Effiziente Profiliermaschinen und Produktionsanlagen
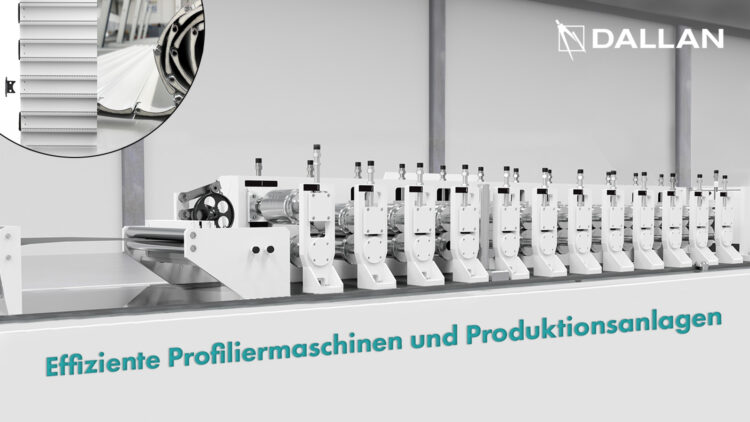
Neben dem Bau unserer Stanz- und Laserschneidmaschinen habe ich im Jahr 2008 gemeinsam mit meinem Vater begonnen, auch die technische Beratung und den Vertrieb von Profilieranlagen voranzubringen.
Das Unternehmen Dallan, gegründet im Jahr 1978, mit Sitz in Castelfranco Veneto, Italien, hatte sich durch langjährige Erfahrung einen Namen als Spezialist im Bau von Profilieranlagen im Dünnblechbereich erworben. Diese Spezialisierung ermöglichte es uns, die Kompetenzen in den Bereichen Trockenbau und Sonnenschutz ebenfalls weiter auszubauen.
Entnommen aus dem Buch „Die Revolution der Effizienz“
FORDERN SIE DAS BUCH KOSTENLOS AN
Diese Profile haben ganz besondere Eigenschaften: Sie bestehen oft aus vorlackiertem Material, das nur extrem geringe Toleranzen erlaubt und gleichzeitig eine absolut makellose Ästhetik erfordert.
Mein Vater hat sich in diesem Bereich sehr dafür eingesetzt, die Beziehungen zu unseren Kunden weiter auszubauen und zu festigen. Wir waren von Beginn an regelmäßig auf Fachmessen präsent, wo wir die Gelegenheit wahrnehmen konnten, unsere Kunden persönlich zu treffen und ihre technischen Fragestellungen und Herausforderungen gemeinsam zu diskutieren.
Anhand der Erfahrungen, die wir in dieser Zeit gesammelt haben, ließen sich die Hauptanforderungen unserer Kunden in vier eng zusammenhängende Kriterien einteilen. Die vier ermittelten Schlüsselfaktoren sind Effizienz, Produktivität, Flexibilität und Automatisierung.
Das bedeutet, dass alle vier Faktoren für die Bewertung einer Investition zu berücksichtigen sind und die Produktivität als alleiniges Bewertungskriterium somit nicht ausreichend ist!
Wenn die Maschine zum Beispiel nicht flexibel einsatzfähig ist, viele manuelle Eingriffe erfordert, wenn Bedienung und Programmierung kompliziert ist, oder wenn viel Rohmaterial und Energie verschwendet wird, kann dies, anstelle einer Margenverbesserung, sogar eher zu einem Verlust führen!
Beginnen wir mit der Analyse der Effizienz und betrachten wir die positiven Auswirkungen, die eine Effizienzsteigerung auf die weiteren drei Faktoren hat.
Die Effizienz von Produktionsanlagen
Blechverarbeitende Unternehmen sehen sich häufig mit dem Problem der Ineffizienz des Produktionsprozesses konfrontiert. Es gibt verschiedene Typen von Ineffizienz.
Die offensichtlichste Ineffizienz, die sich am leichtesten berechnen lässt, ist die Verschwendung von Rohmaterial.
Insbesondere bei der Produktion mit traditioneller Blechbearbeitung in den klassischen Arbeitsschritten Stanzen, Laserscheiden und Abkanten oder Umformen haben sich die Unternehmen an einen Materialausschuss von bis zu 20% gewöhnt.
Mir ist klar geworden, dass dieser Anteil an Ausschuss von vielen Unternehmen sogar als “ganz normal” für den Prozess angesehen wurde.
Die Materialkosten machen oft bis zu 80% der Produktionskosten aus. Das bedeutet, dass sich jedes Prozent an eingespartem Material direkt auf die Ergebnisse in der Bilanz auswirkt.
Eine weitere Ineffizienz ist durch die Komplexität des Produktionszyklus bedingt.
Oft ist der Produktionsprozess nicht hinreichend optimiert. Es gibt zahlreiche Engpässe, und das Unternehmen ist dazu gezwungen, Lager mit Halbzeugen anzulegen, welche keinerlei Wert für den Kunden aufweisen, jedoch drei weitere, große Probleme verursachen.
