Flexibilidad en las líneas de perfilado: el sistema COMBI para un cambio rápido de herramientas
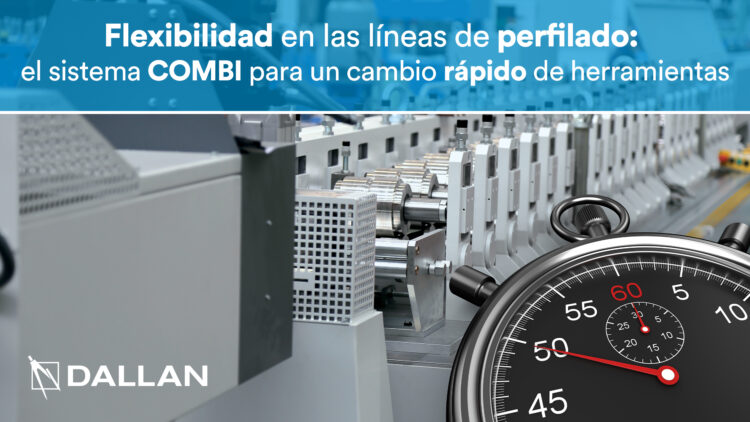
Uno de los instrumentos de la Lean Production es la técnica SMED. Esta técnica concierne a la velocidad de reequipamiento de las líneas productivas y quiere decir “Single Minute Exchange Die”.
El objetivo es hacer el reequipamiento de la línea (con una nueva bobina o una nueva matriz) en menos de diez minutos.
Concretamente, este instrumento responde al problema de la Flexibilidad, pero siempre en una perspectiva de Eficiencia y Productividad.
En las líneas de perfilado, el problema de la productividad vinculada a la flexibilidad se presentaba, por ejemplo, en las líneas de producción de chasis para puertas blindadas.
Extraído del libro «La Revolución de la Eficiencia»
SOLICITE EL LIBRO GRATIS
Las empresas pasaban con frecuencia al perfilado, porque el trabajo a partir de formato alcanzaba una tasa de residuos de material que se podía elevar a más del 20 por ciento.
Pasando al perfilado con instalaciones inadecuadas (por ejemplo, sin punzonadora paramétrica a partir de bobina o sin sistema de cambio rápido Combi), los tiempos de cambio de producto eran tan elevados que el proceso solo resultaba rentable si los lotes cubrían al menos una semana de trabajo.
En la producción de chasis para puertas blindadas, el punzonado paramétrico junto con el sistema de cambio de producción Combi para rodillos y matrices –como vimos en el capítulo anterior– resolvía a la perfección el problema de la flexibilidad. En efecto, era posible producir chasis de tamaños diferentes y llegar al famoso lote uno.
O, como lo llama Giovanni Maffei, la producción “Zero Standard”: esto indica que el sistema está equipado y siempre preparado para fabricar perfiles de diferentes tamaños sin tiempos de preparación y sin que una persona tenga que programar las máquinas.
En el sector de las ventanas, las puertas blindadas y los cortafuegos, cuando la máquina tenía que producir perfiles diferentes, era necesario cambiar de equipamiento. El sistema Combi para rodillos y matrices permitía hacer el cambio en menos de diez minutos para cada grupo y en menos de una hora para todo el conjunto.
Los productores encontraban el mismo problema en el sector de los perfiles para falsos techos, donde las primeras máquinas eran de líneas preparadas para realizar numerosos perfiles y el cambio de rodillos para pasar de un perfil a otro podía durar horas o, incluso, días.
Por eso, para ellos era importante identificar con certeza las soluciones que les permitieran aumentar la productividad y reducir al máximo el tiempo de cambio de equipamiento a menos de una hora o, incluso, a diez minutos.
Como veremos, el sistema Combi para rodillos y matrices presentaba una doble ventaja: aumentaba la productividad – reduciendo el tiempo de cambio de producción– y la flexibilidad de la instalación.
Flexibilidad: el sistema Combi para perfilado
En el perfilado con rodillos, tradicionalmente, los pertenecientes a todo tipo de series se montan en rodillos superpuestos.
