Efficient rollforming machines and production lines
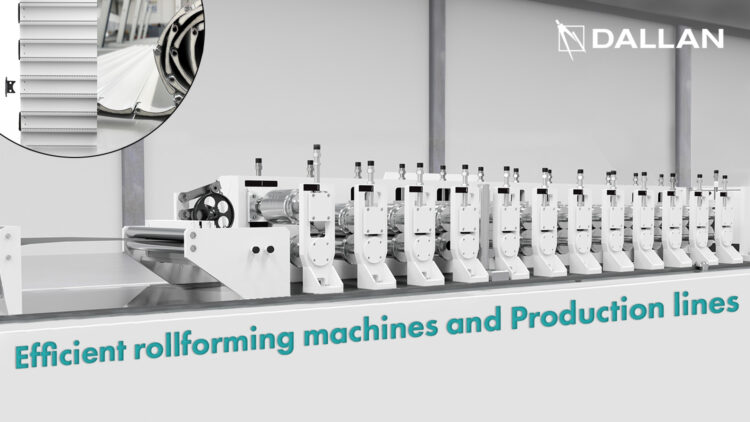
In 2008, when I started working together with my father in Dallan, I was involved with him in sales and consulting for profiling machines.
Dallan was a recognized thin sheet metal roll forming systems specialist and this focus meant that we specialized even more in the fields of interior finishing and protection from the sun.
These profiles have quite particular characteristics: they’re often made using pre-painted material and require strict tolerances, as well as impeccable aesthetics.
Taken from the book “The Revolution of Efficiency”
REQUEST THE BOOK FOR FREE
My father worked on developing the relationships he created with his customers in this field, so we often took part in trade fairs; fairs where we could meet our customers and listen to their problems first hand.
Over time, I was able to place the main problems they faced into four closely related categories, linked to the principles of Efficiency, Productivity, Flexibility and Automation.
In short, these four aspects are used to evaluate an investment, since the parameter of productivity alone is insufficient!
For example, if a machine isn’t flexible, if it requires lots of labor, if it’s complicated to use and program or perhaps wastes lots of raw materials and energy, it could prove to be a loss-maker, instead of improving margins.
Let’s start with Efficiency analysis and see how improving it always produces benefits to the other three aspects.
Efficiency in production systems
Sheet metal companies are pestered by inefficiencies that plague the manufacturing process. There are various types of inefficiencies.
The most obvious – and the easiest to calculate – is the waste of raw materials.
Especially when working with a traditional sheet cycle, traditional processing systems (punching, laser cutting and bending or paneling) have accustomed companies to waste rates as high as 20%.
I often figured out that many companies considered this percentage of waste in the process to be “physiological”.
The value of the material used often accounts for 80 percent of the production costs. That’s why every percentage point in terms of savings translates into great results for the bottom line.
Another type of inefficiency involved the complexity of the processing cycle.
The process was often incorrectly balanced due to the number of bottlenecks and the company was forced to create warehouses for semi-finished products that were of no value to the customer, but which caused three huge new problems.
The first problem was an increase in the amount of work in progress, the value of which often matched that of the raw materials stored in the warehouse.
The second problem was the space required and the third major problem was that these products had to be physically handled, picked up and deposited by a person not involved in production, but employed in logistics.
What was the value for the end customer? Nothing.
Let’s imagine a job shop type of sheet metal working company. The material is punched and the punched products are stacked so that they can be brought to the panel bender or the bending machine.
A person or a robot then takes the piece, loads it into the machine and unloads it when finished.
This is the most straightforward example. The problem is that costs for a semi-finished product intermediate warehouse, which include the cost of the surface area taken up, the people who work there, the cost of the material and the correct allocation of the added value of the processing performed, are so complex to calculate that many companies simply prefer not to take them into account.
A second, very interesting example of the inefficiency of process logistics concerns companies that produce plasterboard profiles (metal stud framing).
It’s an area in which Dallan was well known as a supplier of roll forming systems to the sector’s leading European companies, as well as many small and medium-sized companies.
In this sector, profile production was relatively simple and many companies already had our variable speed roll forming machines which went from thirty up to one hundred and twenty meters per minute.
