sich die Lösungen schaffen, die auf der Abbildung dargestellt sind:
In diesem Fall ist der Informationsfluss optimiert und obwohl wir dem Produktionsleiter und dem Bediener einen Handlungsspielraum gelassen haben, haben wir den gesamten Fluss an ausgedruckten Aufträgen und manueller Dateneingabe mit allen dadurch bedingten Fehlern eliminiert.
Entnommen aus dem Buch „Die Revolution der Effizienz“
FORDERN SIE DAS BUCH KOSTENLOS AN
Andrea Dallan
CEO – Dallan Spa