Flessibilità nelle linee di profilatura: il sistema COMBI per il cambio rapido delle attrezzature
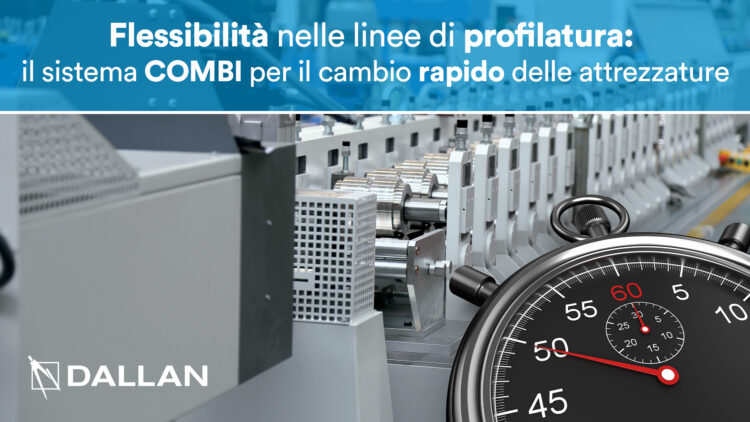
Uno strumento della Lean Production è la tecnica SMED. Questa tecnica è rivolta alla velocità di riattrezzaggio delle linee produttive e significa Single Minute Exchange Die.
L’obiettivo è tendere al riattrezzaggio della linea (con un nuovo coil, o con un nuovo stampo) in meno di dieci minuti.
Chiaramente, questo strumento si rivolge al problema della Flessibilità, ma sempre in chiave di Efficienza e Produttività.
Nelle linee di profilatura, il problema della produttività legata alla flessibilità si presentava, ad esempio, nelle linee di produzione per telai per porte blindate.
Tratto dal libro “La Rivoluzione dell’Efficienza”
RICHIEDI IL LIBRO GRATUITAMENTE
Qui le aziende spesso passavano alla profilatura, perché lavorando da foglio avevano scarti di materiale anche oltre il 20 percento.
Passando alla profilatura, con impianti inadeguati (che non includevano per esempio una punzonatrice da coil parametrica o il sistema di cambio rapido Combi), il tempo di cambio prodotto per passare da un profilo all’altro erano talmente alti che il processo diventava vantaggioso solo se i lotti erano di almeno una settimana di lavoro.
Nella produzione di telai per porte blindate, la punzonatura parametrica unita al sistema di cambio produzione Combi per rulli e stampi – già visto nel capitolo precedente – risolveva egregiamente il problema della flessibilità. Infatti per telai con dimensioni e lavorazioni diverse, si potevano produrre telai di dimensioni diverse uno dall’altro, arrivando al famoso lotto uno.
O, come lo chiama Giovanni Maffei, la produzione “Zero Standard”: questo indica che il sistema è preparato e sempre pronto a realizzare profili di dimensioni diverse senza tempi di attrezzaggio e senza bisogno di programmazione umana delle macchine.
Nel settore degli infissi, porte blindate e tagliafuoco, quando la macchina doveva realizzare profili differenti era necessario il cambio di attrezzatura: il sistema Combi per rulli e stampi permetteva di eseguire il cambio in meno di dieci minuti per ciascun gruppo e in meno di un’ora complessivamente.
I produttori trovavano lo stesso problema nel settore dei profili per controsoffitti, dove le prime macchine erano linee preparate per realizzare numerosi profili e dove il cambio di rulli per passare da un profilo a un altro poteva richiedere ore o giornate.
Per questo per loro era importante identificare con certezza le soluzioni che aumentassero la produttività, riducendo il più possibile il tempo di attrezzaggio a meno di un’ora; se possibile portandolo entro i dieci minuti.
Come vedremo, il sistema Combi per rulli e stampi aveva una duplice funzione: aumentava la produttività – riducendo il tempo di cambio produzione – e al tempo stesso la flessibilità dell’impianto.
Flessibilità: il sistema Combi per profilatura
Nella profilatura a rulli, tradizionalmente i rulli di ogni serie sono montati su rulli sovrapposti.
