Profileuses et systèmes de production efficaces
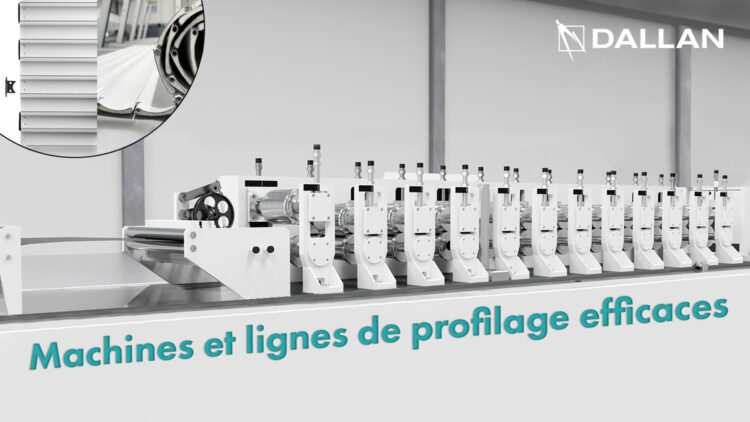
À partir de 2008, outre ces travaux sur les poinçonneuses et le laser, j’ai cherché à améliorer – en collaboration avec mon père – la vente et les conseils relatifs aux systèmes de profilage.
Dallan était reconnue comme le spécialiste incontesté des systèmes de profilage de tôle fine et cette expertise nous a amenés à nous spécialiser ultérieurement dans les secteurs des finitions intérieures et de la protection solaire.
Ces profils présentent des caractéristiques particulières : généralement composés de matériaux prélaqués, ils requièrent des tolérances réduites et doivent offrir un aspect esthétique parfait.
Extrait du livre » La Révolution de l’Efficience »
DEMANDER LE LIVRE GRATUITEMENT
Dans ce secteur, mon père veillait à optimiser ses relations avec la clientèle. Nous participions fréquemment à des salons professionnels, où nous pouvions rencontrer nos clients et nous mettre à l’écoute de leurs difficultés.
Au fil du temps, j’ai pu classer les problèmes principaux qu’ils rencontraient en quatre catégories étroitement liées entre elles : l’Efficience, la Productivité, la Flexibilité et l’Automation.
Concrètement, c’est sur la base de ces quatre critères que doit être évalué l’investissement, la productivité n’étant pas la seule évaluation à prendre en compte !
Par exemple, si une machine n’est pas flexible et nécessite une main-d’oeuvre importante, si son utilisation et sa programmation sont complexes, ou si elle génère un important gaspillage de matière première et d’énergie, elle sera davantage susceptible d’entraîner des pertes qu’une amélioration des marges.
Nous commencerons par l’analyse de l’Efficience et nous verrons en quoi son optimisation apporte systématiquement des améliorations dans les trois autres dimensions.
L’Efficience dans les systèmes de production
Les entreprises du travail de la tôle sont affectées par certaines failles liées au processus de transformation. Ces failles sont de natures diverses.
La plus évidente – et la plus facile à quantifier – concerne le gaspillage de matières premières.
Les cycles de transformation classiques (poinçonnage, découpe au laser et pliage ou panneautage), notamment pour un travail de la tôle à partir de feuilles, ont habitué les entreprises à des taux de rebus pouvant atteindre 20 %.
J’observais que de nombreuses entreprises considéraient ce taux de rebus comme étant « physiologiquement lié au processus ».
Le coût de la matière première représente 80 pour cent du coût de production. C’est pourquoi chaque point de pourcentage gagné en termes de diminution des déchets se traduit par un gain significatif au final.
Un autre type de perte était dû à la complexité du cycle de transformation.
Le processus était souvent déséquilibré par la présence de nombreux goulots d’étranglement, et l’entreprise devait créer des stocks de produits finis qui n’apportaient aucune valeur ajoutée au client, mais qui engendraient trois autres problèmes importants.
Le premier problème était lié à l’augmentation du volume des en-cours de production, qui finissait souvent par être équivalent, en valeur, au stock de matière première brute.
Le second problème concernait l’espace occupé et le troisième, non des moindres, était lié au fait que ces produits devaient être physiquement déplacés, manipulés et déposés par une personne ne faisant pas partie du service production, mais du service logistique.
La valeur ajoutée pour le client final ? Zéro.
Imaginons une entreprise du travail de la tôle de type job shop. Le matériel est poinçonné et les produits poinçonnés sont empilés pour être transférés vers la presse plieuse ou la panneauteuse.
De là, une personne ou un robot doit à son tour prendre la pièce, la charger dans la machine et la récupérer une fois terminée.
Et ceci est l’exemple le plus simple. Le problème se situe au niveau des coûts des stocks intermédiaires des produits semi-finis, qui incluent la surface occupée, les personnes qui doivent la gérer, le coût du matériel et l’attribution correcte de la valeur ajoutée du travail effectué, et dont le calcul est d’une telle complexité que de nombreuses entreprises préfèrent tout bonnement les ignorer.
Un second exemple très intéressant sur l’inefficience de la logistique du processus concernait les entreprises produisant des profils pour carton-plâtre.
Ici, la société Dallan était connue comme fournisseur d’installations de profilage par les principaux leaders européens du secteur et par de nombreuses PME.
Dans ce secteur, la production de profils était relativement simple. De nombreuses entreprises avaient déjà installé nos profileuses à vitesse variable allant de trente à cent-vingt mètres par minute.
