Der Cash Flow in einem Coil-To-Window System
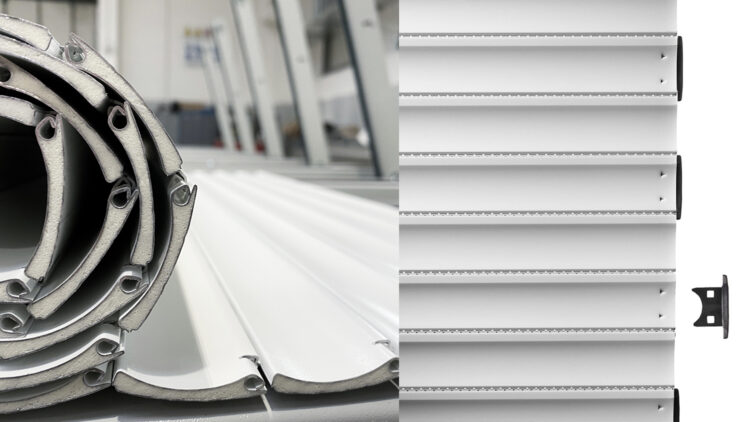
In diesem Abschnitt möchte ich zeigen, wie die Hersteller von fertigen Rollladenpanzern mit den Coil-to-Window Systemen Einsparungen von mehr als 200.000 Euro pro Jahr generieren können, welche die Hauptfaktoren sind, die diese sehr hohen Einsparungen generieren, und warum dieses System deutlich nachhaltiger und umweltfreundlicher als die herkömmlichen Systeme ist.
Produktion von Rollläden aus Aluminium: Steigerung der Gewinne und der Nachhaltigkeit mit Coil-to-Window Systemen.
Die Nachfrage nach Rollläden aus ausgeschäumtem Aluminium steigt in Europa und weltweit kontinuierlich. Grund dafür sind die vielen Vorteile, die sie bieten:
- Energieersparnis (drastische Senkung der Kosten für die Gebäudeklimatisierung)
- Privatsphäre
- Sicherheit und Schutz der Fenster und der Fensterrahmen
- Sehr einfache Automatisierung und Einbindung in die Gebäudeautomation
Der Standardproduktionszyklus für Rollläden startete mit den bereits geformten Profilstäben mit einer Länge von 5, 6 und 7 Metern, die nach Maß abgelängt und montiert wurden, mit einem Ausschuss im Bereich von 5 bis 12%.
Die modernen Coil-to-Window Anlagen fertigen dagegen direkt ausgehend vom Blechband, das vom Coil abgewickelt wird, und produzieren komplette, nach Maß zugeschnittene Rollläden, wobei praktisch kein Ausschuss entsteht.
Das herkömmliche Verfahren: Fertigung aus profilierten Stäben
Am weitesten verbreitet ist das Fertigungssystem für Rollladenbehänge ausgehend von Paketen bereits geformter Profile. Diese Profile werden nach Maß abgelängt und montiert oder einer Maschine zugeführt, die die Profile einzeln entnimmt, nach Maß ablängt und montiert.
Beim Zuschneiden der Stäbe auf die Fensterbreite bleibt ein Reststück übrig, das als Ausschuss anfällt.
Die Tabelle zeigt den Ausschuss in Prozent für Stäbe mit einer Länge von 5,6 m in Abhängigkeit von der Breite des Rollladenbehangs.
Die Rollladenhersteller haben mit vielen Ansätzen versucht, diesen Ausschuss zu optimieren, aber alle Lösungen waren entweder sehr zeitaufwändig oder machten die Anwesenheit eines Bedieners erforderlich.
Im Allgemeinen wird von einem Ausschuss im Bereich von 5 bis 12% ausgegangen.
Das Produktionssystem Coil-to-Window für Rollladenbehänge
In den drei Minuten, die für das Lesen dieses Abschnitts erforderlich sind, produziert ein COIL-TO-WINDOW System von Dallan einen fertigen Rollladenbehang direkt vom Coil, und das praktisch ohne Ausschuss oder dass Fachkräfte dazu erforderlich sind.
Die Produktionssysteme Coil-to-Window produzieren fertige und montierte Rollladenpanzer direkt vom Coil.
Dazu ist nur ein Bediener notwendig und die komplexen Prozeduren für das Bewegen der Profilpakete, die beim Transportieren leicht beschädigt werden können, entfallen.
