Macchine profilatrici: è più facile vincere alla lotteria che trovare un tecnico specializzato
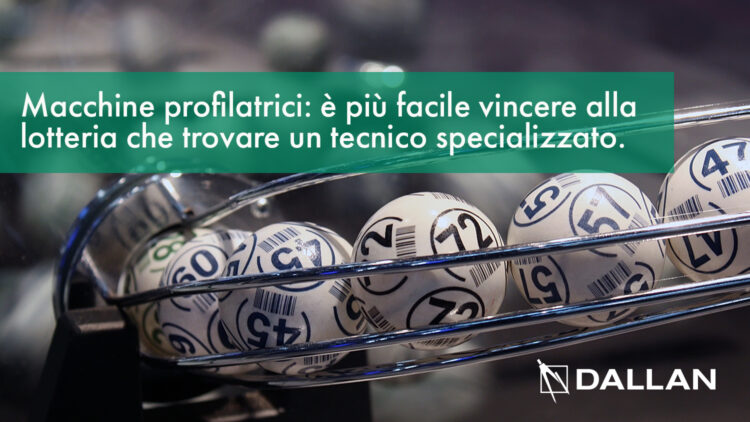
La difficoltà di reperire personale produttivo, specialmente in Europa e Nord America, sta diventando un problema sempre più diffuso.
Questo si accompagna con la volontà di contenere il più possibile i costi di produzione, sostituendo il personale addetto a operazioni semplici o ripetitive con automazioni. Il sogno proibito degli imprenditori e delle aziende è arrivare a produrre con pochissimo o zero personale.
Quindi mi trovavo di fronte a una duplice esigenza.
Da un lato vedevo la volontà delle aziende di acquisire linee ad alta automazione, che partendo dalla materia prima grezza arrivassero, se possibile, al prodotto imballato e pronto da spedire impiegando il minimo di personale. Questo spingeva verso linee con un alto livello di sofisticazione.
Tratto dal libro “La Rivoluzione dell’Efficienza”
RICHIEDI IL LIBRO GRATUITAMENTE
Dall’altro c’era la necessità di avere linee che fossero molto semplici da usare. Infatti diventava sempre più difficile trovare personale qualificato e le aziende non volevano trovarsi a essere legate a tecnici iper-specializzati, che erano gli unici a conoscere il “segreto” della linea che conducevano.
Le automazioni e le macchine dovevano essere semplici da usare anche da personale non esperto.
Abbiamo visto nel capitolo precedente come le automazioni Coil To Pack siano state un grande punto di forza per aumentare la produttività delle linee per profili per cartongesso.
Questo lo potei constatare anche nelle linee per profili per controsoffitto T-bar. Questa era un’altra delle grandi specializzazioni dell’azienda. Il T-bar è un profilo a T rovesciato, composto da un corpo in lamiera zincata e una copertina in lamiera o alluminio preverniciati.
Per la produzione di questi profili, un cliente tedesco voleva attivare una serie di linee di produzione di altissima capacità e il dato di progetto era che le linee dovevano produrre il doppio delle macchine fino ad allora presenti sul mercato, con un quarto del personale.
L’analisi mostrò che era necessario prendere in considerazione non solo la produzione del profilo, ma anche la sequenza di controllo qualità e imballo del prodotto; considerando la linea sotto molteplici aspetti: dimensioni e lunghezza dei coils, velocità di produzione, velocità di consumo dei materiali all’interno della linea, qualità delle materie prime, tipologia di imballo da realizzare, studio ergonomico sul peso dei pacchi di profili, collegamento con sistema di visione per il controllo della qualità dei profili.
Il risultato sono state le prime linee completamente integrate Coil To Box – dal coil al profilo finito in scatola, già posizionato sul pallet per la reggiatura e la spedizione.
Questi impianti producevano questi profili estetici, molto tecnici e complessi, alla velocità di oltre 100 metri al minuto.
Per fare tutto questo necessitavano solo di tre supervisori ogni due linee, principalmente per assicurare l’approvvigionamento della materia prima alle macchine, che – letteralmente – divoravano tonnellate e tonnellate di lamiera zincata, preverniciata, acciaio altoresistenziale per i clips, cartoni per l’imballo e colla per consegnare a fine linea i pallet con i cartoni perfettamente ordinati e impilati uno sull’altro.
Anche i sistemi Coil To Window, che abbiamo già visto nel caso di Profalux e del gruppo Stella, sono un ottimo sistema per introdurre automazione nella produzione di teli di tapparella. In questo caso, pur trattandosi di automazione, non parliamo di imballo ma di confezionamento.
I sistemi Coil To Window esistono anche per un altro ramo di prodotti per la protezione solare: le veneziane per esterni.
Questi prodotti fino a qualche anno fa erano caratteristici del mercato svizzero, austriaco e tedesco. La richiesta oggi si è allargata a tutta l’Europa dell’est, la Francia e iniziano ad arrivare anche in Italia. Le veneziane per esterni hanno il vantaggio, rispetto alle tapparelle, di permettere la modulazione della luce all’interno della stanza, variando l’inclinazione delle lamelle.
Anche in questo caso, come nel caso delle tapparelle, una finestra è diversa dall’altra e quindi anche un telo prodotto può essere diverso dal successivo. Riuscire a gestire la produzione senza dover programmare manualmente le macchine è assolutamente indispensabile.
