Profilatrici: ecco come garantire la produttività e il valore di un impianto con la manutenzione programmata e i contratti di assistenza
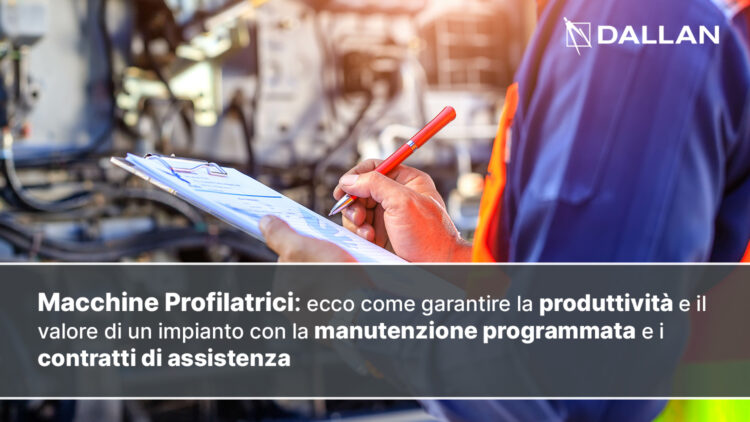
Questa è una nota importante. Vedremo negli ultimi capitoli che il costo orario di un impianto, nei primi anni, è legato all’ammortamento dell’investimento: infatti nei primi anni si ha l’affidabilità tipica degli impianti di nuova generazione, quindi, il valore dei costi di manutenzione è inizialmente molto basso.
Una volta ammortizzato l’impianto, il costo orario scende, naturalmente, ma nell’attribuire il costo orario all’impianto consiglio sempre di continuare a utilizzare il valore inizialmente calcolato. Per due motivi.
Il primo è di tipo conservativo: l’impianto si è ripagato, quindi calcolando il costo con il valore iniziale, otteniamo sempre un valore più alto che ci permette di avere un fattore di sicurezza nei calcoli del costo pezzo.
Tratto dal libro “La Rivoluzione dell’Efficienza”
RICHIEDI IL LIBRO GRATUITAMENTE
Il secondo motivo è legato al mantenimento del valore dell’investimento fatto.
All’interno della mia azienda, abbiamo molti impianti di produzione: torni a controllo numerico, impianti di fresatura elettroerosioni e rettifiche per la produzione degli utensili e degli stampi.
Per garantire affidabilità anche dei nostri impianti di produzione, sappiamo che dobbiamo continuare a investire in manutenzione e che i costi di manutenzione di un impianto, dopo i primi cinque anni, possono salire sensibilmente.
In generale quando acquistiamo un nuovo impianto automatizzato, in Dallan sappiamo che per garantire la qualità della produzione in uscita e l’affidabilità dell’impianto dobbiamo vedere l’investimento in più dimensioni.
Investimento nell’impianto
Chiaramente è l’investimento iniziale, dove ci assicuriamo una macchina affidabile e che produca con altissimi standard qualitativi. Investire in impianti affidabili che durano decenni assicura un grande risultato: in particolare quando l’impianto è ammortizzato, il costo orario dell’investimento si azzera! Lo vedremo nei capitoli finali dedicati al calcolo del costo di produzione.
Investimento nella professionalità personale addetto
Abbiamo parlato del problema della scarsità di personale tecnico specializzato e della necessità di investire in impianti semplici da usare. Verissimo, infatti non occorre cercare specialisti di profilatura, punzonatura o taglio laser.
Ma se è vero che l’impianto automatico richiede meno manodopera, è importante anche che gli addetti alla linea, i supervisori – o perlomeno i responsabili di reparto – siano persone motivate e qualificate da un punto di vista manageriale.
Quando si tratta di addestrare i tecnici del cliente nell’utilizzo delle linee Dallan, preferiamo spesso lavorare con giovani tecnici che abbiano voglia di mettersi in gioco, anche appena usciti dalla scuola, piuttosto che con personale che abbia già esperienza.
Infatti i nuovi impianti in ottica Industria 4.0 includono funzioni e tecnologie, come la teleassistenza e il controllo da ufficio, che richiedono curiosità, elasticità e freschezza. Doti che incontriamo spessissimo nei giovani.
Investimento nelle materie prime
Gli impianti oggi hanno raggiunto una grande sofisticazione. Capita che chi acquista le materie prime, cerchi di ottimizzare e ridurre i costi acquistando materiali di seconda scelta.
Questa non è la strada giusta, come abbiamo già visto.
Infatti:
- I materiali di seconda scelta richiedono tempi di regolazione della macchina non prevedibili. E prevedere i tempi di avvio macchina è FONDAMENTALE.
- Ma soprattutto, ci sono sistemi molto più efficaci per ridurre il costo della materia prima per pezzo prodotto.
