Flexibilité des lignes de formage de tôles : le système Combi pour outil
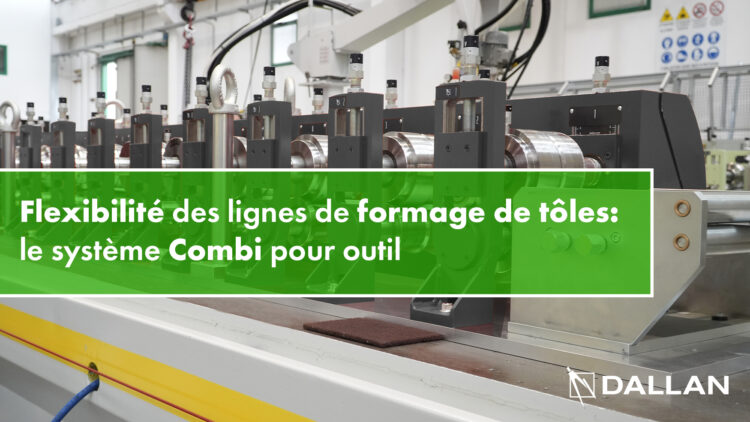
Après avoir constaté les avantages du système Combi pour les trains de galets, nous avons appliqué le même concept aux groupes de matrices qui sont installés avant ou après les profileuses.
Lorsqu’un profil a été formé, il est parfois nécessaire de compléter le travail à l’aide d’unités hydrauliques et de matrices spéciales pour emboutissage ou ouvertures particulières – qui ne peuvent être effectuées antérieurement au profilage.
C’est ainsi qu’est né le groupe Combi électrohydraulique. Il s’agit d’une plaque en acier sur laquelle viennent se fixer :
- Des unités hydrauliques
- Des matrices
- Des systèmes de lubrification
- Des systèmes d’extraction motorisés
- Des unités pneumatiques
- Des systèmes d’insertion d’accessoires
Extrait du livre « La Révolution de l`Efficience ».
DEMANDER LE LIVRE GRATUITEMENT
Tous ces éléments sont utilisés pour un type de profil spécifique. Sur la plaque du Combi se trouvent également :
- Les raccordements hydrauliques à fixation rapide
- Les raccordements pneumatiques à fixation rapide
- Les raccordements électriques effectués avec des connecteurs à fixation rapide
Lors d’un changement de profil, la plaque du Combi est débranchée, soulevée à l’aide d’un pont roulant et posée sur un côté.
Elle est remplacée par la plaque comprenant toutes les matrices déjà installées et réglées pour le profil suivant, ce qui permet d’économiser des heures de travail pour l’installation des matrices, les réglages et les essais.
Là encore, la plaque est dotée de dispositifs de centrage spéciaux permettant un positionnement rapide.
En résumé :
- Plusieurs groupes Combi électrohydrauliques peuvent être installés en dehors de la machine en temps masqué
- Il est possible de disposer de plusieurs machines utilisant les mêmes Combi afin d’augmenter la productivité et la fiabilité et d’éliminer la nécessité de changer de produits
- Les Combi permettent de rénover la ligne lorsque les systèmes ont plus de vingt ans
La philosophie SMED, qui fait partie des outils de la Lean Production, propose un idéal de perfection vers lequel on doit tendre ponctuellement, mais également au fil du temps, en ajoutant des groupes Combi et des équipements dans le but de simplifier et d’accélérer toujours davantage les changements d’outils – si la machine a été pensée et conçue dans cette optique.
Voici comment la société Roto Okna a résolu son problème de flexibilité. Cette entreprise fait partie du groupe allemand Roto, fabricant de fenêtres pour toits. Laissons la parole à Arkadiusz Guz, responsable de production :
“ En 2013, Roto produisait environ 11 000 éléments de fenêtre par jour, avec deux équipes en rotation.
Notre processus productif était très complexe et prenait beaucoup de temps. Il comprenait les étapes suivantes :
- Le matériau était découpé longitudinalement et transversalement dans une bobine
- Il était placé sur une palette
- Il était ensuite transporté à la station de cisaillement avec l’assistance d’un opérateur
- Les pièces étaient ensuite acheminées à la station de pliage sur une presse mécanique
- Là encore, le pliage s’effectuait sur des matrices spéciales avec l’assistance d’un opérateur
Ce type de processus était totalement inefficient et nécessitait la présence de trois opérateurs qualifiés lors de chaque service.
En 2014, le conseil d’administration avait un objectif ambitieux : trouver et activer un processus en mesure de réduire le nombre de passages de 3 à 1, sans augmenter les durées de rééquipement de la machine. C’est ce problème que nous avons présenté à Dallan lors de notre première rencontre.
Parmi ses technologies, Dallan avait une solution toute prête. Il s’agissait d’une ligne de poinçonnage flexible et de profilage Combi comprenant les éléments suivants :
- Dérouleur
- Redresseuse
- Presse de poinçonnage
- Profileuse dotée des différents équipements
- Table de déchargement
Cette ligne offrait un important avantage : le système de changement rapide des galets et des matrices, installés en groupes sur des bases en aluminium ou en acier (Combi). Dans notre cas, la durée requise pour ce changement étaitde 20 minutes avec l’intervention de deux opérateurs.
La solution proposée par Dallan nous a permis de réduire le nombre d’opérateurs nécessaires à la production de 3 à 1, en maintenant le temps de changement de profil à 20 minutes.
Un autre aspect très positif de cette solution est la possibilité d’automatiser le processus de réception et de palettisation des pièces. Ceci sera notre prochaine étape dans la direction de l’amélioration continue. ”
Arkadiusz Guz
Extrait du livre « La Révolution de l`Efficience ».
DEMANDER LE LIVRE GRATUITEMENT
Andrea Dallan
CEO – Dallan Spa