Rollforming machines: it is easier to win a lottery than to find a specialized technician
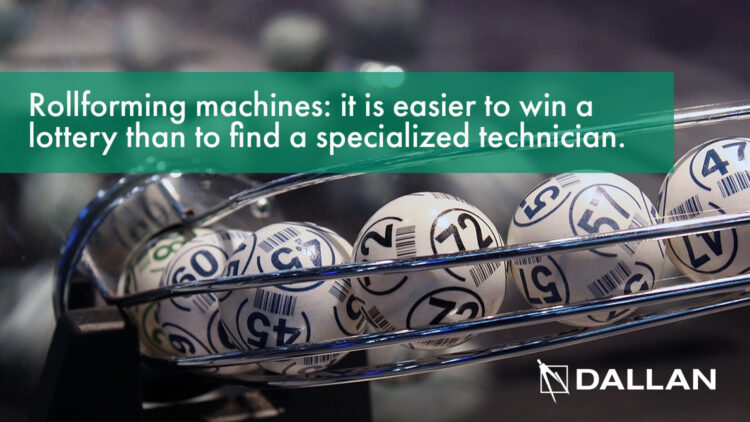
Difficulties finding productive staff is becoming an increasingly widespread problem, especially in Europe and North America.
This is in addition to wanting to keep production costs as low as possible by replacing personnel who perform simple or repetitive tasks with automations. The dream of entrepreneurs and companies is to produce efficiently using little to no personnel.
So, I was faced with these two needs.
On the one hand, I saw the willingness of companies to purchase highly automated lines, which would start with raw materials and, where possible, work their way right through to packaged and ready to ship products using the minimum number of personnel. This was a driving force towards lines with high levels of sophistication.
Taken from the book “The Revolution of Efficiency”
REQUEST THE BOOK FOR FREE
On the other hand, there was a need for lines that were extremely simple to use. Indeed, it was becoming increasingly difficult to find qualified personnel and companies did not want to be dependent on hyper-specialized technicians, who were the only ones who knew the “secrets” of the lines they operated.
Automations and machines had to be simple to use, even by unskilled personnel.
In the previous chapter, we saw how Coil To Pack automations have greatly contributed to increasing the productivity of lines for plasterboard profiles.
I found the same to be true in relation to lines for suspended ceiling T-bar profiles. This was another of the company’s major areas of specialization. The T-bar is an inverted T-profile, consisting of a body made of galvanized sheet metal and a cover made of pre-painted sheet metal or aluminum.
A German customer wanted to activate a series of ultra-high capacity production lines in order to produce these profiles and the aim of the project was that said lines had to double the production of the machines previously available on the market, while using a quarter of the personnel.
The analysis showed that, along with the production of profiles, it was also necessary to focus on the product’s quality control and packaging sequences. A lot of aspects of the line had to be considered: size and length of the coils, production speed, speed with which materials on the line were used, quality of the raw materials, type of packaging required, an ergonomic assessment of the weight of the packs of profiles and the connection to a vision system for quality controls on the profiles.
The result was the first fully integrated Coil To Box lines – from the coil to the boxed finished profile, already positioned on the pallet for strapping and shipping.
These systems produced these highly technical and complex aesthetic profiles at speeds of over 100 meters per minute.
To do all of this, they only needed three operators for every two lines, mainly to ensure the supply of raw material to the machines, which – literally – devoured tons and tons of galvanized, pre-painted sheet metal, high-strength steel for clips, cardboard for packaging and glue so that pallets have perfectly arranged cardboard boxes stacked on top of each other by the time they reach the end of the line.
Coil To Window systems, which we’ve already discussed in the section on Profalux and the Stella group, are also an excellent way of introducing automation into the production of rolling shutter blinds. In this case, although still automation, it’s not about packing, but packaging.
Coil To Window systems also exist for another branch of sun protection products: external Venetian blinds.