Come ad esempio passare dalla lavorazione a partire da foglio al coil, oppure passare dalla produzione di teli di tapparelle a partire da barre, alla produzione diretta a partire da coil, che noi chiamiamo COIL TO WINDOW.
Questo garantisce altissima qualità del prodotto per il cliente finale e un grandissimo risparmio negli acquisti, dell’ordine di centinaia di migliaia di euro all’anno.
Investimento nella manutenzione programmata
Questa è la quarta dimensione dell’investimento. La manutenzione infatti non è un costo ma un investimento. E deve essere programmata e preventiva, per evitare costosi fermi macchina in emergenza.
Le macchine punzonatrici, profilatrici e laser sono progettate per durare decenni, ma bisogna tenere conto che alcuni organi come cuscinetti, viti a ricircolo di sfere, riduttori e così via sono soggetti a un’usura proporzionale all’utilizzo della macchina.
Dopo i cinque anni, è importante prevedere a budget un valore per la manutenzione preventiva, che si svolge in genere con una visita annuale dei nostri tecnici. Durante questa visita i tecnici eseguono i controlli e consegnano al cliente una lista di ricambi che consigliamo di tenere in casa.
Questi ricambi sono disponibili in caso di emergenza, oppure vengono installati dai nostri tecnici durante la visita dell’anno successivo.
In questo modo, ogni cliente può creare un piccolo magazzino di ricambi relativo all’impianto, che garantisce affidabilità e costi irrisori legati a eventuali guasti.
Questo è molto importante.
Occorre considerare che questi costi – con impianti che possono lavorare anche 24 ore al giorno – dovrebbero essere costanti negli anni e se questo non avviene, dovrebbe essere un campanello di allarme per l’imprenditore!
Alcune aziende hanno sottovalutato l’importanza della manutenzione preventiva e in alcuni casi può essere un errore molto costoso.
Un’azienda nostra cliente aveva acquistato negli anni ‘90, dieci macchine profilatrici e ciascuna di queste macchine produceva – e produce – un componente che confluisce in una linea di produzione e assemblaggio.
Le macchine sono sempre attrezzate con lo stesso profilo, quindi la linea di assemblaggio lavora in logica “Pull” dove la linea a valle richiede i pezzi di volta in volta alle macchine.
Un sistema di produzione eccellente, che ha prodotto per quasi trent’anni in modo impeccabile.
Negli ultimi anni avevamo osservato una riduzione dell’acquisto dei ricambi e non avevamo richieste di manutenzione preventiva. Nel frattempo, i componenti elettronici delle macchine erano diventati obsoleti, così come le protezioni e le sicurezze.
Quando si verificarono dei fermi macchina, siamo stati ricontattati per una manutenzione generale, ma considerando lo stato di abbandono degli impianti e i costi di rimessa a punto delle linee, il valore degli interventi risultava molto superiore al costo che si sarebbe sostenuto annualmente per la manutenzione programmata.
Fortunatamente, grazie al sistema Combi, è stato possibile riutilizzare tutte le attrezzature e gli stampi e rinnovare tutta la produzione e i sistemi di sicurezza investendo solo nelle nuove basi e quadri elettrici delle linee.
Come facciamo in Dallan: per mantenere il nostro vantaggio competitivo continuiamo a investire in nuove tecnologie, torni e centri di lavoro più veloci, affidabili e automatiche, che permettano di produrre con maggiore qualità, meno scarti e impiegando meno energia.
Programmiamo la sostituzione delle macchine quando superano i vent’anni di vita, cercando di mantenere la compatibilità con gli utensili che già abbiamo disponibili e con gli asservimenti all’intorno alle macchine.
Abbiamo anche osservato che i nostri operatori sono anche più motivati nel vedere che si investe in impianti più ergonomici e semplici da usare: un’importante evoluzione anche per loro, che sono i nostri “scultori dell’acciaio”!
Sławomir Sofiński, responsabile di produzione e della manutenzione di Aluprof, racconta qui come la corretta manutenzione delle linee permette di garantire il valore dell’investimento e la continuità della produzione di tapparelle.
“La nostra azienda fu fondata nel 1997. Prima di conoscere Dallan, impiegavamo una linea di profilatura tedesca per produrre i profili di tapparella. Nel 1998 arrivò la prima profilatrice Dallan, seguita da altre otto linee, l’ultima installata nel 2020.
Tutte le linee Dallan sono prodotte con componenti di aziende leader, come SKF, Nidec e Rexroth e in ogni macchina incorpora tecnologie molto avanzate. Siamo molto contenti dell’evoluzione dei controlli verso il sistema Beckhoff.
Nel corso degli anni, abbiamo visto che ogni nuova linea include sempre dei miglioramenti, specialmente nelle ultime due macchine che abbiamo ricevuto.
Per alcuni componenti, sappiamo che è necessario mantenere alcuni componenti in casa come ricambi: prima di tutto vorrei dire che non esistono macchine che non hanno bisogno di manutenzione.
