Rollforming Machines: here’s how to ensure the productivity and value of a plant with scheduled maintenance and service contracts
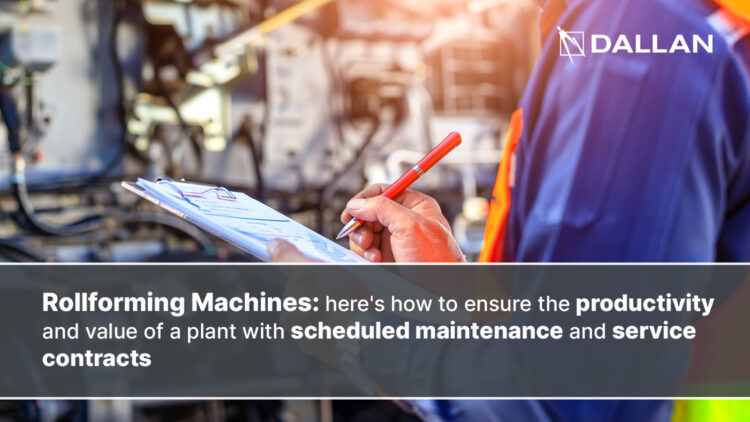
Once the system has been amortized, the hourly cost drops, obviously, but when attributing an hourly cost to a system, I always recommend the continued use of the value calculated initially. There are two reasons for doing so.
The first is conservative: the system has paid for itself, therefore by calculating the cost using the initial value, we always get a higher value that gives us a safety factor when calculating piece cost.
The second reason is related to maintaining the value of the investment.
Taken from the book “The Revolution of Efficiency”
REQUEST THE BOOK FOR FREE
My company has a number of CNC machining systems: lathes, electro-erosion, milling systems and grinders, for the production of accurate tools and dies.
To ensure the reliability of our production systems, we know that we have to continue investing in maintenance and that the maintenance costs of a system, after the first five years, can rise significantly.
In general, when we purchase a new automated system, at Dallan we know that to guarantee the quality of production output and the reliability of the system we need to view investment under several aspects.
Investment in the system
This is clearly the initial investment, which provides us with a reliable machine that produces in compliance with the highest quality standards. Investing in reliable systems that last for decades ensures a great result: that’s particularly the case once the system is amortized and the hourly cost of the investment is eliminated! We’ll see this in the final chapters on how to calculate production cost.
Investment in professional skills of operators
We’ve discussed about the problem regarding the shortage of specialized technical staff and the need to invest in systems that are simple to use. All of that is quite true and it’s not necessary to recruit roll forming, punching or laser cutting specialists.
However, while it’s true that an automatic system requires less labor, it’s also important for line operators, supervisors – or at least department managers – to be motivated and qualified from a managerial point of view.
When it comes to training customer technicians on how to use Dallan Lines, we like to work with technicians who are open-minded, who “want” to get involved and who are “motivated” to continually improve; rather than staff that might be coasting along or content in their ways.
Indeed, the new Industry 4.0-inspired systems include functions and technologies, such as remote assistance and office control, which require curiosity, elasticity and openness.
Investment in raw materials
Nowadays, systems have become very sophisticated. Sometimes, those purchasing raw materials try to optimize and reduce costs by purchasing second choice materials.
That’s not a good solution, as we’ve already seen. Indeed:
Second choice materials require unforeseeable machine adjustment times. Knowing the exact machine start-up times is of FUNDAMENTAL importance;
Above all, there are much more effective ways of reducing the cost of raw materials per piece produced.
Such as, for example, going from sheet-fed to coil-fed processing or going from producing rolling shutters using bars to direct production using coils, which we call COIL TO WINDOW.
This guarantees very high product quality for the end customer and huge purchasing savings, amounting to hundreds of thousands of Euros (or Dollars) per year.
Investment in scheduled maintenance
This is the fourth aspect pertaining to investment. In fact, maintenance is not a cost, but rather an investment. It needs to be scheduled and preventive, to avoid costly emergency machine downtime.
Punching, roll forming and laser machines are designed to last for decades, but it must be borne in mind that certain parts, such as bearings, ball screws, reducers and so on, are subject to wear in proportion to the use of the machine.
After five years, it is important to set aside a budget for preventive maintenance, which usually entails an annual visit by our technicians. During such a visit, our technicians perform checks and give the customer a list of spare parts that we recommend keeping at hand.
These spare parts are available in an emergency or are installed by our technicians during the following year’s visit.
That way, each customer can create a small spare parts warehouse for the system, which guarantees reliability and negligible costs related to any failures.
This is very important!
It’s worth remembering that these costs – for systems that sometimes operate 24 hours a day – should be constant over the years and if that isn’t the case, it should set off alarm bells for an entrepreneur!
Some companies underestimate the importance of preventive maintenance and, in some cases, doing so can prove a very costly mistake.
One of our customer’s companies purchased ten roll forming machines in the 1990s and each of these machines produced – and produces – a component that is used on a production and assembly line.
The machines are always equipped with the same profile, therefore the assembly line uses “Pull” logic, in which the line downstream requires pieces from the machines as and when it needs them.
It’s an excellent production system that has operated flawlessly for almost thirty years.
In recent years, we noticed a reduction in the purchase of spare parts and we received no requests for preventive maintenance. In the meantime, the electronic components of the machines became obsolete, as did the protections and safeties.