Die Produktionsdaten der einzelnen Rollladenpanzer wie Breite, Höhe und Stückzahl können direkt vom Büro aus oder mit Excel-Tabellen geladen werden.
Die Produktion der Rollladenpanzer ist parametrisch, sodass keine Zeit für die Programmierung der Anlage veranschlagt werden muss!
Diese automatische Fertigungslinie umfasst:
- Abwickelhaspel mit dem Rohmaterial (in der Regel beschichtetes Aluminium)
- Präzisionsprofiliermaschine T4
- Schnellwechselsystem COMBI mit den Profilierrollen für ein Rollladenmodell
- Ausschäummaschine, die die Komponenten des Schaums mischt (in der Regel Polyol und Isocyanat)
- Tische für die Aushärtung des Schaums
- Fliegende Säge für das Zuschneiden der Profile nach Maß
- Stanzmaschine, die die Lüftungslöcher ausführt (auch ausgerichtet)
- Einfädeltisch
- Blockierungssystem mit Kunststoffclips oder mit mechanischer Blockierung ohne Clips (Patent Dallan)
Diese Anlage macht bei laufender Produktion lediglich die Anwesenheit von einem Bediener erforderlich, der die Qualitätskontrolle durchführt und die fertigen Rollladenbehänge entnimmt.
Für die Fertigung von Rollläden für 25.000 Fenster sind 2 bis 2,5 Millionen laufende Meter Profil pro Jahr erforderlich, je nach Abmessungen der Fenster und Profile. Die Analyse der Einsparungen, die mit einem Coil-to-Window System erzielt werden können, basieren auf diesen Zahlen.
Materialeinsparungen, die mit dem Coil-to-Window System für verschiedene Profilgrößen erzielt werden können
Die Tabelle zeigt die Menge an Aluminium und Polyurethan für ausgeschäumte Aluminiumprofile mit unterschiedlichen Abmessungen für Stäbe mit einer Länge von 1 Meter.
Die Kosten für Aluminium und Polyurethan sind variabel und können bei den entsprechenden Herstellern angefragt werden.
Aus den über 300 Rollladenprofilen aus dem Katalog von Dallan wurden die wichtigsten Rollladenprofile ausgewählt. Das Angebot der Profile für Rollläden aus Aluminium ist in verschiedene Produktgruppen eingeteilt, um sowohl das Segment der hochwertigen Profile zu bedienen, als auch das Niedrigpreissegment („ECO“-Profile).
Eco-Profile haben in der Regel eine geringere Abwicklung (Blechbandbreite) und meist auch eine geringere Dicke. Auf das Aluminium entfallen 86 bis 92% der Rohmaterialkosten, wie der Tabelle entnommen werden kann.
In der Tabelle sind im unteren Teil die Rohmaterialkosten für die Produktion von 2,5 Millionen Meter Rollladenprofil aufgelistet, sowie die Einsparungen, die alleine durch eine Senkung der Beschaffungskosten für Aluminium und Polyurethan bei einer Bedarfssenkung von 5% bzw. von 12% generiert werden.
Ein wichtiger Hinweis: Die angegebenen Mengen und Einsparungen wurden nur unter Berücksichtigung der Einsparung bei den Beschaffungskosten von Aluminium und Polyurethan berechnet. Wenn die Profilstäbe zugekauft werden, sind die Einsparungen doppelt bis dreifach so hoch, da der Lieferant zu den Rohmaterialkosten seinen Aufschlag addiert, der folgende Kosten umfasst:
- Bearbeitungskosten,
- Energiekosten,
- Personalkosten,
- Versandkosten,
- Aufteilung der Fixkosten,
- und die Gewinnmarge.
Das Gewicht des Polyurethans wurde für PU-Schaum mit geringer Dichte berechnet und die Kosten für Aluminium und Polyurethan beziehen sich auf die Werte vom Oktober 2016.
Die Jahresproduktion einer Coil-to-Window Anlage, die mit einer Produktionsgeschwindigkeit von 37 Metern pro Minute und an 220 Tagen pro Jahr gefahren wird, liegt bei 2 bis 2,5 Millionen Meter pro Schicht. Dieser Wert variiert anhand der Größe des Profils, der durchschnittlichen Abmessungen der produzierten Fenster und der Anzahl der erforderlichen Farbwechsel. Diese Daten wurden außerdem durch die Erfahrungswerte der Unternehmensgruppe Stella bestätigt (siehe Erfahrungsbereich am Anfang des Buchs).
