Cash flow of a Coil to Window System
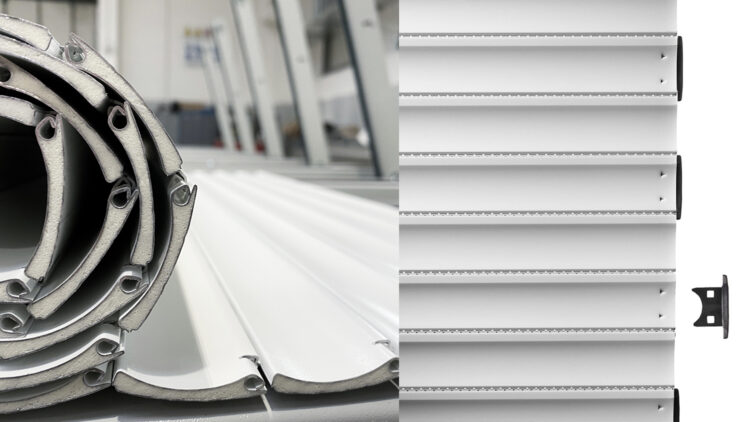
In this section, I’d like to explain how coil to window systems can generate savings of over 200,000 Euros per year for manufacturers of finished rolling shutter curtains, which are the main factors that generate these very high savings and also why this production system is much more sustainable and environmentally friendly than traditional systems.
Production of aluminum rolling shutters: increasing profits and sustainability using Coil To Window systems.
Aluminum foam-filled rolling shutters are increasingly popular in Europe and abroad thanks to their many advantages:
- energy saving (heating and cooling costs of buildings decrease enormously)
- privacy
- safety and protection of windows and fixtures
- simple automation and domotics (implementing smart functions like you would have on your home technology)
- high quality and weather resistant
The standard production cycle for rolling shutters began with pre-formed profile bars, between 5.6 and 7 meters in length, which were cut to size and assembled, generating a percentage of waste varying between 5 and 12%.
Modern Coil To Window systems, on the other hand, produce directly from continuous coils and produce complete rolling shutter curtains, cut to size; the percentage of waste is next to nothing.
The traditional method: production using pre-formed bars
The most common system for the production of rolling shutter curtains begins with bundles of pre-formed profiles. They’re cut to size and assembled or fed into a machine that picks up one piece at a time, cuts it to size and assembles it.
The bars are cut to size and, depending on the width of the window, a piece is left unusable and is discarded.
The table below shows the percentages of waste for bars that are 5.6m in length by various curtain widths.
Rolling shutter manufacturers have tried lots of systems to try to optimize this waste, but every solution proved to be very expensive in terms of the time required and required the support of an operator.
In general, the percentage of waste assumed is between 5 and 12%.
The Coil-to-window Production System for rolling shutters
In the three minutes it takes to read this part, a Dallan COIL TO WINDOW system produces a finished rolling shutter curtain directly from a coil, practically without waste and even without the assistance of expert operators
Coil To Window production systems produce finished and assembled rolling shutter curtains directly from coils.
To do so, they only require a single operator and there are no complex operations to handle the packs of profiles, which sometimes suffer damage during said operations.
Production data for each curtain, such as width, height and quantity can be loaded directly from the office or via Excel tables.
This is also classed as parametric production and there’s no need to calculate line programming times!
The automatic line includes:
- Decoiler that contains the raw material (usually pre-painted aluminum)
- T4 precision roll former
- Quick changeover COMBI system which contains the rollers for a rolling shutter model
- Foam machine that mixes the foam components (usually polyol and isocyanate)
- Set of foam maturing benches
- Flying saw that cuts the pieces to size
- Punching machine that drills the ventilation holes (aligned, if required)
- Threading bench
- Locking system with plastic caps or mechanical locking without caps (patented by Dallan)
This line requires the presence of only one operator during production, for quality control and removing the finished curtain.
25,000 windows require between 2 and 2.5 million linear meters of profile per year, depending on the size of the windows and profiles. We then analyze the savings generated by a Coil To Window system based on these volumes.
