Lieferkette und Kosten für Rohstoffe: Was kann man von der Blockade des Suezkanals lernen
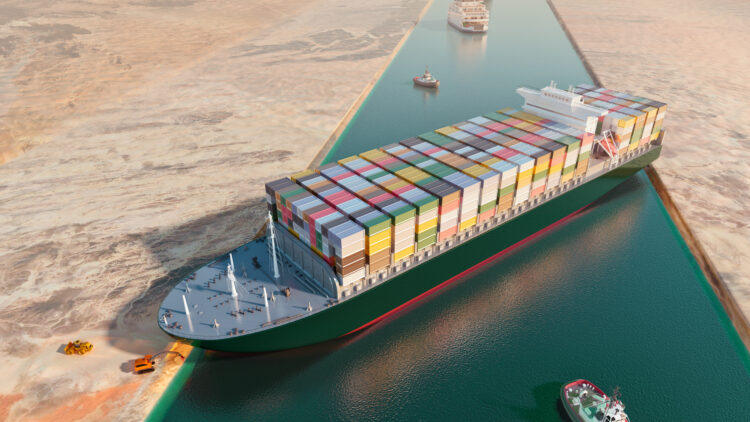
Der Vorfall ist allen bekannt: Das Frachtschiff Ever Given, das am 23. März dieses Jahres auf der Fahrt durch den Suezkanal in Richtung Mittelmeer zum Stillstand kam, hat mehr als 380 Schiffe blockiert und Frachtlieferungen erheblich verzögert, was Schäden in zweistelliger Milliardenhöhe verursacht hat.
Um diese Blockade zu umgehen und nicht im Golf von Suez warten zu müssen, haben sich viele Frachter dazu entschlossen, umzukehren und sich nach Süden zum Kap der Guten Hoffnung zu begeben, was jedoch ihre Fahrt zu den wichtigsten Häfen Europas um etwa 29 Tage verlängerte und mit höheren Risiken verbunden war.
Zweifelsohne hat dieser Vorfall eine wichtige Frage in Bezug auf die Infrastruktur und die Kommunikationswege für den Handel aufgeworfen, die leider beide im neunzehnten Jahrhundert stecken geblieben sind, als der Suezkanal und kurz darauf sein amerikanisches Gegenstück in Panama entstanden.
Zwei bedeutende technische und strategische Bauwerke, an denen unter anderem – um die Weitsicht und den Eifer jener Zeit zu verstehen – auch Gustav Eiffel beteiligt war, der einige Jahre später die Fertigstellung des nach ihm benannten Turms und Symbols von Paris erleben sollte.
Glücklicherweise konnte das Frachtschiff in der Nacht vom 28. auf den 29. März befreit werden, sodass der Weg endlich frei war.
Aber die Frage bleibt: Kann Ihre Lieferkette das Risiko eines drei- bis vierwöchigen Stillstands in Kauf nehmen?
Vor allem durch Amazon haben wir uns daran gewöhnt: Ich klicke, ich bezahle, und am nächsten Tag habe ich das Paket bei mir zu Hause. Und wenn es zu Verzögerungen von ein paar Tagen kommen sollte, macht das auch nichts.
Was aber, wenn diese Lieferung Bauteile enthält, die für Ihre Produktion wichtig sind? Was, wenn Sie aufgrund dieser Verzögerung gezwungen wären, ganze Linien über mehrere Wochen zu stoppen, ohne mit Ihrer Arbeit voranzukommen – und das nur, weil Sie nicht genügend Lagerbestände aufgebaut haben oder Ihnen Lieferanten in Ihrer Nähe fehlen?
Da bleibt nichts als zu warten und zu hoffen.
Das eigentliche Problem ist jedoch Folgendes: Dieser Vorfall hat gezeigt, wie furchtbar anfällig die globale Lieferkette ist.
Es stimmt, dass eine der häufigsten Strategien zur Aufrechterhaltung einer hohen Liquidität darin besteht, die Bestände zu reduzieren. Dennoch müssen wir uns vergewissern können, dass unsere Unternehmen auch in Notfallsituationen oder bei Lieferengpässen betriebsbereit sind und produzieren können.
Sicherlich hat dieser Unfall die Grenzen der Globalisierung aufgezeigt, und wie ich bereits in meinem Artikel über Re-Shoring (den Sie HIER lesen können) erwähnte, haben Europa und Nordamerika einen strategischen Fehler begangen, indem sie einen zu großen Teil ihrer Produktion in geografisch weit entfernte Länder ausgelagert haben.
Das Know-how, die Produktion und wichtige Zulieferer im eigenen Land zu behalten, hat sich während der Pandemie 2020 als großer Vorteil erwiesen, und als ob wir es nötig gehabt hätten, hat die Blockade des Suezkanals dies noch einmal bestätigt.
Ich erinnere mich, wie in den 1990er Jahren und bis 2015 das „Mantra“ der Informations- und Industrieverbände lautete: „Globalisierung ist gut und richtig“.
Vielleicht ist es vor allem im Lichte der Vorkommnisse an der Zeit, uns einige Gedanken zu machen.
Die Verlagerung der Produktion in „Schwellenländer“, um von den niedrigen Lohnkosten zu profitieren, konnte in jenen Jahren noch funktionieren. Das Problem ist jedoch, dass sich diese Länder in der Zwischenzeit zu wahren Wirtschaftsmächten entwickelt haben.
