Wie Sie beim Profilieren maximale Produktivität erreichen
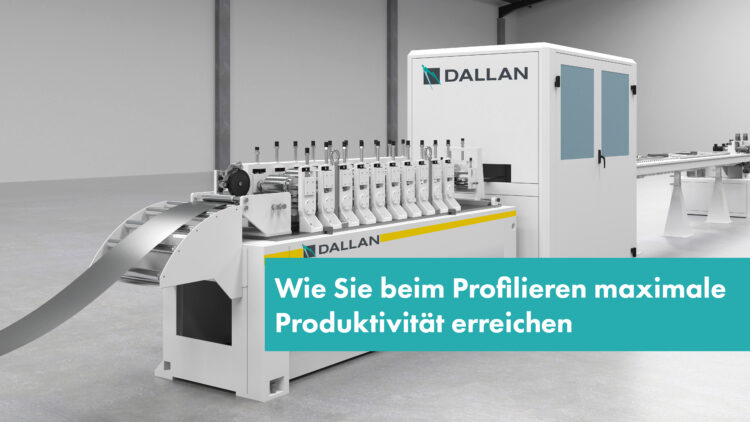
Wenn uns ein Unternehmen für ein neues Projekt kontaktierte, war das oft das einzig wirkliche Problem, mit dem ich konfrontiert wurde.
Lassen Sie mich das erklären.
Entnommen aus dem Buch „Die Revolution der Effizienz“
FORDERN SIE DAS BUCH KOSTENLOS AN
Der Kunde wollte ein Profil einführen oder ein System aus Profilen und Produkten, und war deshalb auf der Suche nach einem Fertigungssystem, mit dem sich diese Produkte mit einer bestimmten Produktivität und unter Optimierung der Kapitalrentabilität herstellen ließen.
Wie wir bereits gesehen haben, ist die Produktivität nur einer der vier Faktoren für die Beurteilung einer Investition.
Ich bekam oft stapelweise Zeichnungen des Kunden, für die wir die Machbarkeit und die Zykluszeit prüfen sollten. Tatsächlich war es üblich, die Anlagen verschiedener Hersteller in erster Linie anhand der Produktivität zu vergleichen.
Aber welchen Sinn hatte es, ein Werkstück schnell zu produzieren, wenn der Zeitaufwand für das Beladen und Entladen der Maschine, das Umstellen der Produktion, die Bewegungen und das Verpacken viel größer war? Um eine Lösung für dieses Problem zu finden, müssen in Wirklichkeit auch viele andere Faktoren berücksichtigt werden, angefangen vom Gesamtprozess und vom Produktsortiment.
Langsam verstand ich, welche Fragen gestellt werden mussten, von der Frage nach der Chargengröße über die Produktionssteuerung vor und nach der Maschine bis zur Häufigkeit, mit der die Produktion umgestellt wird.
Der Produktivität stand oft oder sogar praktisch immer die Flexibilität entgegen, die der Prozess erforderlich machte.
Im Blechbearbeitungsbereich gab es im Wesentlichen zwei Produktionssysteme, und zwar die Fertigung ausgehend von der Blechtafel mit Stanzmaschinen mit NC-Steuerung (für geringe Stückzahlen und hohe Flexibilität) und die Fertigung ausgehend vom Coil mit getakteten Pressen und Stanzwerkzeugen (für hohe Stückzahlen, aber mit geringer Flexibilität).
Die Einführung der parametrischen Coil-Stanzanlagen brachte sehr große Vorteile im Hinblick auf die Rohmaterialeinsparung mit sich und ermöglichte gleichzeitig eine extreme Steigerung der Produktivität und Flexibilität, wie wir am Beispiel von Giovanni Maffei bereits gesehen haben.
Das Wegfallen der Belade- und Entladezeiten und der Bewegungen der Werkstücke und die Verbesserung der Logistik waren Faktoren, die in die Bilanz der Produktivität einflossen, wobei gleichzeitig eine Flexibilität gewährleistet wurde, die für ein System mit Presse und getakteten festen Stanzwerkzeugen unerreichbar ist.
Im Gegenteil, viele Pressen arbeiteten zwar im Fließbetrieb, die Umstellung der Produktion war aber mit einem enormen Zeitaufwand verbunden, im Gegensatz zu den Coil-Stanzmaschinen, bei denen die Rüstzeiten gegen Null gehen. Und Anpassungen der Stanzwerkzeuge, um zum Beispiel die Position einer Stanzung zu ändern, waren extrem teuer!
Im Kapitel, das sich mit der Flexibilität befasst, werden wir noch sehen, wie mit der Einführung der Laserschneidmaschine als unabhängiges Modul auf einen Schlag sowohl die Flexibilität als auch die Produktivität gesteigert werden können, da es sich um die erste und einzige Maschine weltweit handelt, die das Stanzen und das Laserschneiden gleichzeitig durchführt.
Produktivität und Automatisierung: Coil to Pack und Coil to Box
Im Bereich der Profilierung war das Profil für die Kunden oft das Endprodukt der Maschinen, aber in vielen Fällen mussten die Profile zuerst noch unter Berücksichtigung der jeweiligen Anforderungen des Absatzmarktes verpackt werden, bevor sie verkauft werden konnten.
Die ersten Hochgeschwindigkeitsanlagen für die Profilierung, die wir gebaut haben, waren die Profilieranlagen für Trockenbauprofile. Sie wurden zu einem der wichtigsten Produkte von Dallan und sind es heute noch
Die Fertigungsgeschwindigkeit der Anlagen auf über 100 Meter pro Minute zu erhöhen, war mit unserem Know-how im Dünnblechbereich relativ einfach. Das wirkliche Problem war das Handling der Menge von Profile, die mit einer Geschwindigkeit von einem Kilometer in weniger als neun Minuten aus der Maschine kamen.
