Profilatura Just In Time: analizzare il costo del magazzino e dei magazzini intermedi
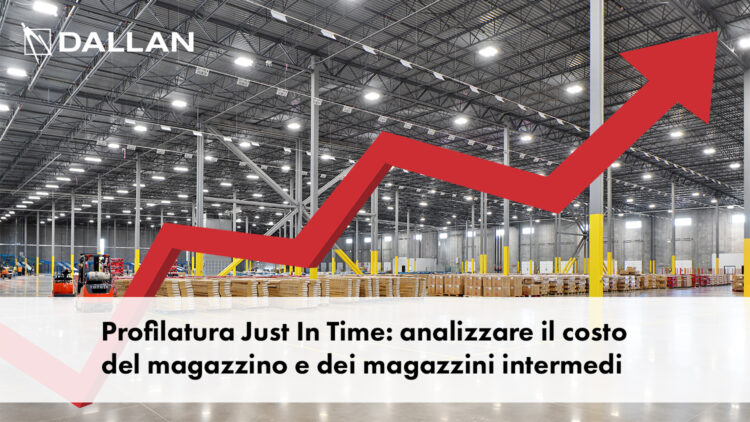
Tratto dal libro “La Rivoluzione dell’Efficienza”
RICHIEDI IL LIBRO GRATUITAMENTE
Conosci quanto pesa il costo dei magazzini nell’efficienza dei tuoi processi?
Generare efficienza vuol dire anche considerare l’impatto del magazzino sul flusso di cassa.
Tra gli strumenti della Lean Production, la produzione Just In Time prevede di realizzare i prodotti in modo che siano pronti nel momento della spedizione.
Questo si contrappone a sistemi di produzione dove l’impianto produce per un magazzino – da cui sono successivamente prelevati i prodotti per le spedizioni – quanto richiesto.
Ma devi sapere che ci sono altri due tipi di magazzino in azienda: il magazzino della materia prima e il magazzino dei semilavorati.
Ogni volta che prendiamo un coil o un foglio di lamiera, lo lavoriamo e lo posizioniamo in un magazzino intermedio, gli aggiungiamo valore.
Quindi il valore del magazzino cresce a mano a mano che si passa dalla materia prima al prodotto finito (negli ultimi capitoli, vedremo anche come calcolare il valore aggiunto di ciascuna operazione e come cresce nel dettaglio questo costo).
Il problema è che questo valore non produce alcun flusso di cassa.
Quanto migliorerebbe il tuo flusso di cassa se potessi produrre solo il venduto, potendo controllare i tempi di produzione in modo da avere il prodotto pronto per la spedizione nel tempo programmato?
Questo è la sintesi del metodo Just In Time: produrre solo quanto richiesto, quando è richiesto e mantenendo al minimo il costo del magazzino:
- Magazzino materia prima;
- Magazzino Semilavorati: il magazzino dei semilavorati è chiamato anche WIP o Work In Progress;
- Magazzino prodotto finito;
Per quanto riguarda il magazzino della materia prima, lo si ottimizza con una buona programmazione basata su dati storici e con tecniche di riordino per evitare la rottura di stock.
Il magazzino dei semilavorati è un grosso problema nelle aziende che lavorano con tecnologie di punzonatura e piegatura standard.
Infatti oltre al valore di questo magazzino – che aumenta quante più operazioni svolgiamo sul semilavorato – questo magazzino genera anche alti costi per la gestione e lo spostamento dei pallet e per le operazioni di prendere e deporre i pezzi.
Negli impianti che lavorano da coil, la lavorazione continua e in linea permette di eliminare tutte le operazioni del prendere e deporre i pezzi, passando dal coil di materiale al prodotto finito senza magazzini intermedi.
Questo avviene, ad esempio nel sistema Coil To Window dove per le tapparelle e le veneziane, si produce in modo automatico un telo finito di tapparella avvolgibile o veneziana, passando direttamente dalla materia prima al prodotto finito.
Nei sistemi Coil To Box e Coil To Pack, impiegati rispettivamente nella produzione di profili T-bar e cartongesso, l’impianto passa direttamente dal materiale in coil al prodotto imballato e pronto per la spedizione.
Anche i sistemi di punzonatura e taglio laser da coil, semplici o combinati, permettono di eliminare le operazioni di carico e scarico dei pannelli, risparmiando tempo e manodopera.
Questi possono essere poi collegati a profilatrici, piegatrici e pannellatrici automatiche in modo da arrivare il più rapidamente possibile e possibilmente senza magazzini intermedi, dalla materia prima al prodotto finito.
