Chaîne d’approvisionnement et coût des matières premières : quel enseignement tirer du blocage du canal de Suez?
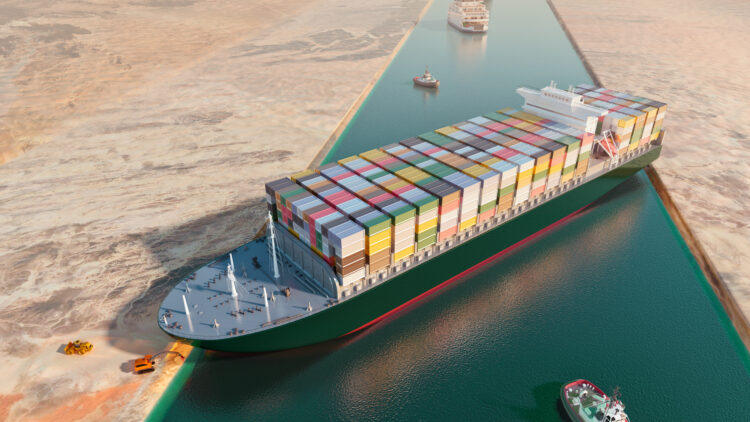
Ce n’est pas nouveau : le porte-conteneurs Ever Given, qui s’est enlisé le 23 mars dernier alors qu’il parcourait le Canal de Suez vers la Méditerranée, a bloqué plus de 380 navires et occasionné d’importants retard de livraisons de marchandises, causant ainsi des pertes de dizaines et de dizaines de milliards de dollars.
Pour éviter les embouteillages et ne pas rester immobilisés dans le Golfe de Suez, de nombreux navires ont décidé de rebrousser chemin et de mettre le cap sur le sud, vers le Cap de Bonne Espérance, prenant ainsi d’énormes risques et rallongeant d’environ 29 jours leur voyage à destination des principaux ports européens.
Cet incident a sans nul doute soulevé des questions concernant les infrastructures et les routes commerciales qui sont restées bloquées – hélas – au 19ème siècle, période où le Canal de Suez a vu le jour ainsi que son équivalent américain à Panama, un peu plus tard.
Deux grands ouvrages d’ingénierie stratégiques qui ont inspiré, entre autres – simplement pour donner une idée de la vision et de la ferveur de cette époque – Gustav Eiffel, qui allait édifier quelques années plus tard la tour devenue le symbole de Paris.
Fort heureusement, dans la nuit du 28 au 29 mars, le navire a été dégagé et remis à flot, libérant enfin la voie de communication.
Mais la question demeure : votre chaîne d’approvisionnement vous permettrait-elle de supporter une mise à l’arrêt de l’entreprise de trois ou quatre semaines ?
Par la faute d’Amazon, principalement, nous nous sommes habitués aux livraisons rapides. Je clique, je paie, et je reçois mon paquet chez moi le lendemain. Si la livraison est retardée de quelques jours, tant pis.
Mais si cette expédition concerne des éléments vitaux pour votre production ? Si ce retard vous obligeait à arrêter des lignes entières pendant des semaines, sans pouvoir agir, uniquement parce que vous n’avez pas créé de stocks suffisants ou parce que vous n’avez pas accès à des fournisseurs plus proches de vous ?
Il ne vous reste plus qu’à attendre et prier.
Voici le véritable problème : cet incident a révélé à quel point la chaîne d’approvisionnement mondiale était fragile.
L’une des stratégies majoritairement adoptées pour garder un niveau élevé de liquidités consiste à réduire les stocks. Mais nous devons être certains de pouvoir maintenir nos entreprises en activité et en capacité de produire, y compris dans des situations d’urgence ou de déficit d’approvisionnement.
Cet incident a mis en évidence les limites de la mondialisation. Comme je l’ai mentionné dans mon article consacré à relocalisation (que vous pouvez retrouver ICI), l’Europe et l’Amérique du Nord ont fait une erreur stratégique en confiant une part trop importante de leur production à des pays géographiquement éloignés.
Le fait de conserver le savoir-faire dans son propre pays, ainsi que la production et les principaux fournisseurs, s’est avéré être un grand avantage durant la pandémie de 2020 et, comme s’il en était encore besoin, le blocage du Canal de Suez nous l’a démontré une seconde fois.
Je me souviens que dans les années 90, et jusqu’en 2015, les médias et les associations industrielles répétaient le même « mantra » : « la mondialisation est bonne et juste ».