Anfang 2000 erkannten wir die Probleme der Kunden und die Notwendigkeit, eine geeignete Automatisierung zu entwickeln. Für den Trockenbau werden C- oder U-Profile verwendet, die zu den Ständerwerken zusammengefügt werden, in die dann die Gipskartonplatten als Wände oder abgehängte Decken eingesetzt werden.
Das Problem ist, dass die Profile jeweils paarweise sortiert und in unterschiedlicher Reihenfolge zu kleinen oder großen Paketen zusammengefasst werden müssen, je nach Profiltyp und Markt. Es wird deshalb ein enormes Volumen an Profilen generiert, die beim Verpacken und Lagern gehandhabt werden müssen.
Uns wurde klar, dass die damaligen Verpackungssysteme einen zu hohen Personalbedarf hatten und aufgrund der Produktgröße ein großes Chaos in der Produktionsabteilung verursachten. Es war praktisch unmöglich, die Kontrolle über die Produktionszeiten und Produktionskosten zu behalten.
1997 begannen wir deshalb mit der Einführung einer Teilautomatisierung in den Prozess, die sich zunächst auf die Automatisierung vom Zusammenfassen der kleinen Pakete beschränkte. 2002 war die Automatisierung des Systems abgeschlossen, die Profile wurden jetzt direkt in der Anlage zusammengestellt und das kleine Profilpaket gebildet. Der Arbeitsschritt des Profilierungsprozesses, der sich am meisten wiederholte und sowohl geistig als auch körperlich am anstrengendsten war, wurde jetzt von der Anlage übernommen, die wir heute als Coil-to-Pack bezeichnen.
Im Bereich der abgehängten Decken sind es zum Beispiel die T-Bar-Profile, die einen hohen Automatisierungsgrad erforderlich machen.
Aus diesen Profilen wird die Unterkonstruktion gebildet, die dann mit 60×60 cm oder 60×120 cm Gipskartonplatten beplankt wird. Diese Art der abgehängten Decke gibt es weltweit.
Die Nachfrage war sehr groß und die Kunden verlangten nach immer schnelleren Maschinen, die in der Lage waren, das Profil zu produzieren, die Qualitätskontrolle durchzuführen und die Profile dann direkt in Kartons zu verpacken, und das alles mit einer Produktionsgeschwindigkeit von mehr als einhundert Meter Profil pro Minute.
Wir nannten diese Systeme Coil-to-Box und sind bis heute das erste und einzige Unternehmen, das komplette Anlagen für die Produktion und Verpackung von T-Bar-Profilen liefert. In einem der Kapitel, die sich mit den Anwendungen befassen, werden diese Systeme noch ausführlich beschrieben.
Und auch in diesem Fall lässt sich eine hohe Produktivität nur mit einer entsprechenden Automatisierung für die verschiedenen Profiltypen erreichen.
Das T-Bar-System besteht aus drei Profiltypen. Das erst ist das Grundprofil (auch CD-Deckenprofil oder Hauptschiene) und bildet die Unterkonstruktion, an der alle anderen Profile befestigt werden. Dieses Grundprofil wird mit Schnellabhängern an der Decke befestigt und ist länger als drei Meter.
Dann gibt es noch zwei Tragprofile (auch CD-Deckenprofil oder Querschiene) mit einer Länge von 600 mm oder 1200 mm, die am Grundprofil und aneinander befestigt werden.
Für eine abgehängte Decke sind in der Regel 25% der erforderlichen Profile Grundprofile, 25% Tragprofile mit einer Länge von 600 mm und 50% Tragprofile mit einer Länge von 1200 mm.
Es muss also von der Gesamtmenge der Profile pro Jahr ausgegangen werden und in diesen Fällen werden Mengen von zig Millionen Metern pro Jahr erreicht. Bei diesen Mengen besteht die Lösung darin, parallel zur Anlage, auf der das Grundprofil produziert wird, mehrere Anlagen laufen zu lassen, auf denen die Trägerprofile produziert werden.
Wenn der Kunde mit Systemen mit geringer Produktivität arbeitet, schlagen wir zunächst halbautomatische Verpackungssysteme vor, wo die Qualitätskontrolle der Profile und das Verschließen der Kartons mit den Profilen von einem Mitarbeiter durchgeführt werden.
Mit folgendem QR-Code kann ein Video aufgerufen werden, das eine halbautomatische Verpackungsanlage für Grundprofile zeigt:
Wie wir noch sehen werden, ermöglicht die Coil-to-Box Lösung bei Systemen, die höhere Stückzahlen produzieren, eine Fließfertigung ausgehend vom Rohmaterial-Coil bis zum kontrollierten, in Kartons verpackten und palettierten Produkt. Diese Anlagen verschlingen in kürzester Zeit zig Tonnen Stahl und die Aufgabe des Bedieners besteht in diesem Fall in der Überwachung der Anlage und natürlich in der Bereitstellung der Rohmaterialien (Coils mit Stahlblech und Karton) und dem Entladen der Paletten mit den Kartons, die das Endprodukt enthalten.
Möchten Sie mehr über automatische Hochgeschwindigkeits-Rollformsysteme erfahren?
Kontaktieren Sie unsere Ingenieure HIER!
Andrea Dallan
CEO – Dallan Spa