Le Cash Flow d’un système Coil To Window
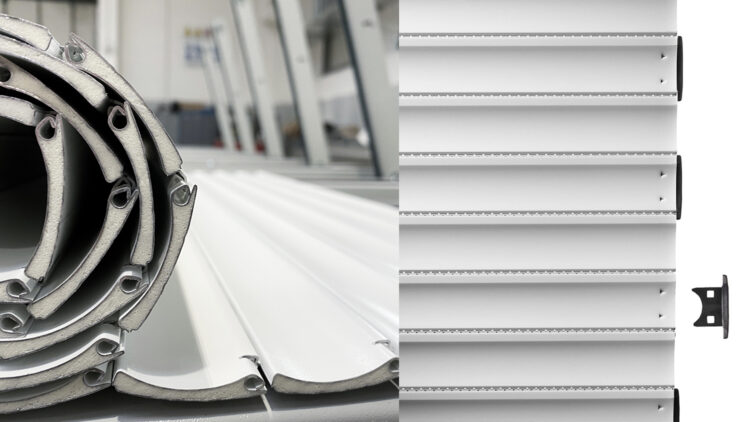
Je vais à présent vous expliquer comment les systèmes Coil to Window peuvent permettre au producteur de volets roulants finis de réaliser des économies de plus de 200 000 euros par an, quels sont les principaux facteurs générant des économies aussi substantielles et pourquoi ce système de production est beaucoup plus durable et écologique que les systèmes traditionnels.
Production de volets roulants en aluminium : augmenter les profits et la durabilité grâce aux systèmes Coil To Window.
Les volets roulants en aluminium mousse sont de plus en plus utilisés en Europe et au-delà en raison de leurs nombreux avantages :
- économie d’énergie (diminuent énormément les coûts de chauffage et de climatisation des bâtiments)
- vie privée
- sécurité et protection des fenêtres
- automation et domotique très simples
- haute qualité et résistance aux intempéries
Le cycle de production standard pour les volets roulants partait de barres de profils déjà moulées, d’une longueur située entre 5, 6 et 7 mètres, découpées sur mesure et assemblées en générant un taux de rebus variant entre 5 et 12 %.
Les installations Coil To Window, en revanche, produisent directement à partir de la bande continue qui provient de la bobine et permettent de fabriquer des tabliers de volets roulants complets et découpés sur mesure, avec un taux de rebus quasiment nul.
La méthode traditionnelle : production de barres déjà profilées
Le système de tabliers de volets roulants le plus courant démarre à partir de paquets de profils déjà moulés. Ces derniers sont découpés sur mesure et montés, ou transférés dans une machine qui prélève une pièce à la fois, la découpe sur mesure et l’assemble.
Les barres étant découpées sur mesure et selon la largeur de la fenêtre, une partie reste inutilisable et finit au rebus.
Le tableau suivant indique les taux de rebus pour les barres de 5,6 m de longueur, pour différentes largeurs de tablier.
Les producteurs de volets roulants ont essayé de nombreux systèmes pour diminuer ce taux de rebus, mais toutes les solutions se sont révélées très coûteuses, car elles demandaient énormément de temps et nécessitaient l’intervention d’un opérateur.
Le taux de rebus tournait généralement entre 5 et 12 %.
Le système de production Coil-to-window pour volets roulants
D’ici les trois prochaines minutes, un système COIL TO WINDOW Dallan aura produit un tablier de volant roulant fini directement à partir de bobine, sans déchets et sans l’intervention d’opérateurs experts
Les systèmes de production Coil To Window produisent des tabliers de volet roulant finis et assemblés directement à partir de bobine.
Ce type de production nécessite l’intervention d’un seul opérateur et permet d’éliminer les opérations complexes de déplacement des paquets de profils, les protégeant ainsi de tout risque de détérioration.
Les données de production de chaque tablier, comme la largeur, la hauteur et la quantité sont chargées directement à partir du bureau ou via des tableaux Excel.
S’agissant également d’une production paramétrique, il est inutile de calculer de temps de programmation pour la ligne !
Cette ligne automatique comprend :
- Dérouleur contenant la matière première (généralement de l’aluminium prélaqué)
- Profileuse de précision T4
- Système COMBI à changement rapide contenant les galets pour un modèle de volet roulant
- Machine qui mélange les composants de la mousse (généralement polyol et isocyanate)
- Bancs de maturation polymérisation de la mousse
- Scie volante qui découpe les pièces sur mesure
- Poinçonneuse effectuant les ajours de ventilation (et les alignements si nécessaire)
- Banc d’enfilage
- Système de blocage avec embouts en plastique, ou blocage mécanique sans embouts (brevet Dallan)
Cette ligne requiert la présence d’un seul opérateur durant la production, pour le contrôle qualité et le prélèvement du tablier fini.
La production de 25 000 volets nécessite entre 2 et 2,5 millions de mètres linéaires de profil par an, en fonction de la dimension des fenêtres et des profils. Nous allons à présent analyser les économies réalisées grâce à un système Coil To Window en nous basant sur ces quantités.
Économies de matériau générées par le système Coil To Window pour différentes dimensions de profil
Le tableau ci-dessous indique la quantité d’aluminium et de polyuréthane de profils d’aluminium et polyuréthane de différentes dimensions pour barres d’un mètre de long.