Das erste Problem ist die Erhöhung des Materialvolumens im laufenden Produktionsprozess. Dieses steigt oft so stark an, dass es den Wert des Rohmaterials im Lager erreicht.
Das zweite Problem ist der beanspruchte Platz, und das dritte große Problem liegt in dem Erfordernis, dass Produkte physisch bewegt werden müssen und es eigens einer Person für logistische Zwecke (zur Abholung und Positionierung von Lagermaterial) bedarf, die in dieser Zeit für produktive Aufgaben nicht zur Verfügung steht.
Der Nutzen für den Endkunden geht somit gegen Null.
Denken wir an ein Unternehmen, das Blechbearbeitung vom Typ Jobshop durchführt. Das Material wird gestanzt und die gestanzten Teile werden gestapelt, um dann zur Biegemaschine oder zum Biegeautomaten weiterbefördert zu werden.
Hier muss das Teil von einer Person oder einem Roboter in die Maschine eingelegt und anschließend das fertige Teil wieder entnommen werden.
Das ist das einfachste Beispiel. Das Problem ist, dass die Berechnung der Kosten für das Zwischenlager der Halbzeuge, für die belegte Fläche und für den Arbeitsaufwand für das Bewegen der Halbzeuge sowie die Berechnung der Materialkosten und die korrekte Zuweisung des Mehrwerts der durchgeführten Bearbeitung derart komplex sind, dass viele Unternehmen schlicht und einfach darauf verzichten.
Ein weiteres sehr interessantes Beispiel für die Ineffizienz der Prozesslogistik betrifft Unternehmen, die Profile für den Trockenbau herstellen.
In diesem Sektor hatte sich Dallan als Lieferant von Profilieranlagen für die Marktführer der Branche in Europa und für viele kleine und mittelständische Betriebe einen Namen gemacht.
Die Herstellung des Profils war in diesem Sektor relativ einfach und viele Unternehmen arbeiteten bereits mit unseren Profiliermaschinen mit variabler Geschwindigkeit im Bereich von 30 bis 120 Meter pro Minute.
Das eigentliche Problem war, dass das Profil alleine nur einen geringen Mehrwert hatte, bis es korrekt verpackt und versandfertig war. Viele Unternehmen machten den Fehler, ihren Produktionszyklus nur auf die Herstellung des Profils zu beschränken, und übersahen dabei, dass die Kosten in den Phasen danach aus folgenden Gründen explodierten:
- Sehr großer Platzbedarf für das Zusammenstellen und Verpacken der Profile
- Große Menge an profiliertem Material ohne Mehrwert, das zwischen den verschiedenen Verpackungsstationen lagert
- Und natürlich der Bedarf an weiteren Arbeitskräften nicht nur für das Verpacken, sondern auch dafür, kleine und große Pakete von einer Verpackungsstation zur nächsten und in das Lager für die fertigen Pakete zu bringen.
Dieser Aspekt ist sehr wichtig, da die automatischen Verpackungsanlagen für Trockenbauprofile den Platzbedarf für die Herstellung deutlich verringern und eine Produktion ausgehend vom Coil direkt bis zum fertig verpackten Produkt ermöglichen.
Wir nennen diese Systeme Coil-to-Pack:
Außerdem arbeiten wir mit vielen Unternehmen, die Rollladenpanzer aus Aluminium mit ausgeschäumten Lamellen herstellen. In diesem Marktsegment war Dallen anerkannter Weltmarktführer und belieferte die wichtigsten Hersteller in Europa, Südamerika, Russland und China.
Unsere Kunden fertigten hauptsächlich Rollladenpanzer aus sechs Meter langen Stangen, die dann an andere Firmen weiterverkauft und von diesen nach Maß zugeschnitten und für die Konfektionierung der fertigen Rollladenbehänge verwendet wurden.
Andere Kunden führten das Zuschneiden der Stangen und das Konfektionieren der fertigen Rollladenbehänge intern mit Standalone-Maschinen durch.
Beide Systeme führten jedoch signifikante Ineffizienzen in den Prozess ein, der vom Coil bis zum Endprodukt führte.
Das erste Problem war das Verarbeiten von Stangen, die nach Maß zugeschnitten werden mussten, wobei immer ein Verschnitt entstand, der je nach Abmessungen des Rollladenpanzers im Bereich von 5% bis 12% lag. Alleine die Kosten für das Aluminium und den PU-Schaum lagen bei zigtausend Euro für den Verschnitt. Hier gab es also viel Einsparungspotential!
Das zweite Problem waren die Kosten für das Stangenlager, in dem Profile mit unterschiedlichen Abmessungen, mit Stanzungen und ohne Stanzungen und in unterschiedlichen Farben und Oberflächen gelagert wurden. Dieser Lagerbestand bedeutete eine sehr hohe Kapitalbindung.
