Reshoring post covid: tre aziende su quattro riportano la produzione entro i confini nazionali
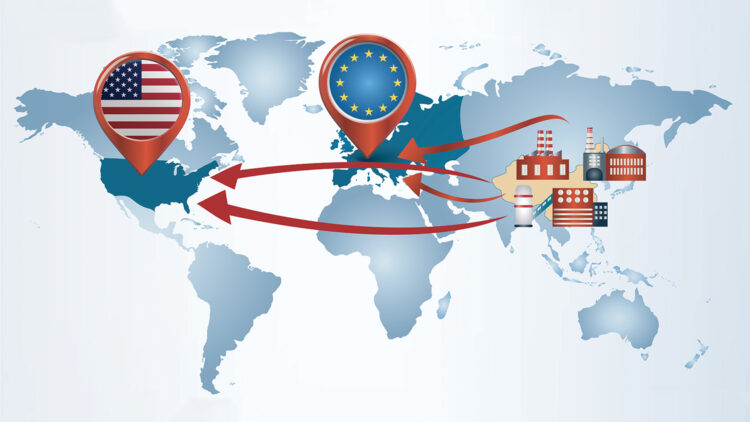
Il dato è molto interessante: in Italia tre aziende su quattro, tra quelle che avevano portato la produzione in paesi esteri, stanno riportando la produzione in patria (fonte: Istat).
Se aggiungiamo a questo il fatto che l’80% delle multinazionali ha già elaborato piani per riportare entro i confini nazionali le produzioni (dati Bank of America), ci accorgiamo che siamo di fronte a un fenomeno estremamente importante e degno di nota.
Questo fenomeno ha accelerato moltissimo dopo l’ondata pandemica, che ha aumentato la difficoltà di spostamento delle merci e delle persone.
Dunque: cos’è il Reshoring?
È la ri-localizzazione delle imprese, ed è il fenomeno opposto all’Offshoring, cioè la delocalizzazione della produzione, che andava così di moda fino a pochi anni fa, soprattutto per imprese che volevano avvantaggiarsi del basso costo della manodopera nei paesi emergenti.
L’Offshoring ha portato nel tempo problemi strategici alle aziende che hanno intrapreso questa strada.
Innanzitutto hanno esportato il loro know-how, favorendo anche la nascita di concorrenti nei paesi dove hanno portato la produzione.
Di conseguenza, il nostro tessuto produttivo si è indebolito, e le economie fino a prima emergenti si sono rafforzate fino al punto da venire anche in Europa a fare shopping di aziende ad alta tecnologia! Il caso della tedesca Kuka, acquistata da un grande gruppo cinese, ne è un esempio emblematico.
Inoltre il vantaggio del basso costo della manodopera si è progressivamente ridotto, per due ragioni fondamentali: l’aumento dei salari in molti di questi paesi, e l’automazione dei sistemi di produzione che riduce fortemente l’impatto del costo della manodopera sul costo di produzione totale.
Un altro grande problema è il controllo della supply chain che diventa molto difficile, per non parlare dei costi del mantenere e controllare una struttura produttiva all’estero.
Quindi, i costi di trasporto e le difficoltà di movimento di merci e persone non sono più compensati dai minori costi e finalmente sempre più aziende capiscono che gli svantaggi e i rischi del produrre all’esterno possono essere facilmente superati riportando la produzione entro i confini nazionali!
E questo senza aumentare i costi di produzione, anzi: permettendo di ridurli, aumentando il controllo di tutte le fasi del processo, aumentando decisamente la qualità e mantenendo al sicuro il proprio know-how, le tecniche di lavorazione e le tecnologie.
Come? Grazie ai grandi passi avanti nelle tecniche e tecnologie di produzione, all’automazione, ai sistemi basati su Industry 4.0 e ai sistemi organizzativi orientati alla Lean Manufacturing.
Reshoring: perchè l’automazione rende sempre più marginale il problema del costo della manodopera
Teniamo presente un dato: il costo di un prodotto è dato da costo della materia prima, energia, manodopera. Se energia e materia prima hanno costi simili nelle diverse zone del mondo, è chiaro il grande “plus” che spingeva le aziende a delocalizzare era il basso costo della manodopera. Che fino a dieci anni fa poteva compensare il costo della controllata estera, delle spese di spedizione e così via.