Le coût de l’aluminium et du polyuréthane est variable et peut être négocié avec les producteurs de ces matières premières.
Les profils de volets roulants ont été sélectionnés parmi les quelques 300 profils de volets roulants les plus significatifs du catalogue Dallan. L’offre de profils pour volets roulants en aluminium s’est segmentée pour couvrir aussi bien les profils haut de gamme que les produits d’entrée de gamme (appelés profils « ECO »).
Les profils Eco présentent généralement une largeur de bande et une épaisseur inférieures. L’aluminium, comme on le voit sur le tableau, représente entre 86 et 92 % du coût de la matière première.
La production de 2,5 millions de mètres de volets roulants génère le coût de matière première suivant. Le tableau indique également les économies réalisées grâce à la seule réduction du coût d’achat de l’aluminium et du polyuréthane, avec des réductions de matière première respectives de 5 % et 12 %.
Remarque importante : les volumes et les économies indiqués sont obtenus en calculant le seul coût de l’aluminium et du polyuréthane économisé. Lorsque l’on doit acheter les barres de profils, les économies sont deux à trois fois plus importantes, car la marge commerciale du fournisseur inclut le coût de la matière première ainsi que :
- les coûts de transformation
- les coûts d’énergie
- les coûts de main-d’œuvre
- les coûts d’expédition
- la répartition des coûts fixes
- et le gain
Le poids du polyuréthane a été calculé sur la base d’une mousse en polyuréthane de faible densité, et les valeurs des coûts d’aluminium et de polyuréthane se réfèrent aux valeurs d’octobre 2016.
La production annuelle d’une installation Coil To Window travaillant jusqu’à 37 mètres par minute et 220 jours par an représente entre 2 et 2,5 millions de mètres en une seule tournée ou une seule équipe ? . Cette valeur peut varier en fonction des dimensions des profils, des dimensions moyennes des tabliers produits et du nombre de changements de couleurs nécessaires. Ces données sont par ailleurs confirmées par l’expérience du groupe Stella (voir témoignage au début du livre).
Lorsque l’on travaille en deux ou trois tournées ou équipes ? , les économies pour une ligne sont multipliées également par deux ou trois, et il existe par ailleurs des systèmes de production Coil To Window également pour des vitesses plus élevées allant jusqu’à 60/80 mètres par minute.
Pour une production de 2,5 millions de mètres de barres de longueur fixe, les déchets correspondent à environ 300 000 mètres linéaires de profils en aluminium et polyuréthane, qui correspondent respectivement à 30,8 tonnes d’aluminium et 2,7 tonnes de mousse de polyuréthane, utilisés ensemble dans le processus de production.
Ces matériaux sont encore plus difficiles à recycler et doivent être mis au rebus, ce qui entraîne des coûts pour l’entreprise. En réduisant les déchets, les systèmes Coil To Window réduisent l’impact environnemental de cette production tout en garantissant une rentabilité annuelle élevée pour la production de tabliers de volets roulants.
Si on analyse la technologie Coil to Window dans une perspective LEAN, on peut constater tous les avantages que la fabrication allégée peut apporter :
- Réduction et élimination des déchets
- Réduction au minimum du Work In Progress – aucun stock de produits semi-finis
- Changement de dimensions du produit en cours de cycle – possibilité de produire des tabliers différents sans arrêter la machine
- Il est inutile de programmer la machine – la ligne lit directement les ordres de production à partir du système ERP du client
- Main-d’œuvre réduite au minimum – la production de tabliers de volets roulants pour 2,5 millions de mètres nécessite généralement au moins 4 personnes, contrairement à une ligne Coil To Window qui nécessite un seul opérateur, même non expert
En matière d’efficience, les technologies les plus innovantes introduisent de nouveaux paradigmes, augmentent la productivité, l’efficience et la durabilité de la production ainsi qu’une plus grande automation tout en réduisant au moins d’un quart la main-d’œuvre normalement requise pour produire la même quantité de tabliers.
La technologie Coil To Window représente une opportunité de bénéficier des avantages suivants :
- une automation plus importante
- un processus léger et continu
- zéro programmation
- contrôle qualité en ligne, y compris automatique
- intégration dans les systèmes ERP de l’entreprise.
Dans ce chapitre, nous avons vu pourquoi la technologie Coil To Window la plus avancée entraîne des économies de 5 à 12 % sur la matière première, et notamment comment elle permet de réaliser des produits de qualité supérieure avec moins de matière première et moins de déchets.
Ainsi, la production de tabliers pour volets roulants est encore plus rentable, durable et écologique.
Cliquez sur ce lien pour découvrir un système Coil To Window en fonctionnement, dans ce cas avec l’application d’embouts en plastique :
Si vous souhaitez également en savoir plus sur le système Coil to Window, mais pas seulement, inscrivez-vous à notre Masterclass en direct: chaque semaine, j’approfondirai un sujet lié à nos machines et à nos systèmes de production axés sur la Lean Production.
Pour demander l’accès, cliquez sur le lien et remplissez le formulaire!
JE VEUX M’INSCRIRE À LA MASTERCLASS
Andrea Dallan
CEO – Dallan Spa