Perfiladoras y sistemas de producción eficientes
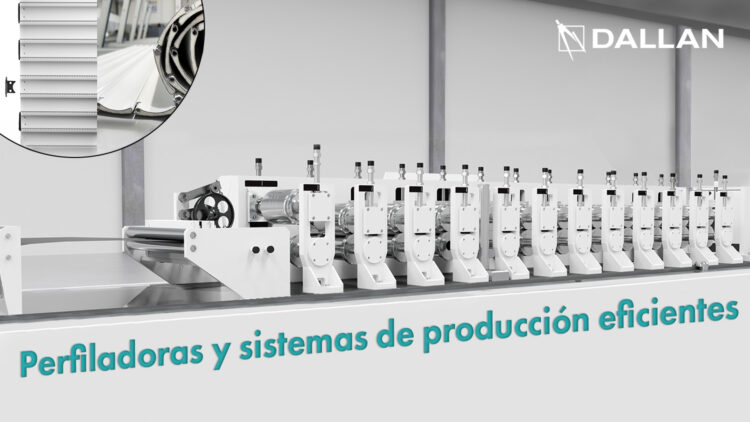
Desde 2008, además de estos trabajos sobre las punzonadoras y el láser, he tratado de mejorar –junto con mi padre– las ventas y los consejos relativos a los sistemas de perfilado.
Dallan estaba considerada como la especialista indiscutible en sistemas de perfilado de planchas finas y esa experiencia nos llevó después a especializarnos en los sectores del acabado de interiores y la protección solar.
Estos perfiles presentan características especiales: a menudo, están compuestos de materiales prelacados, exigen tolerancias reducidas y una estética impecable.
Extraído del libro «La Revolución de la Eficiencia»
SOLICITE EL LIBRO GRATIS
En este sector, mi padre trabajaba para mejorar al máximo las relaciones que establecía con sus clientes. Por eso, participábamos con frecuencia en ferias del sector, donde podíamos quedar con nuestros clientes para escuchar sus problemas.
Con el paso del tiempo, he podido catalogar los problemas principales a los que se enfrentaban en cuatro categorías estrechamente relacionadas entre sí: la Eficiencia, la Productividad, la Flexibilidad y la Automatización.
Concretamente, la inversión se tiene que valorar en base a estos cuatro criterios, ¡la productividad no es la única valoración que hay que tener en cuenta!
Por ejemplo, si una máquina no es flexible y necesita mucha mano de obra, si es difícil de usar y programar o desperdicia una gran cantidad de materia prima y energía, generará pérdidas en lugar de aumentar los márgenes.
Empezaremos analizando la Eficiencia y veremos que, al mejorarla, beneficiará sistemáticamente a las otras tres dimensiones.
La Eficiencia en los sistemas de producción
Las empresas que fabrican planchas se ven afectadas por los fallos que sufre el proceso de fabricación. Estos fallos son de diferentes tipos.
El más evidente –y más fácil de calcular– afecta a los desechos de materia prima.
En particular, cuando se trabaja la chapa a partir de formatos, los sistemas de transformación tradicionales (punzonado, corte láser y plegado o panelado) han llevado a las empresas a unos porcentajes de desechos de hasta el 20 %.
Con frecuencia, observaba que muchas empresas consideraban este porcentaje de desechos como inherente al proceso”.
A menudo, el valor de la materia primare presenta el 80 por ciento del coste de producción. Por este motivo, cada punto de porcentaje de ahorro en la disminución de desechos se traduce en grandes resultados en los beneficios finales.
Otro tipo de fallo se debía a la complejidad del ciclo de transformación.
A menudo, el proceso no se compensaba correctamente debido al gran número de cuellos de botella y la empresa se veía obligada a crear almacenes de productos semiacabados sin ningún valor para el cliente y que causaban otros tres grandes problemas.
El primer problema era el aumento del volumen del trabajo en curso, que crecía hasta igualar en valor al stock de materia prima en bruto.
El segundo problema afectaba al espacio que se ocupaba y el tercer gran problema era que una persona no productora, pero encargada de la logística tenía que manipular, coger y depositar físicamente estos productos.
¿El valor para el cliente final? Cero.
Pensemos en una empresa de fabricación de chapa tipo job shop. El material se punzona y los productos punzonados se apilan para llevarlos a la plegadora o a la paneladora.
Aquí, una persona o un robot, a su vez, tiene que coger la pieza, cargarla en la máquina y descargarla una vez terminada.
Y este es el ejemplo más simple. El problema es que los costes de los stocks intermedios de productos semielaborados incluyen la superficie ocupada, las personas que tienen que gestionarla, el coste del material y la correcta atribución del valor añadido del trabajo realizado son tan difíciles de calcular, que muchas empresas prefieren ignorarlos sin más.
Un segundo ejemplo muy interesante de la ineficiencia de la logística del proceso afectaba a las empresas que producen perfiles de cartón-yeso.
Aquí, la sociedad Dallan era muy conocida como proveedora de instalaciones de perfilado por los principales líderes europeos del sector y por muchas pymes.
En ese sector, la producción de perfiles era relativamente fácil. Muchas empresas ya estaban equipadas con nuestras perfiladoras de velocidad variable que va de treinta a ciento veinte metros por minuto.
El verdadero problema era que el propio perfil tenía poco valor añadido hasta que no estaba correctamente embalado y preparado para su envío. Por tanto, las empresas cometían el error de pensar que su ciclo de producción terminaba con la fabricación del perfil, mientras que los costes se disparaban debido a:
el excesivo espacio reservado para las operaciones de acoplamiento y embalaje,
la gran cantidad de piezas perfiladas sin valor añadido pero depositadas entre una estación de embalaje y la siguiente,
además de la necesidad de más personal no solo para que se ocupe del embalaje, sino también para desplazar los paquetes pequeños y grandes entre las diferentes estaciones de embalaje y el almacenado de paquetes terminados.