Cos’è successo nel frattempo? Semplice: i sistemi di produzione, in Italia come in Europa e Nord America, si sono spostate verso modelli sempre più industriali, snelli e automatizzati.
La Lean Production applicata alla produzione nelle nostre aziende ha permesso di ridurre sprechi e ottimizzare i processi, cosa che è molto più semplice fare nell’azienda “di casa”, piuttosto che cercare di controllare un’azienda a migliaia di chilometri di distanza.
Il fattore chiave che portava le aziende a spostarsi, cioè il basso costo del lavoro, in alcuni dei paesi ormai ex emergenti è diventato sempre meno interessante, per l’aumento progressivo dei salari.
In ogni caso, il fattore determinante è stato l’automazione. Vediamo perché.
Industria 4.0: l’automazione, l’informatizzazione e i sistemi di produzione avanzati
Quando in Germania nel 2013 si parlò per la prima volta di Industria 4.0, pochi capirono l’impatto che avrebbe avuto nel tessuto imprenditoriale e produttivo Europeo.
La Germania stava facendo i conti con un problema di perdita di competitività rispetto ai paesi emergenti, e mise a punto un piano molto strutturato che non riguardava solo le tecnologie, ma anche le infrastrutture fisiche ed informatiche del paese, arrivando a toccare anche la scuola!
Nel corso degli anni, anche gli altri paesi europei hanno abbracciato – ognuno a suo modo – il piano “Industria del futuro 4.0” e questo è riuscito a spingere le aziende a modernizzare non solo le strutture informatiche, ma anche e soprattutto i loro sistemi di produzione.
Molte aziende hanno iniziato ad investire, prima timidamente poi in modo sempre più deciso verso sistemi avanzati di produzione che non si limitano a poche fasi di lavoro, ma permettono di passare, con pochissima supervisione, dalla materia prima direttamente al prodotto finito, imballato e pronto per il magazzino o la spedizione.
Sistemi flessibili, che permettono di cambiare la produzione in tempi rapidissimi, adattandosi alle richieste del mercato come nella migliore filosofia Lean Producion.
Sistemi che permettono la programmazione e il controllo delle linee di produzione in remoto, macchine dotate di teleassistenza e di sensori per la manutenzione predittiva.
L’introduzione di questi sistemi è stata promossa e spinta anche dai governi dei diversi paesi, grazie a politiche fiscali incentivanti che hanno permesso ai primi pionieri di testare con mano l’efficacia e l’efficienza di questi sistemi. L’automazione qui è un componente fondamentale che da un lato riduce la necessità di operatori, dall’altro richiede per i supervisori competenze diverse dalla semplice macchina operatrice. Quindi è necessario che non solo le macchine si evolvano, ma anche le persone.
Non siamo più nel mercato dove una volta imparato il mestiere, te lo porti avanti tutta la vita tale e quale. Anzi: la velocità con cui cambiano le tecnologie richiede grandissima flessibilità nelle persone, capacità di formarsi e studiare.
Quando forniamo un impianto avanzato di produzione, come i sistemi Coil To Box, Coil To Window e Coil To Pack, sappiamo che la formazione è un componente essenziale per ottenere il massimo dagli impianti e per gestirli con successo nel tempo!
Per questo motivo abbiamo creato due servizi di Training specifici, che potrai trovare anche nel nostro sito. La prima sezione è dedicata principalmente ai direttori di produzione e al management, e illustra tutte le nuove tecnologie di produzione nel campo dei prodotti in lamiera sottile: è la sezione Masterclass, a cui puoi registrarti qui:
VOGLIO ISCRIVERMI ALLA MASTERCLASS
La seconda è la sezione training legata al service e all’operatività della linea. A questa sezione puoi accedere con il programma Dallan Priority, che ti permette di accedere alla teleassistenza per le tue linee Dallan e ai contenuti video registrati, suddivisi per tipo di linea e argomento: una collezione di video tutorial che si arricchisce di settimana in settimana! I video fungono da manuale per mantenere aggiornati i vostri tecnici e aiutarli a eseguire da soli la maggior parte delle operazioni di gestione linea, programmazione e manutenzione!
A questo si aggiunge il programma di Training personalizzato, che può essere eseguito in loco con la visita di uno specialista Dallan, oppure con un webinar specifico per le vostre esigenze il cui contenuto registrato vi viene fornito in esclusiva come materiale di studio.
Per maggiori informazioni, contatta subito [email protected]!
Andrea Dallan
CEO – Dallan Spa