Los rodillos se desmontan para pasar de un perfil a otro y el tiempo de cambio de la serie puede ser de horas o, incluso, de un día entero.
Por eso, además de los rodillos motorizados montados en árboles, a menudo se utilizan rodillos periféricos de formación montados en accesorios auxiliares.
Este proceso exigía tiempos de ajuste muy elevados y, por ese motivo, la técnica evolucionó hacia sistemas de distribuidores intercambiables, en los que se instalan grupos de rodillos en estructuras apropiadas.
En general, los distribuidores incluyen grupos de cuatro o seis rodillos y esto es un problema porque:
- hay que montar varios distribuidores para cambiar el producto
- cada distribuidor va conectado a la transmisión que, a menudo, está constituida por varias juntas de cardán.
Seguiría siendo mucho tiempo para cambiar de herramientas, pero el sistema Combi resuelve fácilmente los dos problemas.
El sistema Combi utilizado en las máquinas Dallan es único en su género.
En efecto, los grupos Combi están equipados con los siguientes elementos en una base de aluminio:
- Transmisión con engranajes (de dientes rectos, oblicuos o con sistema de biela-manivela)
- Sistema de lubrificación de la transmisión
- Árboles ya regulados en altura
- Rodillos ya regulados según el espesor adecuado
- Accesorios montados en la placa de aluminio y ya regulados
- Introductor de chapa
- Grupo de enderezado con rodillos
El grupo Combi solo presenta una rueda dentada en el exterior. La base incluye una rueda dentada similar conectada al motor y al reductor.
Cuando el grupo Combi se apoya en la base, se coloca sobre pasadores de alineación especialmente diseñados para ponerse rápidamente en posición y las dos ruedas dentadas se insertan la una en la otra.
En este vídeo, podemos ver la operación de recambio de un grupo Combi:
Las máquinas equipadas con este sistema Combi especial responden, pues, al principio SMED que aconseja la Lean Production (Single Minute Exchange Die) y que está orientado a organizar las máquinas y la producción de modo que el cambio de una herramienta tenga lugar en menos de diez minutos.
El sistema Combi también ofrece otras cuatro importantes ventajas.
- Si contamos con una instalación y varias series de rodillos, son suficientes dos Combi. El primer sistema trabaja en la máquina, mientras que un técnico puede realizar los cambios de rodillos en el segundo Combi, fuera de la máquina, como se suele decir “en tiempo enmascarado”
- Si tenemos un sistema que necesita una gran potencia, en lugar de utilizar un gran motor especial único, cortamos la instalación en dos o tres partes equipadas con grupos Combi motorizados que funcionan de manera independiente, con motores más pequeños y estándares. Además de esto, se pueden modificar las velocidades de las diferentes zonas de la máquina manteniendo el perfil en tracción hasta el final y mejorando aún más el enderezado
- Además, los Combi son instalaciones extremadamente fiables. En más de cuarenta años de actividad, después de haber producido miles de Combi, nunca nos han informado de problema alguno.
Por tanto, los grupos Combi son prácticamente eternos. Con frecuencia, cuando la instalación tiene más de veinte años, las normativas en materia de seguridad han cambiado. A menudo, los componentes electrónicos se quedan obsoletos y ya no hay piezas de recambio disponibles.
De este modo, se puede cambiar solo la base de la perfiladora y de la instalación, además de reutilizar todos los grupos Combi y las series de rodillos ya existentes, porque las nuevas bases son compatibles o se pueden adaptar.
De este modo, puedes tener una instalación nueva y conforme a la normativa con una mínima inversión, ¡solo utilizando el Combi y las matrices ya existentes!
Otro aspecto muy importante.
Cuando se inicia una actividad es normal utilizar una sola base equipada con varios Combi para diferentes perfiles.
Cuando aumenta la demanda de producción, dado que la inversión en equipamiento ya se ha hecho, es posible duplicar la producción invirtiendo simplemente en una base y reutilizando los Combi ya existentes.
Ventajas:
- Se reducen a la mitad los cambios del producto
- Se duplica la fiabilidad de la producción
- ¡Como consecuencia, la producción aumenta en más del doble!
