Flexibilidad en las líneas de conformado de chapa: el sistema Combi para estampación
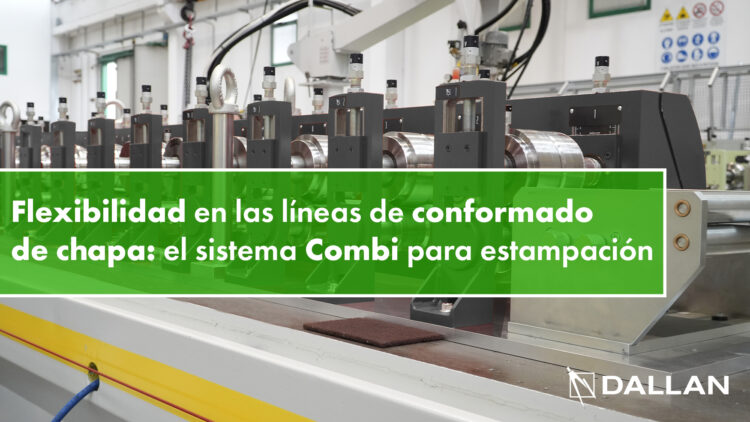
Una vez que constatamos las ventajas del sistema Combi para las series de rodillos, aplicamos el mismo concepto a los grupos de matrices que se instalan antes o después de las perfiladoras.
Cuando se ha moldeado un perfil, a veces es necesario completar el trabajo con la ayuda de unidades hidráulicas y matrices especiales para embutición o aperturas especiales, que no se puede realizar antes del perfilado.
Por eso nació el grupo Combi electrohidráulico. Se trata de una placa de acero en la que se montan:
Unidades hidráulicas
- Matrices
- Sistemas de lubrificación
- Sistemas de extracción motorizados
- Unidades neumáticas
- Sistemas de inserción de accesorios
Extraído del libro «La Revolución de la Eficiencia»
SOLICITE EL LIBRO GRATIS
Todos estos elementos se usan para un tipo de perfil específico. En la placa del Combi, también se montan:
- Los conductos hidráulicos de fijación rápida
- Los conductos neumáticos de fijación rápida
- Los conductos eléctricos con conectores de fijación rápida
Durante un cambio de perfil, la placa del Combi se desconecta, se levanta con un puente grúa y se deposita a un lado.
Después se reemplaza por la placa que incluye todos los matrices ya instalados y regulados para el siguiente perfil, ahorrando horas de trabajo en la instalación de las matrices, las regulaciones y las pruebas.
También la placa tiene dispositivos de centrado especiales para ponerse rápidamente en posición.
En resumen:
- Se pueden instalar varios grupos Combi electrohidráulicos fuera de máquina en tiempo enmascarado
- Se pueden tener varias máquinas que utilicen los mismos Combi para aumentar la productividad y la fiabilidad, y reducir la necesidad de cambiar el producto hasta eliminarla
- Los Combi permiten renovar la línea cuando los sistemas tienen más de veinte años
La filosofía SMED que forma parte de las herramientas de la Lean Production propone un ideal de perfección al que hay que aspirar puntualmente, pero también con el paso del tiempo, añadiendo grupos Combi y equipamiento con el fin de simplificar y acelerar cada vez más el cambio de herramientas, siempre que la máquina esté pensada y diseñada desde este punto de vista.
Así resolvió su problema de flexibilidad la empresa Roto Okna, que forma parte del grupo alemán Roto, fabricante de ventanas para techos. Dice Arkadiusz Guz, responsable de producción:
“ En 2013, Roto producía unos 11.000 elementos de ventana al día, trabajando en dos turnos.
Nuestro proceso productivo era muy complejo y requería mucho tiempo. Se realizaba en las siguientes etapas:
- El material se cortaba longitudinal y transversalmente con una bobina
- Se ponía en un palé
- Se transportaba a la estación de corte con la asistencia del operador
- Después se transportaban las piezas a la estación de plegado en la prensa mecánica
- También aquí se hacía el plegado en matrices especiales con la asistencia del operador
Este tipo de procesos era totalmente ineficiente y requería tres operadores cualificados para cada turno.
En 2014, el objetivo del consejo de administración era ambicioso: encontrar y activar un proceso que permitiese reducir el número de pasos de 3 a 1, sin aumentar el tiempo de preparación de la máquina. Este es el problema que le presentamos a Dallan cuando nos vimos por primera vez.
Entre sus tecnologías, Dallan ya tenía una solución totalmente preparada. Se trata de una línea de punzonado flexible y perfilado Combi, que incluye:
- Devanadora
- Enderezadora
- Prensa de punzonado
- Perfiladora con diferentes equipamientos
- Tabla de descarga
Esta línea ofrece una importante ventaja: el sistema de cambio rápido de los rodillos y las matrices, instalados en grupos en bases de aluminio o acero (Combi). En nuestro caso, el tiempo requerido para el cambio era de 20 minutos con la intervención de dos operadores.
La solución propuesta por Dallan nos permitió reducir el número de operadores necesarios para la producción de 3 a 1, manteniendo el tiempo de cambio de perfil en 20 minutos.
Otro aspecto muy positivo de esta solución es la posibilidad de automatizar el proceso de recepción y paletización de las piezas. Esta será nuestra próxima etapa con vistas a seguir mejorando continuamente”
Arkadiusz Guz
Extraído del libro «La Revolución de la Eficiencia»
SOLICITE EL LIBRO GRATIS
Andrea Dallan
CEO – Dallan Spa