Just in Time production: analyzing the cost of warehouse and intermediate warehouses
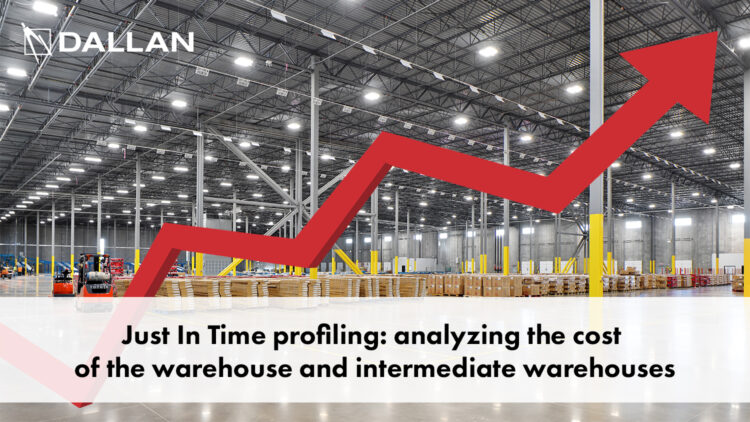
Do you know how much the cost of warehouses weighs in the efficiency of your processes?
Generating efficiency also means taking into account the impact of the warehouse on cash flow.
One of the tools of Lean Production, Just In Time production, involves manufacturing products so that they are ready when they need to be shipped.
This contrasts with production systems in which a facility manufactures products that are then stored in a warehouse, from which products required for shipping are subsequently picked.
Taken from the book “The Revolution of Efficiency”
REQUEST THE BOOK FOR FREE
It’s worth noting that companies have two other types of warehouses: a raw material warehouse and a semi-finished products warehouse.
Every time we take a coil or a sheet of metal, process it and place it in an intermediate warehouse, we add value to it.
Therefore, the value of the warehouse increases as we go from raw material to the finished product (in the final chapters, we’ll also see how to calculate the added value of each operation and how the cost increases in detail).
The problem is that this value doesn’t produce cash flow.
How much would your cash flow improve if you could only manufacture products that were already sold and were able to control production times so that the product would be ready for shipping at the scheduled time?
That’s the Just In Time method in a nutshell: only produce what’s required, when required and keep the cost of the warehouse to a minimum:
- Raw material warehouse;
- Semi-finished product warehouse: the semi-finished products warehouse is also called WIP or Work In Progress;
- Finished product warehouse.
As regards the raw material warehouse, it can be optimized using good planning based on historical data and reordering techniques to avoid out-of-stock issues.
The semi-finished product warehouse is a big problem in companies that use standard punching and bending technologies. In fact, in addition to the value of the warehouse – which increases in line with the number of operations performed on the semi-finished products – it also generates high costs related to the management and handling of pallets and the operations of picking up and depositing pieces.
In coil-fed systems, continuous and in-line processing eliminates all operations involving the picking and depositing of pieces, going from the coil material to the finished product without the need for intermediate warehouses.
This occurs, for example, in the Coil To Window system in which, in the case of rolling shutters and Venetian blinds, a finished rolling shutter or Venetian blind curtain is produced automatically, going directly from the raw material to the finished product.
In Coil To Box and Coil To Pack systems, used respectively in the production of T-bar profiles and drywall profiles, the system goes directly from the coil material to the packaged product and ready for shipment.
Coil-fed punching and laser cutting systems, both simple and combined, also allow the elimination of panel loading and unloading operations, saving time and labor.
They can then be connected to automatic roll former, panel bending and other bending machines in order to go from raw material to finished product as quickly as possible, preferably without the use of intermediate warehouses.
The finished product warehouse often serves as a buffer between market demand and production capacity.
Just In Time production and minimizing the finished product warehouse requires very reliable machines that can process even the smallest production batches.
Therefore, the flexibility of facilities and the ability to change production easily and safely is of fundamental importance.
In the coming pages, we will take a look at the types of solutions that allow these results, for example the parametric punching systems and the Combi tool changing systems: all solutions based on the SMED methodology for reducing equipment changeover time.
Lean production systems: parallel roll forming lines
In some cases, there are products that require multiple roll formed components, which can be produced using the Just in Time philosophy in order to be assembled in the correct order.
Rolling shutters are an example, where an already cut octagonal tube for the rolling shutter is often produced together with the curtain. The tube is paired with the motor and sent to the line where the corresponding rolling shutter curtain is being produced.
Engineer Maurizio Castignoli, of Alias Porte Blindate, explains this concept for the production of metal frames and panels for armored doors.
“I got to know Dallan and roll forming technology in 1995, while working as a production manager at a leading company in the production of armored doors and rolling shutters.
At this company, the metal frame of a door was constructed on a line consisting of a panel bender and a punching machine, numerically controlled.
We, and all the competitors, used to produce the various semi-finished metal products (door frame, sub-frame and door profile) using manual bending machines.
It was then that, for the first time, we thought of producing sub-frames, door frames and profiles using a roll forming machine and cutting and drilling dies at the end of the line, using the same technology with which we produced rolling shutters.
The processing cycle was completely revolutionized and simplified.
From a complex process consisting of sheet metal cutting, sheet metal drilling, sheet metal bending, leg and crossbeam welding and painting, we went to a single processing phase.
Basically, starting from a coil of galvanized and plasticized sheet metal, we were able to produce finished semi-finished parts that were ready to be assembled using metal brackets, thereby eliminating expensive, slow and environmentally unfriendly operations such as welding and painting.
After other work experiences in different sectors, I returned to the world of armored doors at a company where I implemented roll forming technology in the production process of door frames and panel containment profiles: I was finally able to use Dalcos’s now famous coil-fed punching machines.
In 2002, I finally decided to found my own company in the same sector.
This was the context in which I had the idea of also producing the body using a Pxn coil-fed punching machine and a roll forming machine.
I still have magnificent technical and personal memories of my daily discussions with Ingegnere Sergio Dallan regarding the development of an innovative product that could combine all the benefits of lean and in-line production with a booming market.
These are the strengths:
- A profile on every line and “just in time” production: the different profiles that make up a door go immediately to assembly to form the complete door;
- The minimization of intermediate warehouses;
- A Lean Production solution;
- The utmost commercial flexibility for the manufacture of products in non-standard sizes, using Dallan’s parametric programming;
- Advanced industrialization, even in cases of variable sizes and product options that can be chosen for an individual door;
Our competitive advantage over competitors was considerable and allowed us to achieve a turnover of 15 million Euros from scratch in just 4 years!
Today, we almost manage a turnover of 20 million Euros and we produce the second highest number of doors in Italy.
The future? New products and most certainly new production facilities which always focus on technical and production innovation.”
Excerpted from the book “The Revolution of Efficiency,” which you can request for free by clicking HERE
Andrea Dallan
CEO – Dallan Spa