Profilatrici e linee di profilatura efficienti
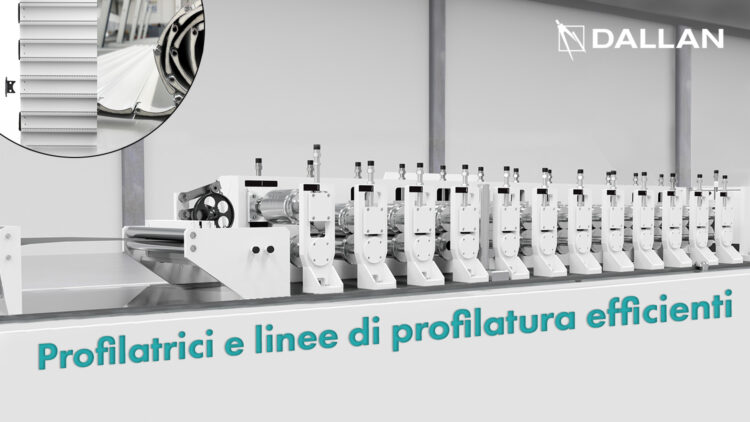
Tratto dal libro “La Rivoluzione dell’Efficienza”
RICHIEDI IL LIBRO GRATUITAMENTE
Nel 2008, quando iniziai a lavorare insieme a mio padre in Dallan, mi occupavo con lui della vendita e delle consulenze per le macchine profilatrici.
La Dallan era riconosciuta come lo specialista dei sistemi per la profilatura di lamiere sottili e questa focalizzazione fece sì che ci specializzassimo ulteriormente nei settori della finitura di interni e protezione solare.
Questi profili hanno caratteristiche particolari: sono spesso in materiale preverniciato e richiedono tolleranze ristrette, oltre all’estetica impeccabile.
In questo settore mio padre lavorava per sviluppare al meglio le relazioni che creava con i propri clienti, quindi partecipavamo spesso a fiere di settore; fiere dove potevamo incontrare i nostri clienti e ascoltare i loro problemi.
Nel corso del tempo, potei catalogare i problemi principali che affrontavano in quattro categorie strettamente interconnesse, legate ai principi di Efficienza, Produttività, Flessibilità e Automazione.
In pratica, queste sono quattro dimensioni su cui valutare l’investimento e non è sufficiente la produttività come singolo parametro di valutazione!
Se la macchina, ad esempio, non è flessibile, richiede molta manodopera, è complicata da utilizzare e programmare, o spreca molta materia prima ed energia potrebbe portare a una perdita, invece di migliorare i margini.
Inizieremo qui dall’analisi dell’Efficienza e vedremo come il suo miglioramento produce sempre vantaggi anche nelle altre tre dimensioni.
L’Efficienza nei sistemi di produzione
Le aziende che lavorano la lamiera sono tormentate dalle inefficienze che affliggono il processo di lavorazione. Inefficienze che sono di diverso tipo.
La più evidente – e la più facile da calcolare – sono gli sprechi di materia prima.
Specialmente quando si lavora con ciclo tradizionale da foglio, i sistemi di lavoro classici (punzonatura, taglio laser e piegatura o pannellatura) hanno abituato le aziende a percentuali di scarto fino al 20%.
Spesso capivo che molte aziende consideravano questa percentuale di scarto come “fisiologica di processo”.
Il valore della materia spesso arriva all’80 percento del costo di produzione.
Per questo motivo, ogni punto percentuale di risparmio in questo senso si traduce in grandi risultati in bilancio.
Un altro tipo di inefficienza era dovuta alla complessità del ciclo di lavorazione.
Spesso il processo non era stato correttamente bilanciato per la presenza di numerosi colli di bottiglia e l’azienda era costretta a creare magazzini di semilavorati senza alcun valore per il cliente, ma che causavano altri tre grandissimi problemi.
Il primo problema era l’aumento del volume del work in progress, che spesso cresceva fino a eguagliare, in valore, il magazzino di materia prima grezza.