En fait, le problème était que le profil avait en soi peu de valeur ajoutée avant qu’il ne soit correctement conditionné et prêt à être expédié. Les entreprises commettaient l’erreur de considérer leur cycle de production terminé une fois le profil réalisé, alors que les coûts les plus importants étaient générés par les facteurs suivants :
- Espace excessif réservé aux opérations d’assemblage et de conditionnement
- Grande quantité de pièces profilées sans valeur ajoutée, mais entreposées entre une station de conditionnement et la suivante
- Nécessité de recourir à du personnel supplémentaire, non seulement pour effectuer le conditionnement, mais également pour déplacer les petits et grands paquets entre les différentes stations de conditionnement et l’entreposage des paquets terminés.
- Ceci est très important, car les systèmes de conditionnement automatiques pour carton-plâtre réduisent l’espace total de la transformation et permettent de passer de la bobine au produit totalement conditionné.
Nous appelons ces systèmes Coil To Pack. Ici, nous pourrez voir une installation en fonctionnement:
Je travaillais également beaucoup avec des entreprises fabriquant des volets roulants en aluminium profilé injecté de mousse. Sur ce marché, la société Dallan était déjà reconnue en tant que leader mondial, car nous fournissions là encore les plus grands producteurs européens, sud-américains, russes et chinois.
Nos clients produisaient principalement des volets roulants dont les barres mesuraient six mètres de long. Ces dernières étaient conditionnées et vendues à des entreprises qui les découpaient sur mesure et les utilisaient pour confectionner les tabliers des volets roulants.
Parfois, nos clients découpaient les barres et fabriquaient les tabliers directement sur site, à l’aide de machines autonomes.
Mais ces deux systèmes présentaient des lacunes importantes dans le processus allant de la bobine au produit fini.
En effet, la découpe sur mesure des barres entraînait de grandes quantités de déchets, variables en fonction des dimensions des tabliers. Le taux de rebus pouvait atteindre entre 5 et 12 pour cent. Le coût de l’aluminium et du polyuréthane représentait à lui seul des centaines de milliers d’euros qui pouvaient être économisés dès le départ !
Le second problème concernait le coût de stockage des barres, qui pouvaient être des profils de dimensions variées, perforés ou non perforés, de couleurs et de finitions différentes. Une grande valeur immobilisée.
La troisième lacune était liée à la nécessité de déplacer les barres de l’entrepôt vers les stations de travail. Cette intervention exigeait naturellement du personnel, des équipements et des manoeuvres très complexes, sans parler du risque permanent d’endommager les profils prélaqués et préfinis..
Les systèmes de travail automatique plus modernes permettaient là aussi de passer directement de la bobine au tablier du volet roulant totalement terminé, sans production de déchets et prêt à installer.
Nous appelons ces systèmes Coil To Window. Ici, on peut voir l’une de ces installations en fonctionnement :
Jean Germanaz, directeur technique du groupe français Stella, qui utilise 12 lignes Coil To Window Dallan, explique les potentialités de ce système de production.
« La collaboration Dallan/Profalux a commencé il y a tout juste 20 ans, en 1999/2000.
À cette époque, Profalux utilisait une machine allemande aujourd’hui vieillissante (lame de 40 mm) et souhaitait profiler ce qui est devenu aujourd’hui la lame la plus vendue dans le groupe Stella, la lame de 39 mm bombée. À cette époque, les échanges avaient lieu avec Monsieur Sergio Dallan, père d’Andrea Dallan, qui finissait ses études quelque part en Europe.
De son côté, la Toulousaine était déjà équipée de moyens Dallan avec la création du groupe Stella en 2007.
Auparavant, la production était assurée à partir de lames en longueur achetées auprès d’un fournisseur européen. Les lames de différents coloris, ajourées et non ajourées, étaient stockées dans des racks, puis coupées au format du volet…avec un taux de chute relativement important. L’assemblage se faisait sur des machines semi-automatique et les lames étaient maintenues entre elles par des embouts en plastique.
La première machine n’était pas une machine « full Dallan ». Elle réalisait le profil avec mousse et la coupe en longueur. Les lames étaient ensuite montées sur une machine spéciale… encore avec des embouts en plastique. À cette époque, les plus grosses difficultés étaient d’ordre informatique. On commençait à voir fonctionner les machines à partir de fichiers informatiques qui étaient générés par notre ERP. Lorsqu’il fallait faire dialoguer des machines de différents fournisseurs entre elles… ce n’était jamais simple.
La technologie Dallan possède de nombreuses qualités parmi lesquelles on trouve :
- 45 mètres entre une bobine de matière première et le sous-ensemble tablier prêt à être monté dans le produit fini
- Entre 3 et 10 minutes pour aller de la bobine au tablier fini
- Zéro stock entre la bobine et le tablier fini
- Un taux de chute étonnamment faible (+/- 3 %) et des solutions innovantes pour réduire la chute de matière
- Un seul opérateur par équipe qui produit jusqu’à 450 m2
- Des innovations Dallan, comme le grugeage pour maintenir les lames entre elles transversalement
Dallan, c’est aussi des échanges qui permettent de répondre aux demandes spéciales des clients :
- Pose de vis plastique en automatique
- Dérouleurs axe vertical
- Lutte contre le bruit
- Amélioration du niveau de sécurité.
- Gestion fine de la qualité de la mousse polyuréthane.
10 machines Dallan chez Profalux, plus d’un vingtaine dans le groupe, 3 ou 4 en commande…un partenariat de 20 ans en 2020. Certainement notre fournisseur avec lequel le lien est le plus fort”
Contactez nos ingénieurs ICI !
Andrea Dallan
CEO – Dallan Spa