¿Es realmente tan complicado el perfilado?
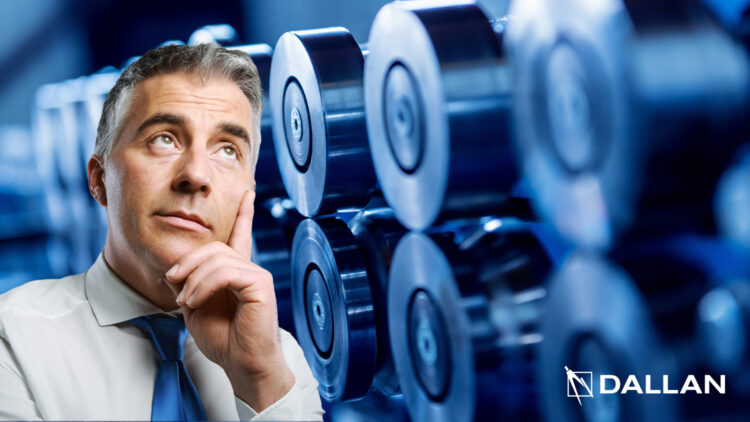
Antes de fundar Dallan, mi padre trabajaba en una empresa que producía chasis metálicos, la sociedad Secco.
Secco era líder en el perfilado de chasis para puertas y ventanas, y de Secco salieron técnicos y empresarios de la envergadura de Massimo Colomban (Permasteelisa) y Sergio Dallan 🙂
Por entonces, mi padre me contaba que el perfilado era todavía un oficio para artistas, donde los “magos” del perfilado sabían qué rodillos y qué pasos ajustar para que quedaran bien los perfiles. A menudo, utilizaban piezas de madera y herramientas ocasionales para obtener el perfil correcto.
¡Un proceso que no tenía nada de industrial a pesar del tamaño de la empresa!
Extraído del libro «La Revolución de la Eficiencia»
SOLICITE EL LIBRO GRATIS
Mi padre estaba estudiando en la universidad mientras trabajaba y casi había terminado su tesis de doctorado sobre un sistema de chorro de agua, cuando decidió cambiar completamente de proyecto. Escribió una tesis sobre el perfilado de los perfiles ligeros, un giro esencial en la historia de nuestra empresa.
Ya en 1973, mi padre tenía en mente los materiales finos.
Reunió todos los estudios disponibles en la época y acabó su trabajo en poco tiempo, desarrollando un algoritmo iterativo para calcular las fases del plegado que más tarde se convirtió en el programa de la empresa que seguimos utilizando todavía hoy.
Para trabajar chapas finas, los parámetros que hay que tener en cuenta son diferentes a los materiales gruesos por ejemplo:
Es mucho más difícil calcular los grandes radios de plegado
Ligeras diferencias en las características de los materiales modifican el retorno elástico
Además, en los modernos programas de simulación, las chapas finas son más complejas al necesitar mesh (reparticiones) mucho más pequeñas y esto aumenta bastante la complejidad y la duración de los cálculos.
El algoritmo que mi padre creó y perfeccionó ofrecía de inmediatos excelentes resultados en los perfiles finos. También diseñó un programa en lenguaje Fortran VI y fue al CED de Milán para calcular el desarrollo de las primeras flores.
En los años siguientes, salieron los primeros plotters y todavía tenemos en la empresa la primera flor diseñada por el programa de mi padre.
Cuando acabó la carrera, quiso incorporar a la empresa este nuevo instrumento, que quitaba un poco de “magia” y recortaba, en parte, el papel de los técnicos “expertos”.
Por eso, es fácil entender por qué esta innovación no fue bien recibida y encontró resistencia.
Quería poder aplicar su tesis en el trabajo de diseñador y, por ese motivo –y, además, añadiría él, porque era un poco presuntuoso e inconsciente –, a los 33 años dejó la empresa y con su dinero y el de mi madre fundaron Dallan.
El Ingeniero y la simplicidad del perfilado
Cuando mi padre se independizó, no tenía experiencia como director de empresa, ni un historial con el que darse a valer ante la competencia.
Por entonces, solo tenía su título de estudios. Fundó la empresa con el nombre de “Dallan Ing. Sergio” que conservó durante los primeros años.
Los primeros colaboradores lo llamaban siempre Ingeniero y, todavía hoy, después de cuarenta años trabajando a su lado siguen llamándolo así.
Incluso Fabrizio, que fue el primer técnico que contrató en 1978 y todavía sigue hablándole de usted.
También para muchos de nuestros clientes mi padre ha seguido siendo el Ingeniero. Esto siempre me ha fascinado y también me influyó cuando decidí lo que quería estudiar.
La comparación con los especialistas del perfilado fue uno de los motivos por los que mi padre, además de especializarse en los perfiles finos, decidió que las máquinas Dallan también tenían que ser fáciles de regular y de utilizar por personal no especializado.
