Flexibility in sheet metal forming lines: the Combi system for stamping
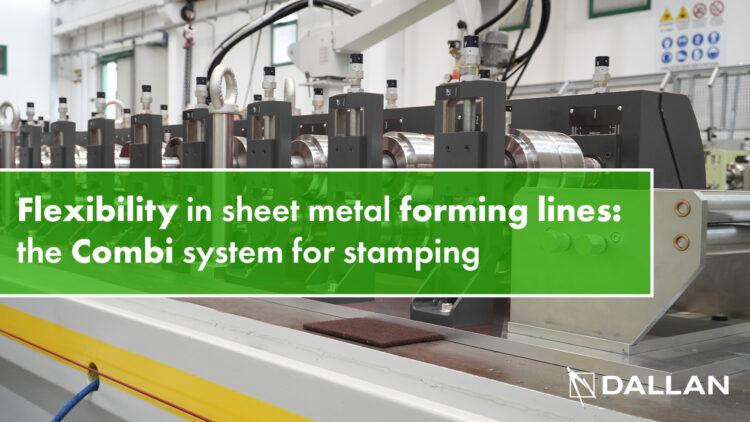
Once we learned the advantages of the Combi system for the sets of rollers, we also applied the same concept to the groups of dies installed before or after the roll forming machines.
When a profile has been formed, sometimes hydraulic units and special dies for deep drawing or special openings (those that cannot be performed before profiling) are required to complete processing.
That’s the reason for electro-hydraulic Combi groups: steel plates on which the following are mounted:
- Hydraulic units
- Dies
- Lubrication systems
- Motorized discharge systems
- Pneumatic units
- Accessory insertion systems
Taken from the book “The Revolution of Efficiency”
REQUEST THE BOOK FOR FREE
All the above, are specific to a certain type of profile. The following are also fitted on the Combi plate:
- Hydraulic connections with quick coupling
- Pneumatic connections with quick coupling
- Electrical connections with quick coupling connectors
When a change of profile is required, the Combi plate is disconnected, lifted using a bridge crane and placed on one side.
Then, it is replaced by the plate that includes all the dies installed and already adjusted for the next profile, saving hours of work on the installation of the dies, adjustments, and tests.
The plate has special centering points for fast positioning in this case, too.
Therefore:
- Several electro-hydraulic Combi groups can be set up away from the machine while it is operating
- You can have multiple machines that use the same Combis to increase productivity and reliability and reduce the need for product changes to the point of eliminating them
- Combis allow lines to be modernized when systems reach twenty years of age
The SMED philosophy, which is an instrument of Lean Production, is the goal of perfection towards which you can strive, even over time, adding Combi groups and equipment in order to increasingly simplify and speed-up tool changeovers – as long as the machine has been conceived and designed with this in mind.
Below is an account of how Roto Okna, part of the German Roto group, a manufacturer of roof windows, resolved the issue of flexibility. According to Arkadiusz Guz, production manager:
“In 2013, our Company manufactured about 11,000 aluminum window elements per day (working on 2 shifts).
Our production process was very complex and time consuming. It consisted of the following tasks:
- A detail was cut longitudinally from a coil of material (operation control)
- The detail was deposited on a rack
- Details were collected from the rack and delivered to the bending brake workstation
- Details were processed on the bending brake (operation control)
- Details were transported from the bending brake to the mechanical eccentric press
- Details were processed on the mechanical eccentric brake (operation control)
This process was very cost-inefficient and required 3 highly qualified operators (per shift)
The objective set by the Managing Board in 2014 was ambitious:
find and implement a process that will allow us to reduce the number of operations from 3 to 1 without extending the time required for machine changeover.
We contacted Dallan and put our requirements to them.
It turned out that Dallan already had such a solution in their portfolio.
It was a Combi-type roll-forming line that consisted of the following:
- Decoiler
- Straightener
- Punching press
- Roll forming set of rollers
- Detail receiving table
An important benefit of this line is represented by the system which ensures the quick changeover of roll forming rollers mounted on a single plate. In our case, the time required is 20 minutes (2 operators).
The solution put forward by Dallan allowed us to reduce the number of operators involved in the process from 3 to 1, while maintaining the changeover time at 20 minutes.
There’s another positive aspect of this solution, namely the opportunity to automate the detail reception and collection process. That’s our next step in the process of continuous improvement of our organization.”
Arkadiusz Guz
Taken from the book “The Revolution of Efficiency”
REQUEST THE BOOK FOR FREE
Andrea Dallan
CEO – Dallan Spa