I rulli vengono smontati per passare da un profilo all’altro e il tempo di cambio della serie può essere di ore o prendere anche una giornata.
Anche perché oltre ai rulli motorizzati montati sugli alberi, spesso servono rulli tangenziali di formazione che sono montati su accessori di supporto.
Questo comportava tempi di setup molto alti e per questo motivo la tecnica si è evoluta verso i sistemi a cassetti intercambiabili, dove su strutture apposite sono montati gruppi di rulli.
In genere questi cassetti includono gruppi di quattro o sei rulli; ed è un problema perché:
- è necessario montare più cassetti per cambiare il prodotto
- inoltre ciascun cassetto va collegato alla trasmissione che spesso è costituita da molteplici giunti cardanici.
Questo sarebbe ancora un tempo lunghissimo per il cambio utensili, ma il sistema Combi risolve in modo semplice entrambi i problemi.
Il sistema Combi utilizzato nelle macchine Dallan è unico nel suo genere.
Infatti i gruppi Combi includono su di una base di alluminio:
- Trasmissione a ingranaggi (a denti dritti, obliqui o con sistema biella-manovella)
- Sistema di lubrificazione della trasmissione
- Alberi già regolati in altezza
- Rulli già regolati al corretto spessore
- Accessori montati sulla piastra in alluminio e già regolati
- Introduttore lamiera
- Gruppo di raddrizzatura con rulli
Il gruppo Combi presenta all’esterno solo una ruota dentata. Sul basamento si trova un’analoga ruota dentata collegata al motore e al riduttore.
Quando il gruppo Combi viene appoggiato al basamento, si centra su appositi perni di allineamento per andare velocemente in posizione e allo stesso tempo le due ruote dentate ingranano l’una con l’altra.
In questo video possiamo vedere anche l’operazione di sostituzione di un gruppo Combi:
Le macchine attrezzate con questo particolare sistema Combi rispondono quindi al principio SMED insegnato dalla Lean Production (Single Minute Exchange Die), che insegna a organizzare macchine e produzione in modo che il cambio di un utensile avvenga in meno di dieci minuti.
Il sistema Combi offre anche quattro altri vantaggi notevoli.
- Se abbiamo un impianto e più serie di rulli, sono sufficienti due Combi. Il primo lavora in macchina, mentre un tecnico può eseguire i cambi rulli sul secondo Combi, fuori macchina – come si dice, in tempo mascherato
- Se abbiamo un sistema che richiede grande potenza, invece di avere un unico grande motore speciale, sezioniamo l’impianto in due o tre sezioni con gruppi Combi motorizzati in modo indipendente, con motori di taglia più piccola e standard. Inoltre questo rende possibile modificare le velocità delle diverse zone della macchina mantenendo in trazione il profilo fino alla fine e migliorandone ancora la raddrizzatura
- Inoltre i Combi sono attrezzature affidabilissime. In oltre quarant’anni di attività, dopo migliaia di Combi prodotti non sono mai stati segnalati problemi
Quindi i gruppi Combi sono praticamente eterni. Spesso quando l’impianto supera i vent’anni, le normative di riferimento per la sicurezza sono cambiate e i componenti elettronici sono spesso obsoleti e non più disponibili come ricambi.
È possibile, così, sostituire solo la base della profilatrice e dell’impianto e riutilizzare tutti i gruppi Combi e le serie di rulli esistenti, poiché i nuovi basamenti sono compatibili o possono essere resi tali.
In questo modo puoi avere un impianto nuovo e a normativa con minimo investimento contenuto, utilizzando Combi e stampi esistenti!
Infine un aspetto molto importante.
Quando si inizia a lavorare è normale avere un solo basamento attrezzato con più Combi per diversi profili.
Quando la richiesta di produzione aumenta, dato che l’investimento in attrezzature è già stato fatto, è possibile raddoppiare la produzione investendo semplicemente su di un basamento e riutilizzando i Combi già presenti.
Così facendo:
- Si dimezzano i cambi prodotto
- Si raddoppia l’affidabilità della Produzione
- Di conseguenza, la produzione risulta sempre più che raddoppiata!
