Waste Reduction in Coil Production: Maximizing Efficiency with the Dallan Method
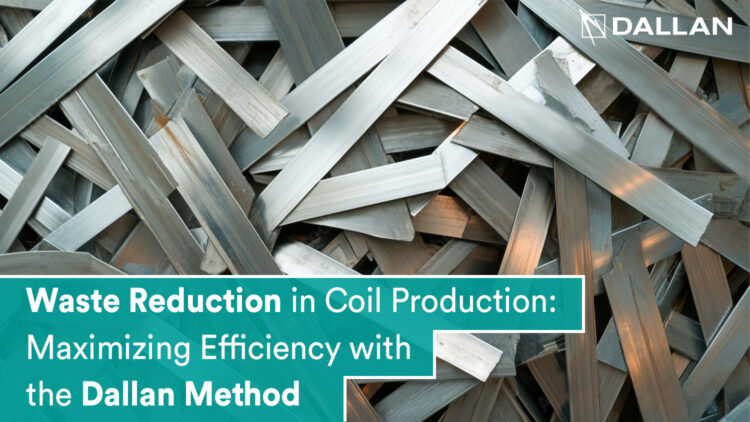
In the world of Lean Production, reducing waste is one of the main goals.
But often, when working with traditional sheet-based methods, waste becomes invisible: it’s considered a normal part of the process and accepted as inevitable.
The truth is that there are technologies – such as coil-based production – that drastically reduce waste while improving both quality and productivity.
Here are three real-life cases showing how the Dallan approach delivers measurable results in terms of material, energy, and cost savings.
Punching and Laser Cutting: Coil VS Sheet
When working from sheet, whether using punching machines or flatbed lasers, you need to “nest” parts within the sheet to optimize space.
This leads to:
- Empty spaces between parts
- Unusable trim waste
- Irregular-shaped scraps
Result? Material waste often exceeds 20%.
With Dallan’s coil-based punching (EXN) and laser cutting (LXN) technologies:
- Parts are produced inline
- The coil strip matches the product width
- No lateral trimming is needed
- Material is used down to the last millimeter
🔧 Some customers working with long coil-based parts have achieved up to 60% raw material savings, as documented in The Efficiency Revolution book.
🎥 Watch the videos:
Roller Shutter Production: From Bars to Coil To Window
In the world of foam-filled aluminum shutters, traditional bar-based production with manual assembly involves:
- An average scrap of 15%
- Higher handling
- High assembly and storage costs
With annual volumes of 2.5 million meters, this means hundreds of thousands of euros wasted.
With the Dallan Coil To Window system:
- It starts from pre-painted coil
- The curtain is assembled and cut to length inline
- End caps and mechanical stop are also applied
📉 Real-world result: over €650,000 saved per year in materials, time, and labor.
🎥 Watch the system in action:
Energy Savings: From Hydraulic Units to Full Electric
Energy is a precious resource too. Traditional machines with hydraulic units consume more energy, are noisier, and require more maintenance.
Dallan Full Electric lines:
- Use only servo-electric actuators
- Operate at up to 120 meters/min
- Offer superior precision
- Are quieter and more reliable
⚡ Energy savings of up to 34%, with measurable reductions on energy bills. Over the course of a year, these savings translate into tens or hundreds of thousands of euros depending on your production volume.
Want to calculate savings for your production?
Every company has different products and processes. That’s why we offer a free consultation:
📩 Write to [email protected] and receive a copy of The Efficiency Revolution with practical examples and formulas.
Together, we’ll discover how much you can save on raw material, energy, and time in your production process.
🔜 Next article
👉 Flexibility – How to produce small batches Just in Time quickly and without waste, thanks to coil processing