Die dritte Ineffizienz ergab sich aus der Notwendigkeit, die Stangen aus dem Lager zu den Arbeitsstationen zu bringen. Dafür waren Arbeitskräfte, Ausrüstung und sehr komplizierte Manöver erforderlich, sodass konstant die Gefahr bestand, die Oberflächen der vorlackierten und vorgefertigten Profile zu beschädigen.
Die modernen automatischen Fertigungsanlagen erlauben auch hier die direkte Herstellung ausgehend vom Coil bis zum montagefertigen Rollladenbehang, und das ohne Materialausschuss.
Wir nennen diese Systeme Coil-to-Window:
Jean Germanaz, technischer Leiter der französischen Gruppe Stella, die insgesamt mit 12 Coil-to-Window Fertigungsanlagen von Dallan arbeitet, erläutert das Potential dieses Produktionssystems:
«Dallan und Profalux arbeiten seit mehr als zwanzig Jahren zusammen, um es genau zu sagen, seit 1999.
Damals arbeitete Profalux mit einer deutschen Maschine, die mittlerweile in die Jahre gekommen war, um ein flaches Lamellenprofil mit einer Höhe von 40 mm herzustellen.
Wir wollten aber das Profil fertigen, das zum meistverkauften Profil der Gruppe Stella geworden war, nämlich ein gewölbtes Lamellenprofil mit einer Höhe von 39 mm. Damals standen wir in engem Kontakt mit dem Ingenieur Dallan, dem Vater von Andrea, der zu dieser Zeit sein Studium mit einem Studienaufenthalt in Deutschland abschloss.
Die Firma La Toulousaine, die zu unserer Gruppe gehörte, hatte bereits einige Maschinen von Dallan.
Vor Einführung der automatischen Fertigungsanlage von Dallan wurden für die Produktion der Rollladenbehänge Profile mit einer Länge von ca. 6 Metern verarbeitet, die wir bei einem Hersteller aus Europa kauften. Es gab Lamellen in verschiedenen Farben, mit und ohne Löcher. Diese Lamellen mussten in entsprechenden Regalen gelagert und dann nach Maß zugeschnitten werden, was mit einem relativ großen Verschnitt verbunden war. Das Zusammensetzen der Lamellen zum Rollladenpanzer erfolgte auf halbautomatischen Maschinen und die Lamellen wurden mit Arretierungen aus Plastik verbunden.
Die erste Maschine war keine “full Dallan” Maschine, sie produzierte nur das ausgeschäumte Profil und führte den Zuschnitt des Profils durch. Die einzelnen Lamellen wurden dann in einem weiteren Schritt auf einer Sondermaschine verbunden, und zwar noch mit Arretierungen aus Plastik! Die größten Schwierigkeiten lagen damals im Softwarebereich. Nach und nach begannen die Maschinen, mit Dateien und Joblisten zu arbeiten, die von unserem internen ERP-System bereitgestellt wurden.
Was fehlte, war die Kommunikation von Maschinen unterschiedlicher Hersteller untereinander und das war keine leichte Aufgabe.
Für diese Produktionen bieten die Technologien von Dallan zahlreiche Vorteile:
- Auf einer Länge von 45 Metern erfolgt die Fertigung ausgehend vom Rohmaterial-Coil bis zum fertigen Rollladenpanzer, also bis zum montagefertigen Endprodukt.
- Die Produktion des Rollladenpanzers dauert 3 bis 10 Minuten, je nach Größe.
- Es gibt kein Zwischenlager zwischen Coil und fertigem Rollladenpanzer.
- Der Ausschuss ist extrem gering (weniger als 3%) und es gibt sehr interessante Lösungen, um den Materialausschuss noch weiter zu reduzieren.
- Ein einziger Bediener kann bis zu 450 m2 pro Tag produzieren.
- Dallan bietet bedeutende Innovationen, wie das seitliche Verbinden des Rollladenbehangs mit einer mechanischen Bearbeitung, um das Verschieben der Lamellen in Querrichtung zu vermeiden.
Dallan ist sehr effizient auf andere spezifische Anfragen von uns eingegangen, wie zum Beispiel dem Hinzufügen kleiner Plastikschrauben an der Seite des Profils, und hat auch weitere Anpassungen durchgeführt:
- Haspeln mit vertikaler Achse, die eine Verarbeitung der Coils direkt von der Palette erlauben, auf der sie geliefert werden.
- Schallisolierte Kabine zur Reduzierung des Lärmpegels.
- Mit den Lösungen konnten wir die Sicherheit unserer Produktion erhöhen.
- Und wir konnten die Verwaltung und die Qualität des PU-Schaums verbessern.
Zur Gruppe Stella France gehören die Unternehmen Profalux, Eveno, La Toulousaine, Flip und Sofermi. Insgesamt haben wir 17 Fertigungslinien im Einsatz, einschließlich 3 für Rohre und 2 für Rollläden sowie vier neue Linien wurden von uns bereits in Auftrag gegeben.
Dallan ist mit Sicherheit der Lieferant der Gruppe, zu dem die engste Bindung besteht.»
Kontaktieren Sie unsere Ingenieure HIER!
Andrea Dallan
CEO – Dallan Spa