Por tanto, con el tiempo, empezó a crear diferentes innovaciones para dotar el proceso de perfilado de puntos de referencia fijos que permitieran a los técnicos montar los rodillos respetando rigurosamente los parámetros del proceso. Después introdujo el árbol inferior de altura fija y un sistema de alineación para todos los rodillos de la serie, gracias a los anillos de alineación rectificados en la base de cada árbol.
Estos dos dispositivos innovadores ya estaban esbozados en los primeros modelos de cabezales y se han ido perfeccionando constantemente.
Además, en los años siguientes, también introdujo:
- el sistema del calibrador, una escala graduada que permitía al operador restaurar en todo momento las regulaciones de fábrica del grupo de rodillos
- el diseño de los rodillos con cojinetes calibrados, un sistema que permite regular el grupo para diferentes espesores empleando un pie de rey a los dos lados externos del grupo
- el calibrado con sistema de medición láser de los distanciadores de alineación
- y, sobre todo, introdujo el sistema Combi, que acelera considerablemente el cambio de producción gracias al cabezal montado con un introductor y una enderezadora en una placa de aluminio. Este sistema ofrecía, y sigue ofreciendo, como hemos visto, una extrema flexibilidad y una gran tranquilidad al operador al estar ya todos los rodillos montados en la máquina. Solo queda hacer el calibrado una vez introducido el primer material.
La calidad de los perfiles metálicos de chapa fina y prelacada
Después de 1984, como ya hemos visto, mi padre decidió especializarse definitivamente en las chapas finas.
Las chapas de menos de dos milímetros representaban una gran parte del mercado, ¡pero era difícil decir que no a los clientes potenciales, cuando en la empresa todavía había poca actividad!
De todas formas, después de la primera máquina para lamas que se vendió en la feria del Saie, Dallan empezó a hacerse un nombre como especialista en el sector de los falsos techos.
En este sector se utiliza una gran cantidad de cintas de chapa y aluminio prelacadas y preacabadas, y los perfiles tienen una función estética, a menudo sin película de protección.
Estos materiales son aún más difíciles de fabricar que los perfiles de cintas brutas o chapa galvanizada debido a dos motivos:
- Los rodillos tienen velocidades periféricas diferentes según la distancia del eje del árbol y, por este motivo, en los puntos de contacto con el material prelacado tienen siempre una velocidad diferente a la del eje neutro del perfil. Por eso, entraña un rozamiento y el riesgo de arañar o dañar la superficie del perfil;
- Además, cada tipo de laca posee una elasticidad diferente. En los radios de plegado más pequeños, la laca externa se extiende con respecto al eje neutro del plegado. Si el radio de plegado es demasiado pequeño y la laca es muy poco elástica, el revestimiento empieza a presentar grietas que dejan entrever el material subyacente, algo que hay que evitar sin falta.
El primer problema se resuelve diseñando la serie de rodillos teniendo en cuenta la posición del eje neutro y dejando los espacios apropiados en las zonas críticas. Además, la laca tiene que ser adecuada para el proceso de perfilado y resistente a los arañazos y la abrasión, conforme a los métodos de test indicados, por ejemplo, según las normativas EN 13523-12 y EN 13523-16.
La solución al segundo problema reside en la concepción del perfil: los radios de plegado más pequeños tienen que respetar las características de elasticidad del revestimiento, que están definidas en la norma EN 1396.
Después de los tests test, los revestimientos quedan clasificados en T0, T0, 5, T1 dependiendo de que la laca tolere radios de plegado de 0 veces el espesor (plegado-aplastamiento), 0,5 veces el espesor o iguales al espesor.
También hay materiales tipo T1, 5 o T2 donde la laca tiene una elasticidad muy baja y los radios de plegado internos deben ser superiores al doble del espesor.
En las chapas finas, se trabaja con revestimientos orgánicos cuyas capacidades se sitúa entre T0, 5 y T1. Por tanto, durante la fase de concepción del perfil, preferimos adoptar radios internos superiores a 0,8 veces el espesor del material.
Gracias al gran trabajo realizado durante tantos años en el sector de las lamas y los perfiles prelacados, mi padre y yo decidimos hace poco cambiar el texto descriptivo de la empresa “Soluciones y Sistemas para la fabricación de la chapa” a “Soluciones y Sistemas para chapas finas y perfiles estéticos”.
Las chapas finas necesitan más medidas de precaución que las chapas de espesor medio y, a menudo, presentan más problemas.
Por eso, llamamos a nuestras máquinas Perfiladoras de Precisión.
Extraído del libro «La Revolución de la Eficiencia»
SOLICITE EL LIBRO GRATIS
Andrea Dallan
CEO – Dallan Spa