Esistono due tipi principali di sistemi di veneziane, il sistema di veneziane a C e a Z. Rispetto alla tapparella, queste tende hanno sistemi di montaggio più complessi, che richiedono l’applicazione di perni e ganci sulle estremità dei profili e il montaggio su scalette in tessuto di forma diversa.
Fino al 2005, le macchine profilatrici realizzavano esclusivamente i profili che venivano poi assemblati manualmente su appositi telai. Il tempo maggiore era sempre quello del montaggio, non la produzione dei profili che poteva arrivare a sessanta metri al minuto.
Dallan era sempre stata presente in questo mercato, trattandosi di profili in lamiera sottile e preverniciata, quindi una nostra specialità. I nostri clienti iniziarono a chiedere sistemi per realizzare il montaggio di questi profili sulle scalette: iniziammo quindi a studiare e costruire i primi sistemi di applicazione dei ganci e i primi sistemi di infilaggio, che finimmo per brevettare.
Infatti tale è la mole di lavoro richiesta per il montaggio manuale di questi profili, che le automazioni finiscono per ripagarsi in brevissimo tempo.
I sistemi Dallan per veneziane vennero studiati con la stessa logica del sistema tapparelle: diverse stazioni di lavoro e assemblaggio separate da dei trasportatori che fungono da buffer per equilibrare il tempo di lavoro di tutte le stazioni. Nel tempo abbiamo lavorato per equilibrare le velocità delle diverse macchine per evitare di avere dei colli di bottiglia nel processo fino ad arrivare alle ultime straordinarie applicazioni.
Il risultato? Un sistema come quello per veneziane a C visibile in questo video:
La prima parte della linea realizza i profili completi delle forature. Il profilo lavorato e tagliato viene consegnato a un set di trasportatori e portato alla macchina che applica i perni di testa. Quindi attraverso una seconda serie di trasportatori, i profili arrivano all’ultima stazione di assemblaggio, dove vengono infilati uno a uno nella scaletta di sostegno.
Il telo assemblato viene prelevato da un operatore oppure in modo automatico e normalmente riposto in appositi carrelli per andare alle stazioni finali di assemblaggio.
In queste stazioni il telo viene aperto, controllato e vengono aggiunti gli ultimi complementi: il profilo estruso alla base, che conferisce il giusto peso e tensione alla tenda, vengono aggiunti i nastri di sollevamento e la motorizzazione inserita nel profilo di testa a C.
Con queste soluzioni i profili vengono realizzati e assemblati riducendo al minimo il lavoro manuale e i magazzini intermedi, inoltre, permettono un cambio rapidissimo del profilo e del colore del nastro.
Un sistema perfettamente analogo esiste anche per i profili a Z, che richiedono un montaggio ancora più complesso. Infatti su questi profili vengono installati ganci laterali che si chiudono su dei nastri a occhielli: anche in questo caso abbiamo dovuto studiare un sistema a stazioni di lavoro indipendenti che permettesse di semplificare il montaggio e arrivare in brevissimo tempo dal coil al telo confezionato e pronto per il montaggio finale.
Queste automazioni hanno ridotto a meno di un terzo il personale necessario alla lavorazione di tipo tradizionale, introducendo altri notevoli vantaggi, come la riduzione del work in progress e l’introduzione dei sistemi di gestione della produzione centralizzati, con programmazione parametrica che permette di caricare i dati dell’ordine direttamente dall’ERP aziendale.
Nella figura possiamo vedere come il software integrato nella macchina permette anche all’operatore di verificare la forma di un telo prima di lanciare l’ordine di produzione alla macchina.
Il software di gestione di queste linee è un asset fondamentale per l’azienda: gli ultimi sistemi permettono di controllare gli ordini in produzione, inviare liste di lavoro e ricevere feedback automatici sulla produzione già eseguita e anche di gestire la produzione di lamelle extra per eventuali riparazioni, qualora nelle operazioni manuali di montaggio a valle si verificassero dei problemi.
Con la fusione del 2013, incorporammo in Dallan anche Elda, l’azienda che si era specializzata nella produzione di quadri elettrici e software per le linee Dallan. Avere all’interno dell’azienda il team di softwaristi che sviluppa il software di gestione ci ha permesso di rispondere in modo puntuale alle richieste del mercato, sviluppando software che complessivamente offrono molto di più di quanto i clienti normalmente si aspettano.
Oggi il team di softwaristi interno è un asset decisamente fondamentale per trasferire ai nostri clienti un enorme valore, automatizzando parti importanti del flusso informativo aziendale.
Infatti, come abbiamo visto, in ottica LEAN non è sufficiente solamente eliminare gli sprechi materiali, ma è necessario anche eliminare i flussi di informazioni e i processi cartacei che non producono valore aggiunto per il cliente!
Con la flessibilità di un team di sviluppo software, è possibile arrivare a soluzioni come quella in figura:
In questo caso, il flusso delle informazioni è ottimizzato e, pur lasciando un margine di azione al responsabile di produzione e all’operatore, abbiamo certamente eliminato tutto il flusso di ordini cartacei e inserimento manuale delle informazioni, con gli errori che questo può generare.
Tratto dal libro “La Rivoluzione dell’Efficienza”
RICHIEDI IL LIBRO GRATUITAMENTE
Andrea Dallan
CEO – Dallan Spa