Wenn in zwei oder drei Schichten gearbeitet wird, multiplizieren sich die Einsparungen mal zwei oder mal drei. Außerdem gibt es auch Coil-to-Window Fertigungsanlagen, die eine Produktionsgeschwindigkeit von 60 bis 80 Metern pro Minute erreichen können.
Der Ausschuss bei der Fertigung von 2,5 Millionen Metern Profil ausgehend von Stäben mit fester Länge entspricht ca. 300.000 laufenden Metern Aluminiumprofil und Polyurethan, was wiederum 30,8 Tonnen Aluminium und 2,7 Tonnen PU-Schaum entspricht, die im Produktionsprozess miteinander verbunden wurden.
Diese Materialien lassen sich nach wie vor nur schwer recyceln und müssen entsorgt werden, was für das Unternehmen mit Kosten verbunden ist. Durch eine Reduzierung des Ausschusses verringern die Coil-to-Window Systeme auch die Umweltbelastung dieser Produktion und garantieren dem Hersteller der Rollladenpanzer gleichzeitig eine hohe jährliche Rentabilität.
Analysiert man die Coil-to-Window Technologie unter dem Gesichtspunkt LEAN, zeigt sich, dass diese Technologie alle Faktoren zu bieten hat, die eine schlanke Produktion ausmachen:
- Reduzierung und Eliminierung des Ausschusses.
- Reduzierung des Umlaufbestands auf ein Minimum: Keine Lager für Halbzeuge.
- Fliegende Umstellung der Produktgröße: Es können Rollladenbehänge mit unterschiedlichen Abmessungen produziert werden, ohne dass eine Stillsetzung der Maschine dazu notwendig ist.
- Eine Programmierung der Maschine ist nicht erforderlich: Die Anlage übernimmt die Fertigungsaufträge direkt aus dem kundeneigenen ERP-System.
- Reduzierung des Personals auf ein Minimum: Die Produktion von 2,5 Millionen Metern Rollladenbehänge macht in der Regel mindestens 4 Personen erforderlich, an einer Coil-to-Window Anlage hingegen ist ein einziger Bediener ausreichend, der keine Fachkraft sein muss.
Im Streben nach Effizienz führen die innovativsten Technologien neue Denkansätze ein. Um die Produktivität, die Effizienz und die Nachhaltigkeit der Produktion zu erhöhen, wird ein hoher Automatisierungsgrad eingeführt, der das Personal, das in der Regel für die Herstellung der gleichen Anzahl Rollladenpanzer gebraucht wird, auf ein Viertel reduziert.
Die Coil-to-Window Technologie ist eine große Chance, von der man profitieren kann, um folgende Ziele zu erreichen:
- Einen sehr hohen Automatisierungsgrad,
- einen schlanken Prozess mit Fließfertigung,
- wegfallende Programmierung,
- eine automatische Qualitätskontrolle in der Anlage,
- die Anbindung an das betriebsinterne ERP-System.
In diesem Kapitel haben wir gesehen, dass sich mit der modernsten Coil-to-Window Technologie Einsparungen in Höhe von 5 bis 12% beim Rohmaterial erzielen lassen und dass sich mit diesen Anlagen Produkte höherer Qualität bei Verwendung von weniger Rohmaterial sowie reduziertem oder ganz gegen Null gehenden Ausschuss produzieren lassen.
Das macht die Produktion von Rollladenbehängen noch rentabler, nachhaltiger und umweltfreundlicher.
Mit diesem Link können Sie ein Video aufrufen, das eine laufende Coil-to-Window Anlage zeigt, in diesem Fall mit Anbringung der Kunststoffclips.
Wenn Sie auch mehr über das Coil-to-Window-System erfahren möchten, aber nicht nur, abonnieren Sie unsere Live-Meisterklasse: Jede Woche werde ich ein Thema vertiefen, das sich auf unsere Maschinen und unsere Produktionssysteme mit Schwerpunkt auf Lean Production bezieht.
Um den Zugang anzufordern, klicken Sie auf den Link und füllen Sie das Formular aus!
ICH MÖCHTE MICH FÜR DIE MASTERCLASS ANMELDEN
Andrea Dallan
CEO – Dallan Spa