Perfiladoras: cómo garantizar la productividad y el valor de una planta con contratos de mantenimiento y servicio planificados
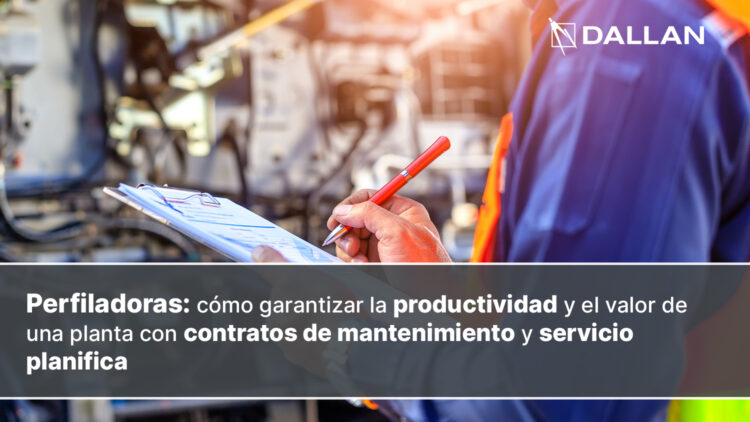
Una vez amortizada la instalación, el coste horario disminuye, naturalmente, pero al atribuir el coste horario a la instalación, siempre aconsejo seguir utilizando el valor calculado al principio por dos motivos.
El primero es la prudencia: la instalación ya se ha rentabilizado, por tanto, calculando el coste con el valor inicial, obtenemos siempre un valor más alto que nos permite contar con un factor de seguridad en los cálculos del coste de la pieza.
El segundo motivo tiene que ver con la conservación del valor de la inversión realizada.
En mi empresa, contamos con numerosas instalaciones de producción: tornos de control numérico, sistemas de fresado, electroerosión y rectificadoras para la producción de herramientas y matrices.
Para garantizar también la fiabilidad de nuestras instalaciones de producción, sabemos que tenemos que seguir invirtiendo en mantenimiento y que los costes de mantenimiento de una instalación, después de los cinco primeros años, pueden aumentar considerablemente.
Por lo general, cuando adquirimos una nueva instalación automatizada, en Dallan sabemos que para garantizar la calidad de la producción resultante y la fiabilidad de la instalación tenemos que tener en cuenta la inversión en varios niveles.
Extraído del libro «La Revolución de la Eficiencia»
SOLICITE EL LIBRO GRATIS
Inversión en la instalación
Se trata de la inversión inicial, durante la cual nos aseguramos una máquina fiable y que produzca con unos estándares de calidad muy altos. La inversión en equipamiento fiable que dura es garantía de rentabilidad. ¡Cuando la instalación se amortiza, el coste horario de la inversión es cero! Lo veremos en los últimos capítulos dedicados al cálculo del coste de producción.
Inversión en la profesionalidad del personal
Hemos hablado del problema de la escasez de personal técnico especializado y de la necesidad de invertir en equipamiento fácil de usar. Es cierto que no hace falta buscar especialistas en perfilado, punzonado o corte láser.
Pero, aunque la instalación automática requiere menos mano de obra, también es importante que los encargados de la línea, los supervisores –o, al menos, los responsables de departamento– sean personas motivadas y cualificadas desde el punto de vista de la gestión.
Cuando tenemos que formar a los técnicos de algún cliente en el uso de las líneas Dallan, a menudo preferimos trabajar con técnicos jóvenes que tienen ganas de implicarse, aunque acaben de terminar sus estudios, en lugar de personal que ya tenga experiencia.
En efecto, las nuevas instalaciones del tipo Industria 4.0 incluyen funciones y tecnología, como la teleasistencia y el control desde la oficina, que requieren curiosidad, flexibilidad y frescura. Unas dotes que encontramos muy a menudo en los jóvenes.
Inversión en las materias primas
Hoy día, el equipamiento cuenta con un nivel de tecnología avanzado. Suele ocurrir que la persona que adquiere las materias primas, trata de optimizar y reducir los costes comprando material de ocasión.
Como ya hemos visto, ese no es el camino correcto.
En efecto:
- Los materiales de ocasión necesitan tiempos de regulación de la máquina muy difíciles de prever. Y prever los tiempos de puesta en marcha de la máquina es FUNDAMENTAL.
- Pero, sobre todo, hay sistemas mucho más eficaces para reducir el coste de la materia prima por pieza producida.
Como, por ejemplo, pasar del trabajo de formato al de bobina o pasar de la producción de persianas a partir de barras a la producción directa a partir de bobina, que nosotros llamamos COIL TO WINDOW.
Esto garantiza una calidad del producto muy alta para el cliente final y un enorme ahorro en las compras, del orden de cientos de miles de euros al año.