Se vuoi mantenere la tua macchina in buone condizioni, la prima cosa da fare è la manutenzione preventiva. Per esempio, in Aluprof prevedo tre tipi di manutenzione preventiva: la manutenzione mensile dove una volta al mese la macchina viene pulita a fondo e controllata per verificare che non ci siano perdite di aria o olio in nessuna parte. La punzonatrice viene pulita e controlliamo il serraggio dei collegamenti meccanici. Questa manutenzione la facciamo al di fuori del tempo di produzione, di solito il sabato o la domenica: abbiamo delle checklist di controllo e questa manutenzione prevede 8 ore di lavoro.
Poi abbiamo la manutenzione annuale, che avviene all’inizio di ogni anno prima del periodo di alta stagione. Ogni macchina Dallan viene fermata per tre giorni e i nostri tecnici controllano separatamente ogni parte della linea: punzonatrice e centrale idraulica, segatrice e gruppo di infilaggio, profilatrice e aspo svolgitore. I nostri tecnici controllano le condizioni di ogni albero e testata e sostituiamo eventuali cuscinetti o elementi usurati.
Si completa l’ingrassaggio secondo le schede di manutenzione ed il controllo delle viti a ricircolo di sfere. Le prime profilatrici avevano una parte della trasmissione a catena, per cui se è necessario o si è allentata la sostituiamo. Oggi le trasmissioni delle macchine sono interamente ad ingranaggi.
Infine abbiamo la manutenzione preventiva. L’anno scorso abbiamo implementato il nostro MES interno (Manufacturing Execution System). Questo sistema ci riporta una mole enorme di dati e abbiamo individuato alcuni KPI per il reparto manutenzione della nostra azienda.
I KPI più importanti riguardano la funzionalità delle linee. Abbiamo installato degli extra sensori nelle punzonatrici che controllano tutti i cilindri idraulici e il numero di operazioni di foratura eseguite sulle tapparelle. Se uno dei quattro sensori non registra un segnale, l’intera linea si ferma e un segnale luminoso indica quale cilindro ha presentato il problema. Questo evita che si producano pezzi non conformi, prima l’operatore poteva non vedere l’errore e il pezzo non conforme veniva imballato comunque.
Il numero di punzonature ci informa anche quando lo stampo dovrebbe essere sostituito; quando ci avviciniamo al limite di utilizzo, appare un allarme giallo che sul MES e i nostri tecnici ricevono un SMS che informa il tecnico su quale utensile dovrebbe essere sostituito.
Questo ci aiuta a fare la corretta manutenzione sugli stampi senza portarli a fine vita, possiamo rettificarli e utilizzarli per molto tempo. Per ogni linea abbiamo due set di stampi in modo da poterli sostituire in pochi minuti e continuare la produzione.
Il nostro MES calcola anche quanti chilometri di profilo sono passati in ogni gruppo combi e in breve tempo sapremo anche prevedere quando alcuni rulli devono essere sostituiti.
Per quanto riguarda la parte elettrica ed elettronica, è molto difficile prevedere la vita di questi componenti, ma il nostro lavoro è mantenerli nelle migliori condizioni. I sensori ottici sono puliti ogni giorno. Due volte all’anno ogni quadro elettrico è controllato con una termocamera e i nostri tecnici controllano il quadro elettrico, i collegamenti e se ci sono degli elementi che si riscaldano in modo anomalo vengono sostituiti.
Abbiamo un ottimo rapporto con il team software di Dallan, che tramite il teleservice riesce anche a riparare o riprogrammare il modulo PLC a distanza. Occorre fare attenzione per le vecchie macchine, perché alcuni componenti elettronici stanno andando fuori produzione ed occorre lavorare in modo preventivo con i tecnici Dallan.
Quando si lavora in alta stagione, se si presenta un problema bisogna avere dei sistemi di intervento rapido: le Forze Speciali non esistono solo nell’esercito!
Alcuni gruppi di automazione all’interno delle macchine sono costituiti da molte piccole parti e abbiamo procurato dei set completi da tenere a magazzino presso di noi. In questo modo possiamo sostituire in pochi minuti per esempio una vite a ricircolo o un collegamento rapido. Molte parti sono compatibili tra le linee e teniamo queste parti disponibili nel nostro magazzino.
La pulizia regolare delle macchine è molto importante ed ogni fine settimana alcuni operatori mantengono le linee perfettamente pulite. Ho preparato per loro una lista dei punti da pulire con più attenzione, così non mi serve uno specialista per questo lavoro. La pulizia è molto importante perché alcune parti accumulano polvere, come i ventilatori e gli scambiatori di calore e la pulizia mantiene l’efficienza e il valore dei nostri impianti.” – Sławomir Sofiński
Tratto dal libro “La Rivoluzione dell’Efficienza”
RICHIEDI IL LIBRO GRATUITAMENTE
Andrea Dallan
CEO – Dallan Spa