Material savings generated by a Coil To Window system for various profile sizes
The following table shows the quantity of aluminum and polyurethane for various aluminum and polyurethane profiles of various sizes for bars that are 1 meter in length.
The cost of aluminum and polyurethane varies and can be requested from the producers of these raw materials.
The rolling shutter profiles were selected from among the most significant ones of the more than 300 rolling shutter profiles in Dallan’s catalog. The offering of profiles for aluminum rolling shutters has been segmented to cover both high-quality profiles and low-cost products (called “ECO” profiles).
Eco profiles are usually not as wide (coil width) and have inferior thicknesses. Aluminum, as shown in the table, accounts for 86 to 92% of the cost of raw material.
The production of 2.5 million meters of rolling shutters results in the raw material costs below. The table also shows the savings generated solely by reducing the purchase cost of aluminum and polyurethane, with a reduction in the purchase of raw materials of 5% and 12% respectively.
An important note: the volumes and savings shown are obtained by calculating solely the cost of the aluminum and polyurethane saved. In the case of profile bars that are purchased, savings increase by two or three times because suppliers add their mark-ups to the cost of the raw material in order to cover:
- processing costs
- energy costs
- workforce costs
- shipping costs
- quota of fixed costs
- profit
The weight of the polyurethane was calculated on the basis of low-density polyurethane foam and the costs of aluminum and polyurethane refer to values as of October 2016.
The annual production of a Coil To Window system that processes up to 37 meters per minute and operates 220 days a year ranges from 2 to 2.5 million meters per shift. The figure can vary depending on the size of the profile, the average size of the windows produced and the number of color changes required. The data is also confirmed by the experience of the Stella group (see their account at the beginning of the book).
When working two or three shifts, savings per line are also multiplied by two or three and there are also Coil To Window production systems with higher speeds, up to 60 and 80 meters per minute.
The waste that would be generated when processing 2.5 million meters of fixed-length bars equates to approximately 300,000 linear meters of aluminum and polyurethane profiles, which equates to 30.8 tons of aluminum and 2.7 tons of polyurethane foam respectively, joined together in the production process.
These materials are still difficult to recycle and their disposal is a cost for the company. By reducing processing waste, Coil To Window systems reduce the environmental impact of production, and at the same time, ensure elevated annual profits for rolling shutter curtain manufacturers.
Analyzed from a LEAN perspective, Coil to Window technology shows you how it can offer the maximum benefits sought from lean production:
- Reduction and elimination of waste
- Minimization of Work-In-Progress (WIP) – no semi-finished warehouses
- Product size changes on the fly – curtains of different sizes can be produced without halting the machine
- No need to program the machine – the line reads production orders directly from the customer’s ERP system
- Reduction of labor to a minimum – the production of 2.5 million meters of rolling shutters usually requires at least 4 people, whereas a single operator, even without specific expertise, is sufficient for a Coil To Window line
In the search for efficiency, the most innovative technologies introduce new paradigms, increase productivity, efficiency and sustainability, introduce widespread automation which reduces the amount of labor normally required to produce the same number of window curtains to less than a quarter.
Coil To Window technology is a great opportunity that you can use to introduce:
- very high levels of automation
- a lean and continuous process
- zero programming
- in-line quality control that can also be automated
- integration into corporate ERP systems
In this chapter, we focused on how the most advanced Coil To Window technology introduces savings of 5 to 12% on raw materials and, in particular, how it results in higher quality products with less raw material and less or zero waste.
This makes the production of rolling shutters even more profitable, more sustainable and ecological.
Click on the link below to see a Coil To Window system in operation, in this case with the fitting of plastic caps:
If you also want to find out more about the Coil to Window System, but not only, subscribe to our Live Masterclass: every week I will deepen a topic related to our machines and our production systems focused on Lean Production.
To request access, click on the link and fill out the form!
SIGN UP TO THE MASTERCLASS
Andrea Dallan
CEO – Dallan Spa