The real problem was that the profile itself had little added value until it was properly packaged and made available for shipping. Companies mistakenly thought their production cycle ended with the creation of the profile, when in fact costs subsequently exploded due to:
Excessive amounts of space needed for pairing and packaging operations;
Large quantity of profiled material without added value deposited between one packaging station and the next;
As well as a need for additional staff, not only to perform packaging operations, but also to move small and large packages from the packaging stations to the finished package warehouse.
This was very important because automatic plasterboard packaging systems reduce the overall space needed for transformation and allow the product to go from a coil to being fully packaged.
We call these systems Coil To Pack and below we can see a system in operation (just frame the code below using the camera on your smartphone):
I also worked a lot with companies in the aluminum foam-filled rolling shutter sector. It was a market in which Dallan was and still is recognized as a world leader, having also supplied the main European, South American producers, as well as producers in Russia and China.
Our customers mainly produced rolling shutters with bars that were six meters in length; they were packaged and sold to companies that cut them to size and used them to package the finished rolling shutter curtains.
On other occasions, our customers would cut the bars and pack the finished curtains directly at their companies, using stand-alone machines.
However, both these systems introduced important inefficiencies into the process that went from the coil to the finished product.
Firstly, working with bars meant they had to be cut to size and doing so always generated waste which ranged from 5 to 12 percent, depending on the size of the curtain. A quick calculation of the cost of aluminum and polyurethane showed that, in many cases, there were hundreds of thousands of Euros in waste that could have been saved!
The second problem was the cost of the warehouse for the bars, which could have profiles of different sizes, be perforated or non-perforated and have different colors and finishes. A huge amount of value tied up in fixed assets.
The third inefficiency was due to the need to move the bars from the warehouse to the work stations: naturally, doing so required personnel, highly complicated equipment and maneuvers and there was a constant risk of damaging the surface of the pre-painted and pre-finished profiles.
Modern automatic processing systems mean it’s also possible to go directly from a coil to a fully finished rolling shutter curtain that is ready for assembly and free of waste.
We call these systems Coil To Window and below we can see one of these systems in operation:
Jean Germanaz, the technical director of French group Stella, which uses a total of 12 Dallan Coil To Window lines, explains the potential of this production system.
«Dallan and Profalux began working together more than twenty years ago, during 1999 and 2000.
At that time, Profalux was using an old German machine to produce a 40mm high flat slat profile and we wanted to make the profile that became the best-selling in the Stella group, the 39mm curved slat. At that time, we had established a relationship with Ingegnere Dallan, Andrea’s father, who was completing his studies in Germany.
The La Toulousaine company, which was part of our group, already had a few Dallan machines.
Prior to Dallan’s automatic system, curtain production started with profiles about 6 meters in length, purchased from a European manufacturer. The slats were of different colors, perforated and non-perforated: they had to be stored on special shelves, cut to size… with a relatively high waste ratio. Semi-automatic machines were used for assembly and the slats were locked into place using plastic caps.
The first machine was not a “full Dallan” machine. Indeed, it only performed profile foam-filling and profile cutting. Individual profiles were then mounted on a special machine, still with their plastic caps! At that time, the biggest difficulties involved IT. We began to see the machines operate using files and work lists generated by our ERP management system.
What was missing was the ability to make machines from different suppliers communicate with each other, which is never easy.
Dallan technologies offer numerous benefits to this type of production, such as:
Starting with a length of 45 meters, we go from a coil of raw material to the assembled curtain, ready to be assembled as a finished product;
The production of a curtain can take from 3 minutes to 10 minutes for the larger curtains;
Zero intermediate magazine from reel to finished curtain;
An extremely low waste ratio (less than 3%), as well as interesting solutions to further reduce material waste;
Only one operator to produce up to 450m2 per day;
Dallan innovations such as the curtain locking system using mechanical processing, to prevent the profiles from sliding across each other.
Dallan also managed to respond to our other specific requests, such as the addition of small plastic screws to the sides of profiles, as well as:
Vertical axis decoilers, which allow the use of coils directly from the pallet with which they’re delivered;
Soundproof booths for noise reduction;
We improved the safety levels of our production operations;
We also improved the handling and quality of polyurethane foam.
The Stella France group includes the companies Profalux, Eveno, La Toulousaine, Flip and Sofermi. In all, we have 17 lines in use, including 3 tube lines, 2 roller shutter door lines and four new lines on order.
Dallan is without doubt the supplier with which the group has the strongest ties.»
Contact our engineers HERE
Andrea Dallan
CEO – Dallan Spa