Inversión en el mantenimiento programado
Esla cuarta dimensión de la inversión. En efecto, el mantenimiento no es un coste, sino una inversión. Debe ser programado y preventivo para evitar costosas paradas de la máquina en momentos de emergencia.
Las punzonadoras, las perfiladoras y el láser están diseñados para durar décadas, pero hay que tener en cuenta que algunos elementos, como los cojinetes, tornillos de bolas recirculantes, reductores, etc. están sujetos a un desgaste proporcional al uso de la máquina.
Después de los cinco años, es importante prever en el presupuesto un valor para el mantenimiento preventivo, que, por lo general, se lleva a cabo con una visita anual de nuestros técnicos. Durante esta visita, los técnicos realizan los controles y le entregan al cliente una lista de piezas de recambio que aconsejamos conservar para casos de necesidad.
Estas piezas de recambio están disponibles en caso de emergencia o son instaladas por nuestros técnicos durante la visita del año siguiente.
De este modo, cada cliente se puede crear un pequeño almacenamiento de piezas de recambio para la instalación, que garantice fiabilidad y costes mínimos para reparar las posibles averías.
Esto es muy importante.
Estos costes –con instalaciones que pueden trabajar hasta 24 horas al día– tendrían que ser constantes a lo largo de los años. ¡Si no es el caso, debería ser motivo de alarma para el Empresario!
Algunas empresas han infravalorado la importancia del mantenimiento preventivo y, en algunos casos, este error puede salir caro.
En los años noventa, una de nuestras empresas clientes había adquirido diez perfiladoras y cada una de las máquinas producía –y sigue produciendo– un componente que se utiliza en una línea de producción y ensamblaje.
Las máquinas siempre están equipadas con el mismo perfil, por tanto, la línea de ensamblaje trabaja en lógica “Pull” donde la línea de abajo exige las piezas a las máquinas una en una.
Un excelente sistema de producción, que ha funcionado durante casi treinta años de manera impecable.
En los últimos años, habíamos observado una reducción de la compra de recambios y ya no recibíamos pedidos de mantenimiento preventivo. Mientras tanto, los componentes electrónicos de las máquinas se habían quedado obsoletos, igual que las protecciones y la seguridad.
Cuando la máquina empezó a fallar, se pusieron en contacto con nosotros para hacer un mantenimiento general, pero, teniendo en cuenta el estado de abandono de las instalaciones y los costes de reparación de las líneas, el valor de las intervenciones resultaba muy superior al coste anual de un mantenimiento programado.
Afortunadamente, gracias al sistema Combi, fue posible reutilizar todo el equipamiento y las matrices, además de renovar toda la producción y los sistemas de seguridad, invirtiendo solo en las nuevas bases y los cuadros eléctricos de las líneas.
En la empresa Dallan, para mantener nuestra ventaja competitiva, seguimos invirtiendo en nuevas tecnologías, controles y centros de trabajo más rápidos, fiables y automáticos, que permiten producir con mayor calidad además de reducir los residuos y la energía.
Programamos el cambio de las máquinas cuando superan los veinte años de vida, tratando de mantener la compatibilidad con las herramientas que ya tenemos disponibles y con el equipamiento periférico emplazado en torno a las máquinas.
Igualmente, observamos que nuestros operadores también estaban más motivados al vernos invertir en instalaciones más ergonómicas y fáciles de usar: ¡una importante evolución también para ellos, que son nuestros “escultores del acero”!
Sławomir Sofiński, responsable de la producción y el mantenimiento en Aluprof, explica la forma en que el correcto mantenimiento de las líneas permite garantizar el valor de la inversión y la continuidad de la producción de persianas.
“ Nuestra empresa se fundó en 1997. Antes de conocer Dallan, usábamos una línea de perfilado alemana para producir los perfiles de persiana. En 1998, llegó la primera perfiladora Dallan, seguida de otras ocho líneas, la última instalada en 2020.
Todas las líneas Dallan se fabrican con componentes de empresas líderes, como SKF, Nidec y Rexroth, y todas las máquinas incorporan tecnología muy avanzada. Estamos satisfechos de la evolución de los controles hacia el sistema Beckhoff.
A lo largo de los años, hemos constatado que cada nueva línea incluía siempre mejoras, sobre todo, en las dos últimas máquinas que hemos recibido.
En el caso de algunos componentes, sabemos que es necesario conservar algunos componentes en casa como piezas de recambio. Me gustaría señalar que no existen máquinas que no necesiten mantenimiento.