Eros Damilano è il titolare della Damilano, società di Cuneo specializzata nella produzione di profili conto terzi. Eros acquistò da mio padre la prima profilatrice per doghe nel 1984 e iniziò a produrre direttamente nel proprio garage. Il posto era molto piccolo, per cui lo scarico della profila era al di fuori del garage ed Eros caricava i profili direttamente nel furgone per la consegna!
Oggi ha anche altre aziende e la Damilano ha 20 linee Dallan funzionanti.
Damilano produce internamente i rulli delle proprie linee, adattandosi così alle richieste del mercato. Ecco cosa può raccontarci Eros Damilano, titolare dell’azienda, sul lavoro svolto con Dallan, le sue profilatrici e con i sistemi Combi:
“Attualmente la Damilano Group dispone di 20 linee di profilatura che realizzano circa 500 tipologie di profili, di cui il 70% su disegno del cliente. Trasformiamo circa 1000 tonnellate mese con l’aiuto di 80 collaboratori
La profilatura è stata da noi introdotta per la produzione di controsoffittature, che al tempo erano in mano a 3-4 aziende in Europa, in Italia esisteva solo la Hunter Douglas con una sede a Milano e la Metal Sadi a Vicenza, per cui spazio nel mercato ve n’era a volontà. Ma ironia della sorte, in due acquistammo la prima profilatrice dall’ing. Dallan che la presentò al Saie di Bologna, noi e la Tecnesa con sede a Marene, a soli 20 chilometri di distanza. Per fortuna riuscimmo a evitare una guerra commerciale!
La prima profila fu acquistata nel 1984 e caricata dall’officina Dallan, dopo un collaudo lunghissimo, alle 4 del mattino in una giornata particolarmente piovosa. La produzione di Dallan era in un piccolo capannone in una zona agricola e per uscire con il camion dal fango dovemmo chiamare un contadino, amico dell’Ingegner Dallan, che con il trattore ci trainò fuori.
Viste le allora scarse risorse economiche e di spazio, la profila fu posizionata in un garage e quando era l’ora di profilare aprivamo la serranda e con i profili uscivamo in strada: nei casi di barre particolarmente lunghe dovevamo parcheggiare le auto in doppia fila per mascherare il problema!
Successivamente, ritenendo la profilatura una attività di nicchia ma con buone possibilità di sviluppo, introdussi la produzione dei profili per cartongesso, che ai tempi uscivano a soli 10/12 metri al minuto: ora si va infinitamente più veloce ma abbandonammo poi quel settore per spostarci su profili più spessi, più complessi e forati a disegno.
La prima punzonatrice per eseguire le forature sui coils, acquistata da Dallan nel 1988, consisteva in una unità idraulica con 5 stazioni, permettendo quindi di eseguire 5 diverse lavorazioni, ma con posizioni fisse, ma presto La Dallan progettò la Pxn, una punzonatrice flessibile da coil con 20 utensili mobili, che ci aprì un mondo di possibilità nella punzonatura, con una flessibilità incredibile.
La scelta di lavorare da coils ci ha permesso di sostituire in molti casi la pressopiegatura, riducendo quasi a zero gli scarti eliminando il vincolo delle lunghezze, permettendo di ridurre i costi delle varie forature, che infatti vengono eseguite in linea quasi in tempo mascherato.
Un altro sviluppo molto interessante della Dallan, è stato il costruire le profilatrici con i gruppi Combi: questo ci ha permesso, nel caso ad esempio della produzione dei telai per porte blindate in lamiera, di avere le diverse attrezzature sempre montate sui vari gruppi Combi e poter quindi cambiare produzione in tempi brevissimi!
Quando invece produciamo i nostri 500 profili a disegno, i gruppi Combi ci permettono di montare i rulli sulle testate e fuori macchina in tempo mascherato. In questo modo riduciamo il tempo di cambio produzione alla sola sostituzione dei gruppi ed al montaggio degli stampi di taglio, con un risparmio in tempo del 60/70% circa!” – Eros Damilano
Tratto dal libro “La Rivoluzione dell’Efficienza”
RICHIEDI IL LIBRO GRATUITAMENTE
Andrea Dallan
CEO – Dallan Spa