When machine stops began to occur, we were contacted for general maintenance work, but considering the abandoned state of the systems and the costs of refurbishing the lines, the cost of the interventions was much higher than what would have been the cost of scheduled annual maintenance.
Fortunately, thanks to our Combi system, it was possible to reuse all the equipment and dies and to renew all the production and safety systems by investing only in new bases and electrical panels for the lines.
What happens at Dallan, to maintain our competitive advantage? We continue to invest in new technologies, lathes and machining centers that are faster, more reliable and automatic. This allows us to produce products with higher quality, less waste and less energy consumption.
We plan to replace our machines when they become over twenty years old, endeavoring to maintain compatibility with the tools that we already have and the devices and services around the machines.
We’ve also noticed that our operators are more motivated when they see an investment in more ergonomic and simple (to use) systems. It’s an important evolution for them and our “steel sculptors”, too!
Below, Sławomir Sofiński, Aluprof’s production and maintenance manager, explains how the correct maintenance of production lines guarantees the value of the investment and the continuity in the production of rolling shutters.
“Our factory was established in 1997. At first, we started production using a roll forming line made in Germany and a bending line from the same manufacturer.
In September 1998, we installed our first Dallan roll forming line, Dallan 1.
The following year, the Dallan 2 dedicated to the production of H77 profiles was installed.
In 2000, Dallan 3 and Dallan 4 joined Aluprof’s Dallan machines.
In 2004, the next two machines were installed, called Dallan 5 and Dallan 6.
Dallan 7 was installed in 2009, followed by Dallan 8 in 2017 and Dallan 9 was installed in 2020.
Therefore, we currently have nine roll forming production lines.
All Dallan lines are produced with components from leading companies, such as SKF, Nidec and Rexroth and every machine incorporates very advanced technologies. We are very happy with how the controls related to the Beckhoff system have evolved.
Over the years, we’ve noticed that each new line always includes improvements, especially the last two machines that were delivered.
With regard to some components, we know we need to keep a few spare parts on site: it’s a known fact that all machines need maintenance.
If you want to keep your machine in good working order, the first thing you need to do is preventive maintenance. For example, at Aluprof there are three types of preventive maintenance: monthly maintenance, where the machine is thoroughly cleaned and checked once a month to make sure there are no air or oil leaks. The punching machine is cleaned and we check that all the mechanical connections are secure. We perform this maintenance outside of production time, usually on a Saturday or a Sunday: we have checklists and this maintenance involves 8 hours of work.
Then we have annual maintenance, which takes place at the beginning of each year before peak season. Every Dallan machine is halted for three days and our technicians check every part of the line separately: the punching machine and hydraulic unit, the sawing machine and threading unit, the roll forming machine and decoiler. Our technicians check the condition of each shaft and cylinder head and replace any worn bearings or components.
Greasing is performed according to the maintenance sheets and we check the recirculating ball screws. The part of the transmission on the first roll forming machines used a chain, so we replace it if needs be or if it has worked loose. Nowadays, machine transmissions only use gears.
Lastly, there’s preventive maintenance. Last year we implemented our internal MES (Manufacturing Execution System). This system generates a huge amount of data and we have identified a set of KPIs for our maintenance department.
The most important KPIs regard the functioning of the lines. We’ve installed extra sensors on the punching machines that control all the hydraulic cylinders and the number of perforations performed on rolling shutters. If one of the four sensors doesn’t record a signal, the entire line stops and a warning light identifies which cylinder has experienced the problem. This prevents the production of non-compliant pieces, whereas before the operator was unable to spot the error and the non-compliant piece was packaged anyway.
The number of punches also tells us when the die should be replaced; when we draw close to the limit of use, a yellow warning sign appears on the MES and our technicians receive an SMS informing them which tool should be replaced.
This helps us carry out the correct maintenance on dies without wearing them out completely, so that we can grind them and use them for a much longer time. We have two sets of dies for each line, so that we can replace them in a few minutes and continue production.
Our MES also calculates how many kilometers of profile have passed through each combi group and soon we’ll also be able to know when certain rollers need to be replaced.
As for electrical and electronic parts, it’s very difficult to predict the service life of these components, but our job is to keep them in the best working order. The optical sensors are cleaned every day. Each electrical panel is checked twice a year using a thermal imaging camera and our technicians check the electrical panel and the connections. Any elements that heat up abnormally are replaced.
We have an excellent relationship with Dallan’s software team, which also manages to repair or reprogram the PLC module remotely via teleservice. We need to pay particular attention to old machines, because certain electronic components are going out of production and we need to work preventively with Dallan technicians.
During peak season, when there’s a problem there need to be rapid intervention systems: Special Forces don’t only exist in the army!
Some automation groups inside the machines are made up of many small parts and we have procured complete sets that we keep in stock. That way, we can replace a recirculating screw or a quick connection in a matter of minutes, for example. Many parts are compatible with all types of lines and we keep a stock of these parts in our warehouse.
Regular cleaning of machines is very important and we have operators coming in every weekend to keep the lines perfectly clean. I’ve prepared a list of items that they need to clean more carefully, so I don’t need a specialist for this job. Cleaning is very important because some parts accumulate dust, such as fans and heat exchangers, and cleaning maintains the efficiency and value of our systems.”
Sławomir Sofiński
Taken from the book “The Revolution of Efficiency”
REQUEST THE BOOK FOR FREE
Andrea Dallan
CEO – Dallan Spa