Para mantener una máquina en buen estado, la primera necesidad es el mantenimiento preventivo. Por ejemplo, en Aluprof, preveo tres tipos de mantenimiento preventivo: el mantenimiento mensual en el que limpiamos y controlamos cuidadosamente la máquina para asegurarnos de que no haya pérdidas de aire o aceite en ninguna parte. Limpiamos la punzonadora y controlamos la fijación de las conexiones mecánicas. Este mantenimiento lo hacemos fuera de las horas de producción, generalmente, el sábado o el domingo. Tenemos listas de verificación de control y este mantenimiento prevé 8 horas de trabajo.
Después está el mantenimiento anual, que se hace a principios de año antes del periodo de temporada alta. Todas las máquinas Dallan se detienen durante tres días y nuestros técnicos controlan, de forma separada, cada parte de la línea: las punzonadoras, centrales hidráulicas, sierras, grupos de roscado, perfiladoras y la devanadora. Nuestros técnicos controlan las condiciones de los árboles y los cabezales, además de cambiar los posibles cojinetes o elementos desgastados.
Realizamos el engrasado según las fichas de mantenimiento y el control de los tornillos de bolas recirculantes. Las primeras perfiladoras incluían una parte de la transmisión en cadena y si esta se aflojaba, la cambiábamos. Hoy día, las transmisiones de las máquinas son totalmente de engranajes.
Por último, está el mantenimiento preventivo. El año pasado, utilizamos nuestro MES interno (Manufacturing Execution System). Este sistema nos ofrece una enorme cantidad de datos y hemos determinado algunos ICP (indicadores clave de rendimiento) para la sección de mantenimiento de nuestra empresa.
Los ICP más importantes conciernen a la función de las líneas. Hemos instalado sensores adicionales en las punzonadoras, que controlan todos los cilindros hidráulicos y el número de operaciones de punzonado realizadas en las persianas. Si alguno de los cuatro sensores no registra señal, toda la línea se detiene y una señal luminosa indica el cilindro que presenta el problema. Esto evita que se produzcan piezas no conformes; antes, al operador se le podía pasar el error y la pieza no conforme se embalaba de todas formas.
El número de punzonados también nos indica el momento en que la matriz se tiene que cambiar. Cuando esta se acerca al fin de su vida útil, aparece una señal de alarma amarilla en el MES y nuestro servicio técnico recibe un SMS que le indica al técnico la herramienta que hay que cambiar.
Esto nos permite hacer un mantenimiento correcto en las matrices antes de que lleguen al final de su vida útil. Podemos rectificarlos y usarlos durante mucho tiempo. Por cada línea, disponemos de dos grupos de matrices para poder cambiarlos en pocos minutos y continuar con la producción.
Nuestro MES calcula además la cantidad de kilómetros de perfil que han pasado en cada grupo combi y, en poco tiempo, también podremos prever en qué momento hay que cambiar algunos rodillos.
En cuanto a la parte eléctrica y electrónica, es muy difícil prever la vida útil de estos componentes, pero nuestro trabajo consiste en mantenerlos en las mejores condiciones posibles. Los sensores ópticos se limpian todos los días. Dos veces al año, se controlan todos los cuadros eléctricos con una cámara térmica. Nuestros técnicos inspeccionan el cuadro eléctrico, las conexiones y, si algunos elementos se calientan de forma anómala, se sustituyen.
Tenemos una excelente relación con el equipo informático de Dallan, que puede hacer operaciones de reparación y de reprogramación en teleservicio a través del módulo PLC a distancia. Hay que prestar especial atención a las máquinas viejas, porque algunos componentes electrónicos se están dejando de producir y es necesario trabajar de forma preventiva con los técnicos de Dallan.
Cuando se trabaja en temporada alta, si se presenta algún problema, necesitamos sistemas de intervención rápida ¡Las Fuerzas Especiales no solo están en el ejército!
Algunos sistemas de automatización integrados en las máquinas están formados por muchas partes pequeñas y hemos procurado equipos completos para guardarlos en el local. De este modo, podemos cambiar en pocos minutos, por ejemplo, un tornillo recirculante o una conexión rápida. Muchas piezas se pueden utilizar en varias líneas y las conservamos en nuestro almacén.
La limpieza regular de las máquinas es muy importante y, todos los fines de semana algunos operadores llevan a cabo una limpieza completa de todas las líneas. Les tengo preparada una lista con los puntos que hay que limpiar con más atención a fin de no tener que recurrir a ningún especialista para este trabajo. La limpieza es esencial para evitar que algunas piezas acumulen polvo, como los ventiladores o los intercambiadores térmicos. Esto permite conservar la eficiencia y el valor de nuestras instalaciones. ”
Sławomir Sofiński
Extraído del libro «La Revolución de la Eficiencia»
SOLICITE EL LIBRO GRATIS
Andrea Dallan
CEO – Dallan Spa