Il secondo problema era lo spazio occupato e il terzo grandissimo problema era che questi prodotti dovevano essere fisicamente movimentati, presi e deposti da una persona non produttiva, ma addetta alla logistica.
Il valore per il cliente finale? Zero.
Pensiamo a un’azienda di lavorazione lamiera di tipo job shop.
Il materiale viene punzonato e i prodotti punzonati vengono accatastati per essere portati alla piegatrice o alla pannellatrice.
Qui una persona o un robot deve a sua volta prendere il pezzo, caricarlo in macchina e scaricarlo una volta finito.
E questo è l’esempio più semplice.
Il problema è che i costi del magazzino intermedio di semilavorati includono la superficie occupata, le persone che se ne devono occupare, il costo del materiale e la corretta attribuzione del valore aggiunto della lavorazione eseguita sono talmente complessi da calcolare, che molte aziende preferiscono semplicemente non vederli.
Un secondo esempio molto interessante sull’inefficienza della logistica di processo riguardava le aziende che producono profili per cartongesso.
Qui la Dallan era molto conosciuta in quanto fornitrice di impianti di profilatura per i principali leader europei di questo settore, oltre a moltissime piccole e medie aziende.
In questo settore la produzione del profilo era relativamente semplice e molte aziende erano già attrezzate con nostre profilatrici di velocità variabile da trenta fino a centoventi metri al minuto.
Il vero problema è che il profilo in sé aveva poco valore aggiunto fino a che non era correttamente imballato e reso disponibile per la spedizione.
Quindi erroneamente, le aziende vedevano il loro ciclo di produzione terminare con la realizzazione del profilo quando successivamente i costi esplodevano per:
- eccessivo spazio necessario alle operazioni di accoppiamento ed imballo,
- grande quantità di materiale profilato senza valore aggiunto depositato tra una stazione di imballo e la successiva,
- oltre naturalmente alla necessità di personale ulteriore non solo per eseguire l’imballo, ma anche per movimentare i pacchi piccoli e grandi tra le diverse stazioni di imballo e il magazzino dei pacchi finiti.
Questo è molto importante perché i sistemi di imballo automatici per cartongesso riducono lo spazio complessivo della trasformazione e permettono di arrivare dal coil al prodotto completamente imballato.
Chiamiamo questi sistemi Coil To Pack e qui possiamo vedere un impianto in funzione:
Lavoravo inoltre molto con aziende del settore delle tapparelle in alluminio schiumato. Questo era un mercato dove Dallan era ed è riconosciuta come leader a livello mondiale, in quanto anche qui avevamo fornito i principali produttori europei, sudamericani e fino alla Russia e alla Cina.
I nostri clienti principalmente producevano le tapparelle in barre di lunghezza sei metri; queste venivano imballate e vendute ad aziende che le tagliavano a misura e le usavano per confezionare i teli di tapparella finiti.
Altre volte erano i nostri clienti a tagliare le barre e a confezionare i teli finiti direttamente in azienda, usando macchine stand-alone.
Entrambi questi sistemi, però, introducevano inefficienze importanti nel processo che portava dal coil al prodotto finito.
Infatti, per prima cosa lavorando da barre queste devono essere tagliate a misura e si genera sempre uno scarto che a seconda della dimensione del telo va dal 5 al 12 percento.
Solo calcolando il costo di alluminio e poliuretano, si trattava in molti casi di centinaia di migliaia di euro di scarti che potevano essere risparmiati in origine!
Il secondo problema era il costo del magazzino delle barre, che potevano essere di profili con dimensioni differenti, forate e non forate, colori e finiture differenti.
Un grandissimo valore immobilizzato.
La terza inefficienza era dovuta alla necessità di movimentare le barre dal magazzino alle stazioni di lavoro: questo richiedeva naturalmente personale, attrezzature e manovre complicatissime e con il rischio costante di danneggiare la superficie dei profili che erano pre-verniciati e prefiniti.