Eros Damilano es el propietario de Damilano, una sociedad de Cuneo especializada en la producción de perfiles por cuenta de terceras personas. Eros le compró a mi padre la primera perfiladora para lamas en 1984 y empezó a producir directamente en su garaje. El lugar era muy pequeño, por eso, los perfiles se descargaban fuera del garaje. ¡Era el propio Eros el que cargaba los perfiles en la furgoneta de entrega!
En la actualidad, posee otras empresas y Damilano cuenta con 20 líneas Dallan en funcionamiento.
Damilano produce internamente los rodillos de sus propias líneas, adaptándose así a las exigencias del mercado. El director de la empresa, Eros Damilano, nos habla de su colaboración con Dallan, sus perfiladoras y sistemas Combi:
“ Actualmente, Damilano Group dispone de 20 líneas de perfilado que producen alrededor de 500 tipos de perfiles, el 70 % de los cuales están basados en los diseños del cliente. Trasformamos alrededor de 1000 toneladas al mes con un equipo de 80 colaboradores.
Por la época en que introdujimos el perfilado para producir falsos techos, los productores de este sector se limitaban a 3 o 4 empresas en Europa. En Italia solo estaba la empresa Hunter Douglas con una sede en Milán y Metal Sadi, en Vicenza; por tanto, el mercado ofrecía grandes oportunidades. Pero, ironías de la suerte, dos empresas compramos la primera perfiladora del ingeniero Dallan que había presentado en el Saie de Boloña: nosotros y Tecnesa con sede en Marene, a solo 20 kilómetros de distancia. ¡Por suerte, pudimos evitar una guerra comercial!
La primera perfiladora se compró en 1984 y la trasladamos desde el taller de Dallan, después de una inspección muy larga, a las 4 de la mañana de un día especialmente lluvioso. La producción de Dallan tenía lugar en una pequeña nave en una zona agrícola y, para poder salir con el camión del fango, tuvimos que llamar a un campesino, amigo del Ingeniero Dallan, que nos sacó con su tractor.
Debido a los escasos recursos económicos y la falta de espacio del momento, la perfiladora se colocó en un garaje. Cuando llegaba el momento de perfilar, abríamos el portón y salíamos a la calle con los perfiles. ¡Si las barras eran muy largas teníamos que aparcar los coches en doble fila para ocultar el problema!
Posteriormente, al considerar que el perfilado era una actividad muy especializada, pero con buenas posibilidades de desarrollo, introduje la producción de perfiles para cartón-yeso que, por entonces, se producían a un ritmo de 10/12 metros por minuto. Ahora la producción es muy rápida, pero luego dejamos el sector para centrarnos en perfiles de más espesor, más complejos y perforados a medida.
La primera punzonadora utilizada para hacer las perforaciones en las bobinas, adquirida en Dallan en 1988, incluía una unidad hidráulica con 5 estaciones, que permitía realizar 5 transformaciones diferentes, pero con posiciones fijas. Poco después, Dallan diseñó la Pxn, una punzonadora flexible a partir de bobina con 20 herramientas móviles, que nos abrió todo un mundo de posibilidades en el punzonado, gracias a su increíble flexibilidad.
La opción de trabajar con bobinas nos permitió cambiar el plegado con prensa en muchos casos, reducir casi a cero los residuos, eliminar la limitación del largo, reducir los costes vinculados a las diferentes perforaciones que se habían hecho en línea casi en tiempo enmascarado.
Otra novedad muy interesante de Dallan, fue construir perfiladoras con los grupos Combi. Gracias a esto, por ejemplo, para la producción de chasis para puertas blindadas de chapa, ¡los diferentes equipamientos iban siempre montados en varios grupos Combi y así podíamos cambiar de producción rápidamente!
Pero cuando producíamos nuestros 500 perfiles a medida, los grupos Combi nos permitían montar los rodillos en los cabezales y fuera de la máquina en tiempo enmascarado. De este modo, redujimos el tiempo del cambio de producción con solo cambiar los grupos y montar las matrices de corte, ¡con un ahorro de alrededor del 60/70 %!”
Eros Damilano
Extraído del libro «La Revolución de la Eficiencia»
SOLICITE EL LIBRO GRATIS
Andrea Dallan
CEO – Dallan Spa