Is Rollforming really that complicated?
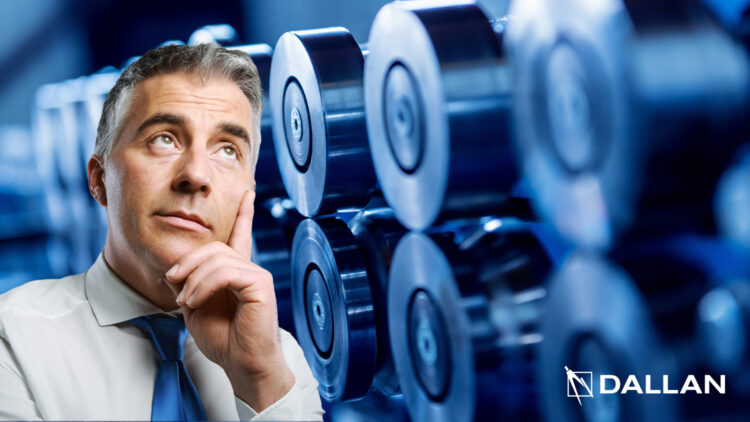
Before founding Dallan, my father worked in a company that produced metal door and window fittings called Secco.
Secco was a leading company in the roll forming of door and window frames and the company produced technicians and businessmen of the caliber of Massimo Colomban (Permasteelisa) and of course, Sergio Dallan š
My father always tells me that, back in the days, roll forming was a profession for artists, in which roll forming āmagiciansā knew which rollers and sections to touch to ensure profiles turned out well. Pieces of wood and temporary fixes were often used to obtain the right profile.
A process that was anything but industrial, despite the size and the company!
Taken from the book “The Revolution of Efficiency”
REQUEST THE BOOK FOR FREE
He studied at university while working and had almost finished his graduation thesis on water jets, when he decided to change the subject of the thesis completely. He proceeded to write a thesis on roll forming light profiles – a milestone in the history of our company.
Thin materials were already the focus of my fatherās attentions way back in 1973.
He gathered all the studies available at the time and was quick to complete the new thesis, developing an iterative algorithm for calculating the steps required for bending, which subsequently, developed into the proprietary software that we still use today.
Processing thin sheet metal requires different parameters compared to those for thick materials, for example:
- Calculating large bend radii is much more complex
- Small differences in the characteristics of materials modify spring-back
Moreover, even in modern simulation software, thin sheet metal is more complex as it requires much smaller meshes (partitions). This greatly increases the complexity and length of the calculation.
The algorithm that my father developed and perfected, immediately produced excellent results on thin profiles. He also developed software using a programming language called Fortran IV and went to the CED data center in Milan to get the first āflowersā calculated.
The first plotters came out in the years that followed and we still have the first flower designed by my fatherās software at the company.
When he graduated, he tried to introduce the new tool into the company, a tool which removed a lot of the āmagicā and partially reduced the role of āexpertā technicians.
Itās easy to understand why this innovation was not well received and encountered resistance.
He wanted to be able to apply his idea to design work and thatās why, he would say, ābeing a bit pretentious and recklessā, this is one of the reasons he left the company at the age of 33 and used his and my motherās money to found Dallan.
The Ingegnere and the simplicity of roll forming
When my father started out on his own, he didnāt have a company behind him, nor a history of experience he could use to give him an advantage over other competitors.
What he had at the time were his academic qualifications. He founded the company under the name āDallan Ing. Sergioā, which he kept for the first few years.
The first people who joined the company would always call him Ingegnere and, after forty years together, they continue to do so.
Even Fabrizio, who was the first technician he hired in 1978, and who also continues to refer to him as āLeiā, an Italian form to express courtesy, when speaking to him.
My father is also still called Ingegnere by many of our customers: this has always fascinated me and, as I told you at the beginning of this book, also influenced my choice of studies.
The clash with roll forming specialists was one of the reasons my father decided that, as well as specializing in thin profiles, Dallan machines should be simple to adjust and use, even by non-expert personnel.
Consequently, over time he began to introduce a number of innovations to introduce fixed reference points in the roll forming process that allowed technicians to mount rollers in a way that would strictly comply with the parameters of the process. Then he introduced the fixed height lower shaft and an alignment system for all the rollers in a set, using purposely machined alignment rings at the base of each shaft.
Basic versions of these two measures were also used in the first models of tool-heads and were continuously improved.
Furthermore, in the following years he also introduced:
- The Vernier system – a graded scale that allowed the operator to restore the factory settings of a set of rollers at any time
- The design of rollers with calibrated shoulders – a system that allows the adjustment of a set for different thicknesses by using a thickness gauge on the two external sides of the set
- Alaser measuring system for the calibration of alignment spacers
Above all, he introduced the Combi system, which makes production changeovers very quick thanks to the tool-head assembled together with the introducer and the straightener on an aluminum plate. This provided and, as weāve already seen, continues to provide extreme flexibility and, above all, assures the operator that all the rollers are already assembled on the machine, with calibration being the only thing left to do once the first material has been introduced.
The quality of pre-painted, thin sheet metal profiles
As already mentioned, after 1984 my father decided to focus exclusively on thin sheet metal.
Sheet metal less than two millimeters in thickness represented a large part of the market, but it was difficult to say no to potential customers when there wasnāt much work around at the beginning!
In any case, after the first slat machine was sold at the Saie fair, Dallan began to make a name for itself as a specialist in the suspended ceiling sector.
The sector uses a lot of pre-painted and pre-finished sheet metal and aluminum coils and the profiles have an aesthetic function, often without protective film.
These materials are even more difficult to process than profiles made from bare coils or galvanized sheet metal, for two reasons:
- Rollers have different peripheral speeds depending on the distance from the axis of the shaft, and thatās why the speed at the points of contact with pre-painted material is different to the speed of the profileās neutral axis. Consequently, thereās some sliding and the risk of scratching the surface of the profile
- Furthermore, every type of paint has a different elasticity: on smaller bending radii, the external paint lengthens with respect to the neutral axis of fold. If the bending radius is too small and the paint is too inelastic, the coating starts to crack and the underlying material becomes visible. This must be avoided at all costs.
The first problem is resolved by designing the set of rollers, considering the position of the neutral axis and leaving the appropriate space in critical areas. In addition, the paint must be suitable for the roll forming process and be resistant to scratches and abrasions according to the test methods described, for example, in the EN 13523-12 and EN 13523-16 standards.
The second problem is resolved by the design of the profile: the smaller bending radii need to observe the coatingās elasticity characteristics, as defined in the EN 1396 standard.
The test qualifies coatings as T0, T0.5, T1 according to whether the paint tolerates bending radii equal to zero times the thickness (bend-press), 0.5 times the thickness, or equal to the thickness.
There are also T1.5 or T2 type materials where paint has very low elasticity and the internal bending radii must be kept at more than twice the thickness.
On thin sheet metal, we normally use organic coatings with a capacity of between T0.5 and T1. Hence, in the profile design phase, we always prefer to adopt internal radii that are 0.8 times greater than the material thickness.
Thanks to the great work carried out over many years in the slat and pre-painted profile sector, my father and I recently decided to change the companyās quoted Mission Statement from āSolutions and Systems for sheet metal processingā to āSolutions and Systems for thin sheet metal and aesthetic profilesā.
Thin sheet metal requires different measures compared to medium thickness sheet metal and often presents greater difficulties.
Thatās why we call our machines Precision Roll Forming machines.
Taken from the book “The Revolution of Efficiency”
REQUEST THE BOOK FOR FREE
Andrea Dallan
CEO ā Dallan Spa