Denken Sie kurz darüber nach: Während Europa bei dem Versuch, sich von dieser Geißel zu befreien, in den letzten Wochen noch damit beschäftigt war, sich um die wichtige Frage der Impfstoffproduktion und -verteilung zu kümmern, befindet sich Asien im vollsten Wirtschaftswachstum – und zwar so sehr, dass zur Zeit der Großteil aller verkehrenden Frachtschiffe für den Warentransport rund um Asien und im Pazifik konzentriert sind.
Die Situation hat sich im wahrsten Sinne des Wortes auf den Kopf gestellt: Die traditionell als „industrialisiert“ geltenden Länder sind immer noch im Drama der Pandemie gefangen und können nur noch zuschauen, wie sich „Ex-Schwellenländer“ von Lieferanten zu echten Konkurrenten entwickeln. Und das auch im Hinblick auf den Zugang zu Rohstoffen, deren Kosten weiterhin dramatisch ansteigen.
Als Antwort auf all dies denken wir in Europa immer noch über die Schließung von Stahlwerken nach, in der Überzeugung, dass die „Verlagerung der umweltschädlichen Produktion in weiter entfernte Gebiete“ das Allheilmittel für alle Übel ist. Ich denke jedoch, dass wir in Wirklichkeit in die Modernisierung dieser Stahlwerke investieren müssen, um sie nachhaltiger und weniger umweltschädlich zu machen.
Bedenken Sie Folgendes: Von den 1850 Millionen Tonnen Rohstahl, die 2019 weltweit produziert wurden, kommen 53 % aus China, während Europa und die NAFTA-Länder zusammen nur 14,9 % ausmachen.
Wenn wir darüber nachdenken, von welcher strategischen Bedeutung ein Rohstoff wie Stahl ist, der für unsere Infrastrukturen, das Bauwesen und die Automobilindustrie unverzichtbar ist, verstehen wir, dass diese mageren 14,9% eine viel zu geringe Menge darstellen und absolut nicht zufriedenstellend sind!
Ich gebe Ihnen ein Beispiel als Anlagenhersteller. Wussten Sie, dass die Maschinen, die wir nach Asien und insbesondere China verkaufen, zu den automatisiertesten Maschinen gehören, die wir entwickeln?
„Wie ist das möglich?“ werden Sie sich vielleicht fragen. „Sind das nicht die Länder der billigen Arbeitskräfte?“
Nun, in Wirklichkeit nicht mehr.
Heutzutage steigen die Arbeitskosten auch in diesen Ländern und die Unternehmen beginnen mit Voraussicht und strukturierter Planung sich an diese Entwicklung anzupassen.
Vielleicht sind Sie sich dessen nicht bewusst, aber dieser Trend ist einer der ausschlaggebenden Aspekte, die Deutschland im Jahr 2013 dazu veranlassten, als erstes Land den Plan zur Automatisierung 4.0 einzuführen.
Offshoring, also die Verlagerung von Know-how und Wissen außerhalb Europas, war ein Prozess, der bis zur Übernahme der deutschen Kuka (ja, richtig, die mit den Robotern!) durch den chinesischen Konzern Midea im Jahr 2016 anhielt.
Gerade die Industrie 4.0 zeigt uns, dass es eine Alternative zur Verlagerung gibt, und zwar die intelligente Prozessautomatisierung.
Dadurch werden die Arbeitskosten zu einer weniger wichtigen Variable innerhalb der Gesamtproduktionskosten. Außerdem erweist es sich auf strategischer Ebene zunehmend als kluge Entscheidung, unser Know-how und unsere Technologie „in der Nähe“ zu behalten.
Hier also meine Überlegungen.
Erstens.
Automatisierung in unsere Unternehmen einzuführen bedeutet, dass wir mittel- und vor allem langfristig viel wettbewerbsfähiger auf dem Markt werden und sicherlich auch attraktiver für Kunden in der Nähe.
Zweitens.
Wenn Sie innerhalb Ihrer Lieferkette auf Lieferanten zurückgreifen können, die für die Verbesserung und die effizientere Gestaltung der eigenen Prozesse auf Automatisierung und Industrie 4.0 setzen, wird Ihre Lieferkette automatisch sicherer und bestimmte Ereignisse, wie z. B. der Vorfall des Frachtschiffs Ever-Given, werden für Ihr Unternehmen deutlich weniger relevant sein.
Fortschrittliche Produktionssysteme sind in der Tat eine der neuen 4.0-Technologien, die von Boston Consulting genannt wurden, und folgende Information ich gebe Ihnen vorausblickend schon jetzt: Diesen Sommer wird mein neues Buch erscheinen, das sich mit Industrie 4.0, Fortschrittlichen Produktionssystemen und der Entwicklung von Dünnblechprodukten beschäftigt – ein intelligenter Weg, um hochwertige Produkte mit weniger Rohmaterial herzustellen.
Der Titel? Think Thin.
Es ist nicht in Buchhandlungen erhältlich, sondern nur bei Dallan S.p.A.
Reservieren Sie schon jetzt Ihr Exemplar und schreiben Sie uns auf [email protected]
Andrea Dallan
CEO – Dallan Spa