Il magazzino dei prodotti finiti serve spesso a fare da cuscinetto tra la domanda del mercato e la capacità produttiva.
Per produrre Just In Time e ridurre al minimo il magazzino dei prodotti finiti, è necessario avere macchine molto affidabili che possono lavorare lotti di produzione anche molto piccoli.
Quindi la flessibilità degli impianti e la possibilità di cambiare produzione in modo semplice e sicuro è fondamentale.
Vedremo in queste pagine il tipo di soluzioni che permettono di raggiungere questo risultato, ad esempio i sistemi di punzonatura parametrica e i sistemi di cambio utensili Combi: tutte soluzioni che si rifanno alla metodologia SMED per il cambio produzione.
Sistemi snelli di produzione: linee di profilatura parallele
In alcuni casi ci sono prodotti che richiedono più componenti di profilatura, che possono essere prodotti con filosofia Just in Time per poter essere assemblati nell’ordine corretto.
Un esempio sono le tapparelle, dove insieme al telo spesso si produce il tubo ottagonale per l’avvolgibile già tagliato a misura.
Il tubo viene accoppiato con il motore e inviato alla linea dove si sta producendo il telo di tapparella corrispondente.
L’Ingegner Maurizio Castignoli, di Alias Porte Blindate, spiega questo concetto nella produzione di telai e pannelli per porte blindate.
“Nel 1995 conobbi Dallan e la tecnologia della profilatura mentre lavoravo come direttore di produzione presso un’azienda leader nella produzione di porte blindate e tapparelle avvolgibili.
In questa azienda la scocca metallica della porta veniva ottenuta tramite una linea costituita da punzonatrice e pannellatrice a controllo numerico.
In quel periodo noi e tutti i concorrenti producevamo i vari semilavorati metallici (telaio, falso telaio e profilo porta) tramite piegatrici manuali.
Fu lì che per la prima volta pensammo di produrre falso telaio, telaio e profilo porta tramite profilatrice e stampi di taglio e di foratura a fine linea, proprio con la stessa tecnologia con cui producevamo gli avvolgibili.
Il ciclo di lavoro venne così totalmente rivoluzionato e semplificato.
Da un processo complesso composto da: taglio lamiera, foratura lamiera, piegatura lamiera, saldatura gambe e traverso e verniciatura si passò ad un’unica fase di lavoro.
In pratica partendo da un coil di lamiera zincata e plastificata si potevano produrre i semilavorati finiti, pronti da assemblare tramite squadrette metalliche eliminando così operazioni costose, lente e poco ecologiche come saldatura e verniciatura.
Dopo altre esperienze lavorative in diversi settori tornai nel mondo delle porte blindate in un’azienda dove implementai la tecnologia della profilatura nel processo produttivo di telai e profili di contenimento pannelli: qui finalmente potei usufruire delle ormai famose punzonatrici da coils di Dalcos.
E nel 2002 finalmente decisi di fondare una mia azienda nello stesso settore.
Fu questo il contesto in cui ebbi l’idea di produrre anche la scocca tramite punzonatrice da coil PXN e profilatrice.
Conservo ancora un magnifico ricordo sia tecnico che umano del confronto quotidiano con l’Ingegner Sergio Dallan per lo sviluppo di un prodotto innovativo che potesse coniugare tutti i vantaggi di una produzione snella ed in linea con un mercato in piena espansione.
Questi i punti di forza:
- avere un profilo su ogni linea, con produzione “just in time”: i diversi profili che costituiscono una porta vanno subito al montaggio per formare la porta completa;
- riduzione al minimo dei magazzini intermedi;
- soluzione in ottica Lean Production;
- massima flessibilità commerciale per produzione di misure speciali, con la programmazione parametrica di Dallan;
- industrializzazione spinta pur in presenza di misure variabili e optional di prodotto che possono essere configurate sulla singola porta;
Il vantaggio competitivo nei confronti dei concorrenti fu notevole e ci permise raggiungere un fatturato di 15 milioni di euro nel giro di 4 anni partendo da zero!
Oggi sfioriamo i 20 milioni di euro di fatturato e siamo secondi in Italia per numero di porte prodotte.
Il futuro? Nuovi prodotti e sicuramente nuovi impianti produttivi sempre alla ricerca di innovazione tecnica e produttiva.”
Maurizio Castignoli
Tratto dal libro “La Rivoluzione dell’Efficienza” che puoi richiedere gratuitamente cliccando QUI
Andrea Dallan
CEO – Dallan Spa