I sistemi di lavorazione automatici più moderni permettono anche qui di passare direttamente dal Coil al telo di tapparella completamente finito, senza scarti e pronto da montare.
Chiamiamo questi sistemi Coil To Window e qui possiamo vedere uno di questi impianti in funzione:
Jean Germanaz, direttore tecnico del gruppo francese Stella che impiega complessivamente 12 linee Coil To Window Dallan, spiega le potenzialità di questo sistema di produzione.
“La collaborazione tra Dallan e Profalux cominciò più di vent’anni fa esattamente tra il 1999 e il 2000.
A quell’epoca Profalux utilizzava una macchina tedesca ormai vecchia, per produrre un profilo di lama piana da 40mm di altezza e volevamo realizzare il profilo divenuto il più venduto nel gruppo Stella, la lama da 39mm bombata. A quell’epoca avevamo stretto i contatti con l’Ingegner Dallan, il padre di Andrea, che a quel tempo stava completando i suoi studi in Germania.
La società La Toulousaine, che faceva parte del nostro gruppo era già dotata di alcune macchine Dallan.
Precedentemente al sistema automatico di Dallan, la produzione dei teli partiva da profili di lunghezza circa 6 metri, comprate da un produttore Europeo. Le lame erano di diversi colori, forate e non forate: dovevano essere stoccate su delle scaffalature apposite, tagliate a misura… con un tasso di scarto relativamente importante. L’assemblaggio si faceva su delle macchine semi automatiche e le lame erano bloccate con dei tappi in plastica.
La prima macchina non fu una macchina “full Dallan”. Realizzava infatti solo il profilo schiumato e il taglio profilo. I profili singoli erano in seguito montati su una macchina speciale, ancora con dei tappi in plastica! A quell’epoca le più grandi difficoltà erano di ordine informatico. Cominciammo a veder funzionare le macchine a partire dai file e dalle liste di lavoro generate dal nostro gestionale ERP.
Quello che mancava era far dialogare le macchine di diversi fornitori tra di loro e questo non è mai semplice.
Le tecnologie Dallan offrono per queste produzioni numerosi vantaggi come ad esempio:
- In una lunghezza di 45 metri, passiamo dal coil di materia prima al telo assemblato, pronto per essere montato come prodotto finito
- La produzione di un telo può richiedere da 3 minuti fino ai 10 minuti dei teli più grandi
- Zero magazzino intermedio tra la bobina e il telo finito
- Un tasso di scarto estremamente basso (meno del 3%) oltre a soluzioni interessanti per ridurre ancora lo scarto di materiale
- Un solo operatore per produrre fino a 450m2 al giorno
- Delle innovazioni Dallan come la chiusura del telo con lavorazione meccanica, per evitare che i profili scorrano tra di loro trasversalmente
Dallan è riuscita anche a rispondere positivamente alle altre richieste specifiche che abbiamo fatto, come ad esempio l’aggiunta di piccole viti in plastica sul lato del profilo ed inoltre:
- Aspi ad asse verticale, che permettono di lavorare con i coil direttamente dal pallet con cui vengono consegnati
- Cabine di insonorizzazione per la riduzione del rumore
- Abbiamo migliorato il livello di sicurezza della nostra produzione
- E abbiamo anche migliorato la gestione e la qualità della schiuma di poliuretano.
Il gruppo Stella France include le aziende Profalux, Eveno, La Toulousaine, Flip e Sofermi. In tutto abbiamo 17 linee in utilizzo, incluse 3 linee di tubo e 2 linee per serrande e quattro nuove linee in ordine.
Dallan è certamente il fornitore del gruppo con il quale il legame è più forte.” – Jean Germanaz
(Tratto dal libro “La Rivoluzione dell’Efficienza” di Andrea Dallan, 2020)
Vuoi più informazioni sui sistemi di profilatura automatici per profili di tapparella e cartongesso?
Contatta QUI i nostri ingegneri!
Andrea Dallan
CEO – Dallan Spa