How to choose a sheet metal working machine
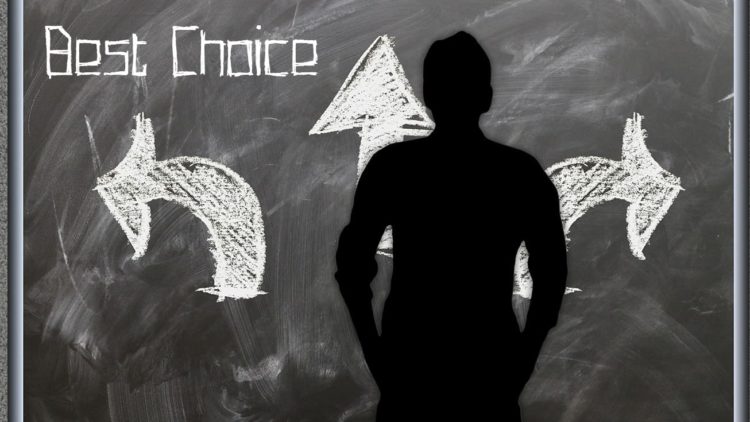
When investing in an automated sheet metal production system, there are several different aspects or criteria that need to be considered, for example productivity, quality of the produced goods, delivery time, and of course, the value of the investment.
When comparing the offers of two or more manufacturers, production managers, purchasing managers and CEOs normally use the gathered information and assess the best choice based on the above criteria and on their experience in the field.
In this article, I suggest a simple method to take into account the different criteria and their overall value in the decision, and calculate a number that will help in the decision on the best purchasing solution.
Main criteria for production systems comparison
The criteria I suggest, in the case of the purchasing of a production system, are the following: feasibility, quality of the produced part, productivity, reliability, efficiency, serviceability, ease of use, flexibility, level of automation, level of safety, and payback time.
Let’s now see the meaning of each criterion.
Feasibility
Is the capacity and the experience of the selected manufacturer in the production of the specific machine.
Normally, in scouting for suppliers, it is normal to find companies that are specialized more in one application field than in the other. It is important to see the products made by the supplier’s machines, in order to understand its experience in the specific industrial sector and product.
Quality of the produced part
This is the quality of parts made by the machine. The quality can be a measure of accuracy, bad parts/good parts ratio and can depend again on the experience of the selected manufacturer in the production of the specific good.
Productivity
Is the productivity of the machine in terms of meters per minute/hour, parts per minute/hour. This figure should take into account also the Efficiency figure that I describe later on.
Sustainability and “Green” technologies
In these years more than ever, sustainability becomes one of the key criterion in the choice of a production technology. It turns out that “green” technologies such as servo electric punch presses have lower power consumption and require less maintenance by eliminating or greatly reducing the use of hydraulic oil. Moreover, new production lines such as coil fed lines ensure the production of the same amount of product with significant savings in raw materials.
All this turns out into smaller operating costs and a lower cost per part – which becomes a huge advantage in order to reduce the payback time, but also in generating extra cash flow in the following years when the amortization of the machine is complete.
Moreover, these technologies have proved to have a greater reliability over the years, and have lower costs for the final disposal of the equipment – due to the absence of oil and hydraulic parts.
Reliability or Availability
This parameter is the evaluation of the reliability of the plant and can be expressed in terms of:
Availability = (Mean Time Between Failures)/(Mean time between Failures – Mean Time to Repair)
This is sometimes not possible for special machines, so it will have to be estimated case by case.
Efficiency
The efficiency of the machine takes into account the time that is required for the machine loading and unloading: for example, a machine can have a very high hits per minute rate, but can take a substantial amount of time in the loading/unloading of the raw material.
Serviceability
This criterion expresses how simple is to have the machine serviced. For example it should evaluate the presence of the teleservice facility, the structure of the service of the supplier, the possibility to service the machine with the internal maintenance personnel.
Ease of use
Different sheet metal manufacturing companies stress on the fact that the machines and systems should be easy to use even with non-specialized personnel. This is extremely important in today’s working environment, where no company can be in the position to be dependent on one machine operator.
Flexibility
The flexibility is the capacity of the machine to be prepared to produce different types of products. In this case, a machine that is more flexible will have also the lower setup time to change from one product to the next. A thought should be given also on how often the production is changed, and if the setup time affects the overall system efficiency as well.
Level of automation
When investing in a production system, the level of automation offered by the different suppliers can be different. For example, one machine could deliver the parts on a roller table, for the operator to pick up, or it could have a robotized stacking/packaging system.
Another way to evaluate the level of automation, is to understand how many operators the machine requires.
When comparing two machines, I suggest to compare machines with similar levels of automation.
Level of safety
Machines have to comply to rigid safety rules. In many cases, it is possible to decide to increase the level of safety in the lines. For example, the coil lines can include coil cars, introduction fingers and features that will make the introduction of the raw material in the machine even simpler.
Payback time
I have left the payback time as the last factor in the list. In fact, I prefer to use the payback time instead of the investment value because it already takes into account the productivity of the machine as we have seen in the previous article (LINK).
Other criteria
Each company can then add other criteria to the list. We will now see how to use all these criteria and weigh them.
Weighing the criteria
Now, it is not necessary to apply the decision-making technique using all of these criteria. Usually the equipment will have some aspects in which they will be similar, and it is not necessary to use these to influence the choice.
I will explain the technique via an example.
Let’s say that we have selected two different machines, and our key criteria are:
- Productivity
- Quality of the produced parts
- Level of automation
- Ease of use
- Payback time
Now, not all of these criteria have the same importance, so we will weigh them with a value from 1 to 10. We apply the value 10 to the most important criterion, then give the value to the other criteria based on the importance that the criterion has to us, compared to the most important.
For us the Productivity is the most important parameter. These are the values we decide to give to the other parameters.
- Productivity: 10
- Quality of the produced parts: 9
- Level of automation: 5
- Ease of use: 6
- Payback time: 8
Now we can build a table such as the following one, using Excel for example:
We now give to the each machine the value 10 when they meet the criteria the best, and a proportional lower value for the other machine.
Now in each column we multiply the evaluation of the machine, with the weight of the criteria.
By summing up the result in the two columns we get a value which represent a sort of weighted average of the evaluation of each machine with all the criteria we chose.
In this case the overall values are similar, but if we have done our considerations well the production manager can use the outcome of this calculation to take a decision or discuss the alternatives with the management.
Note
If we took only the two most important criteria, the Productivity and the Quality of the parts, we would get the value 170 for the first machine and 163 for the second, so we would have a preference on Machine 1 again.
The choice of the most important criteria is the most important part of the process. Once we have decided the first two-three criteria, normally the direction of the choice is already clear.
A weighted final choice
The choice in the investment in a sheet metal production system is not usually taken by one person alone. Depending on the value of the investment, it will require the involvement of the upper management, the production manager and CEO.
In some cases, when scouting for possible suppliers, it turns out that one of them has evidently a better technology or longer experience in the field of application of our interest, and can provide a safe and productive solution.
In other cases, the choice between two or more suppliers can be difficult. The decision making technique proposed in this article can help visualizing the advantages each solution is providing, and makes visible all the steps of the process.