Peut-être est-il temps de nous poser des questions, d’autant plus après ce qui vient de se produire.
L’exportation de la production vers des pays « émergents » pour tirer profit du faible coût de la main-d’œuvre pouvait fonctionner durant ces années. Le problème, c’est qu’entre-temps, ces pays ont évolué et sont devenus de véritables puissances économiques.
Réfléchissez-y : ces dernières semaines, alors que l’Europe fait encore face au problème crucial de la production et de la distribution des vaccins pour tenter d’enrayer la pandémie, l’Asie connaît une pleine reprise économique, si bien que la majeure partie des navires de transport de marchandises est concentrée en Asie et dans le Pacifique.
La situation s’est littéralement inversée : les pays dits « industrialisés » sont toujours enlisés dans le drame de la pandémie et regardent impuissants les pays « ex-émergents », qui sont passés du statut de fournisseurs à celui de véritables concurrents, y compris au niveau de l’accès aux matières premières, dont les coûts ne cessent de s’envoler.
En Europe, pour répondre à la situation, nous pensons encore à fermer les usines sidérurgiques, convaincus que le fait de « déplacer au loin » les productions polluantes est le remède à tous les maux. En réalité, je crois qu’il est nécessaire d’investir pour les moderniser, les rendre plus durables et moins polluantes.
Pensez-y : sur les 1 850 millions de tonnes d’acier brut produites dans le monde en 2019, 53 % provenaient de la Chine, contre à peine 14,9 % pour l’Europe et l’ensemble des pays de l’ALENA.
D’un point de vue stratégique, lorsque l’on pense à l’importance d’une matière première comme l’acier, essentiel pour les infrastructures, le bâtiment et l’automobile, on comprend que ce faible pourcentage de 14,9 % est loin d’être satisfaisant !
J’ai une information intéressante à vous transmettre, en tant que producteur d’installations. Saviez-vous que les machines qui nous sont demandées en Asie, et notamment en Chine, figurent parmi les installations les plus automatisées que nous ayons à concevoir ?
« Comment ça ? », vous demanderez-vous, « ce ne sont pas des pays où la main-d’œuvre est bon marché ? »
Ce n’est plus le cas.
Aujourd’hui, ces pays font également face à une augmentation des coûts de main-d’œuvre, et les entreprises protègent leurs arrières de façon anticipée et structurée.
Vous l’ignoriez peut-être, mais cette tendance fait partie des raisons pour lesquelles l’Allemagne a introduit le plan Automation 4.0 dès 2013.
La délocalisation, ou offshoring, contribuait à exporter le savoir-faire et les connaissances hors de l’Europe, et ce processus a continué jusqu’à l’acquisition en 2016 de l’entreprise allemande Kuka (oui, précisément un fabricant de robots !) par le groupe chinois Midea.
L’Industrie 4.0 nous démontre qu’il existe une alternative à la délocalisation, à savoir l’automation intelligente des processus.
Grâce à elle, le coût de la main-d’œuvre devient une variable moins importante sur l’ensemble des coûts de production. De plus, le fait de conserver notre savoir-faire et notre technologie au niveau local s’avère être un choix stratégique bien plus judicieux.
J’aurai donc deux observations à faire.
La première.
L’adoption de l’automation dans nos entreprises renforce significativement notre compétitivité dans le secteur, et à long terme, sur le marché, et nous rend de ce fait plus attractifs pour les clients qui se trouvent proches de nous.
La deuxième.
En faisant appel à des fournisseurs ayant adopté l’automation et l’Industrie 4.0 pour améliorer et renforcer l’efficience de leurs processus, vous disposerez automatiquement d’une chaîne d’approvisionnement plus sûre, et votre production sera beaucoup moins impactée par des évènements tels que l’incident du navire Ever Given.
Les Systèmes Avancés de Production font partie des nouvelles technologies 4.0 identifiés par Boston Consulting, et je vous fais part d’une nouvelle en avant-première : la sortie cet été de mon nouveau livre consacré à l’industrie 4.0, aux systèmes avancés de production et à la conception des produits en tôle fine – une solution intelligente pour réaliser des produits de haute qualité en utilisant moins de matière première.
Le titre ? Think Thin.
Vous ne le trouverez pas dans les librairies, mais uniquement chez Dallan S.p.A.
Commandez votre exemplaire dès aujourd’hui et inscrivez-vous sur [email protected]!
Andrea Dallan
CEO – Dallan Spa