Esto es muy importante porque los sistemas de embalaje automáticos para cartón-yeso reducen el espacio total de la transformación y permiten pasar de la bobina al producto totalmente embalado.
A estos sistemas los llamamos Coil To Pack y aquí podemos ver una instalación en funcionamiento:
También trabajaba mucho con empresas fabricantes de persianas enrollables de aluminio inyectado con espuma. En este mercado, la empresa Dallan ya era reconocida como líder a nivel mundial, dado que aquí también abastecíamos a los principales productores europeos, sudamericanos, rusos y chinos.
Nuestros clientes producían principalmente persianas enrollables con barras de seis metros de largo. Estas se embalaban y se vendían a empresas que las cortaban a medida y las usaban para fabricar lamas de persianas enrollables.
A veces, nuestros clientes cortaban las barras y fabricaban las lamas directamente en sus locales con la ayuda de máquinas automáticas.
Pero los dos sistemas presentaban importantes fallos en el proceso que iba de la bobina al producto acabado.
En efecto, el corte a medida de las barras entrañaba grandes cantidades de desechos que variaban según el tamaño de la persiana enrollable y podían alcanzar entre el 5y el 12 por ciento. ¡Solo el coste del aluminio y el poliuretano representaba cientos de miles de euros de desechos que se podían ahorrar desde el principio!
El segundo problema afectaba al coste del almacenamiento de las barras, que podían ser de perfiles de diferentes tamaños, agujereados o no, con colores y acabados diferentes. Un gran valor inmovilizado.
El tercer fallo se debía a la necesidad de llevar las barras del almacén a las estaciones de trabajo. Naturalmente, estas operaciones requerían personal, equipamiento y maniobras muy complicadas, por no mencionar el riesgo permanente de dañar la superficie de los perfiles que estaban prelacados y preacabados.
Los sistemas de fabricación automáticos más modernos permitían también en este caso pasar directamente de la bobina a la persiana enrollable completamente acabada, sin desechos y lista para su instalación.
A estos sistemas los llamamos Coil To Window y aquí podemos ver una de estas instalaciones en funcionamiento :
Jean Germanaz, director técnico del grupo francés Stella que utiliza 12 líneas Coil To Window Dallan, explica las posibilidades de este sistema de producción.
«La colaboración entre Dallan y Profalux comenzó hace poco más de veinte años, exactamente entre 1999 y 2000.
Por entonces, Profalux utilizaba una máquina alemana, que hoy se ha quedado obsoleta, para producir un perfil de chapa plana de 40 mm de altura y queríamos realizar el perfil que se había convertido en el más vendido del grupo Stella, la chapa abombada de 39 mm. En aquella época, colaborábamos estrechamente con el Ingeniero Dallan, el padre de Andrea, que por entonces estaba completando sus estudios en Alemania.
La sociedad La Toulousaine, que formaba parte de nuestro grupo ya contaba con algunas máquinas Dallan.
Antes de usar el sistema automático de Dallan, la producción de las persianas enrollables empezaba con perfiles de unos 6 metros de largo, comprados por un productor europeo. Las lamas eran de diferentes colores, agujereadas o no. Se tenían que guardar en estantes especiales, cortar a medida… con un porcentaje de desechos relativamente importante. El embalado se hacía en máquinas semiautomáticas y las lamas se bloqueaban con capuchones de plástico.
La primera máquina no fue una “full Dallan”. De hecho, solo realizaba el perfil inyectado con espuma y el corte del perfil. Solo los perfiles se montaban después en una máquina especial, ¡todavía con tapones de plástico! Por entonces, nuestros mayores problemas tenían que ver con la informática. Empezamos a poner en funcionamiento las máquinas a partir de archivos y listas de trabajo que generaba nuestro sistema de gestión ERP.
El problema era hacer que las máquinas de diferentes proveedores fueran compatibles entre sí y eso nunca es fácil.
La tecnología Dallan ofrece numerosas ventajas para este tipo de producciones como, por ejemplo:
- En una longitud de 45 metros, pasamos de la bobina de materia prima a la lama embalada, preparada para ser instalada como producto acabado
- La producción de una lama puede exigir de 3 a 10 minutos en el caso de las lamas más grandes
- Cero stock intermedio entre la bobina y la lama acabada
- Un porcentaje de desechos realmente bajo (menos del 3 %) y soluciones interesantes para reducir más el desperdicio de material
- Un solo operador para producir hasta 450 m2 al día
- Innovaciones Dallan como el cierre de la persiana enrollable con sistema mecánica para evitar que los perfiles se deslicen de forma transversal
Dallan también ha podido satisfacer otras peticiones específicas que le hemos hecho, como, por ejemplo, añadir pequeños tornillos de plástico a un lateral del perfil y además:
- Bobinadoras de eje vertical, que permiten trabajar con las bobinas directamente en el palé donde se entregan
- Cabinas de insonorización para reducir el ruido
- Mejora del nivel de seguridad de nuestra producción
- Mejora adicional de la gestión y la calidad de la espuma de poliuretano.
El grupo Stella France incluye las sociedades Profalux, Eveno, La Toulousaine, Flip y Sofermi. En total, estamos usando 17 líneas, incluidas 3 líneas de tubo y 2 líneas de fabricación de persianas enrollables, y hemos pedido cuatro nuevas líneas.
Dallan es, sin duda, el proveedor del grupo con el que mantenemos unos vínculos más estrechos».
Contacte con nuestros ingenieros AQUÍ
Andrea Dallan
CEO – Dallan Spa