Up to a few years ago, these products were typical of the Swiss, Austrian and German markets. Demand today has spread to all of Eastern Europe, France and they’re also starting to arrive in Italy. Compared to rolling shutters, external Venetian blinds have the advantage of being able to regulate the amount of light in a room by varying the inclination of the slats.
In this case, as in the case of rolling shutters, every window is different, therefore any curtain produced can be different from the next. The ability to manage production without having to manually program the machines is absolutely essential.
There are two main types of Venetian blind systems, C and Z. Compared to rolling shutters, the assembly systems of these curtains are more complex, requiring the use of pins and hooks on the ends of the profiles and the assembly onto fabric brackets of different shapes.
Up to 2005, roll forming machines only produced profiles which were then assembled manually on special frames. Assembly always took the longest time, not the production of the profiles, which could reach sixty meters per minute.
Dallan had always operated on the thin, pre-painted sheet metal profile market, so it was something we were specialized in. Our customers began to ask for systems to carry out the assembly of these profiles on brackets. We began studying and building the first hook systems and the first threading systems, which we ended up patenting.
Indeed, the amount of work required to manually assemble these profiles is so great that automations end up paying for themselves in no time at all.
Dallan Venetian blind systems were designed using the same logic as the rolling shutter system. Several work and assembly stations separated by conveyors that act as buffers to balance the processing time of all the stations. Over time, we worked on balancing the speeds of the different machines to avoid creating bottlenecks in the process and managed to achieve the current extraordinary solutions.
The result? A system like the one for C Venetian blinds that can be seen in the video below:
The first part of the line produces profiles complete with holes. The machined and cut profile is delivered to a set of conveyors and taken to the machine that adds the end pins. Then, via a second set of conveyors, the profiles are sent to the last assembly station, where they are inserted into the ladder string one by one.
The assembled curtain is picked up by an operator or automatically and usually put onto special trolleys that are then sent to final assembly stations.
At these stations, the curtain is opened, checked and the final accessories are added: an extruded profile at the base, which gives the curtain the right weight and tension, then lift tapes are added and the motor is inserted into the C profile.
These solutions allow profiles to be made and assembled while reducing manual work and intermediate warehouses to a minimum, as well as allowing the profile and the color of the tape to be changed very quickly.
An entirely similar system also exists for Z profiles, the assembly of which is even more complex. In fact, lateral hooks are installed on these profiles which close on special loop tapes: this case also involved coming up with a system of independent work stations that would allow us to simplify assembly and get from coil to packaged curtain ready for final assembly very quickly.
These automations reduced the personnel needed for traditional processing to less than a third, introducing other significant benefits, such as a reduction of work in progress and the introduction of centralized production management systems, with parametric programming which allows order information to be loaded directly from the company’s ERP system.
The figure below, shows how the software integrated in the machine also allows the operator to check the shape of the curtain before launching the production order on the machine.
The management software of these lines is one of the company’s fundamental assets. The latest systems allow you to check the orders in production, send Job Lists and receive automatic feedback on already completed production, as well as manage the production of any extra slats required for repairs, should problems occur during the manual assembly operations downstream.
The 2013 merger also saw the incorporation of Elda, the company that had specialized in the production of electrical panels and software for Dallan lines, into Dallan. Having the team of software engineers who develop the management software within the company has allowed us to respond promptly to market requests, developing software that offers much more overall than that which customers normally expect.
Nowadays, the team of internal software engineers is without doubt a fundamental asset in the transfer of enormous value to our customers, automating important parts of the corporate information flow.
Indeed, as we have already seen, from a LEAN point of view it’s not sufficient to merely eliminate material waste, it’s also necessary to eliminate information flows and hard-copy processes that don’t produce added value for the customer!
The flexibility of a software development team makes it possible to come up with solutions such as the one in the figure below:
In this case, the flow of information is optimized, and while leaving a margin for the production manager and the operator to intervene, we eliminated the entire process of hard-copy orders and manual information input, together with the errors that it was capable of generating.
Taken from the book “The Revolution of Efficiency”
REQUEST THE BOOK FOR FREE
Andrea Dallan
CEO – Dallan Spa