How much does downtime really cost your company?
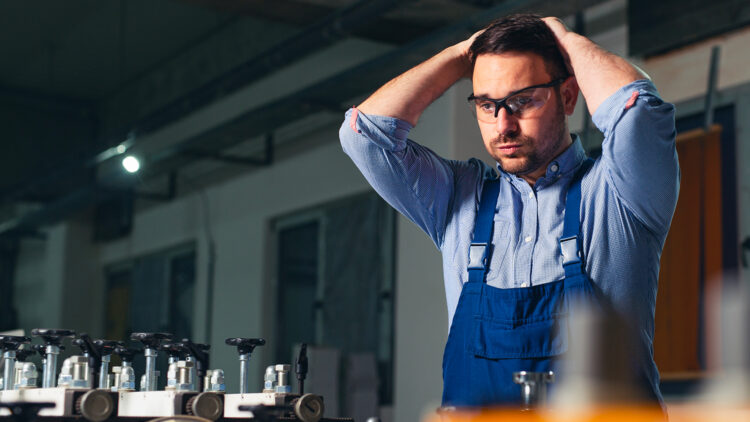
We are talking about the reliability of production systems. We are often too busy or preoccupied working on orders and urgencies, forgetting that systems are the basis of our productivity.
It’s obvious, machines stop when we use them or we need them!
Many of our customers own systems that have been operating for over twenty or even thirty years, and we all know that a system that works properly has mechanical components that wear out.
On “older” systems, this is compounded by the fact that many electrical and electronic components are no longer available, and in case of failure, are difficult if not impossible to source.
Thanks to an obsessive attention to the quality of components and assembly, our company has begun to offer an extended 10-year warranty on some key components, such as roll forming toolheads. The fact is, that even a system built according to exacting standards requires maintenance which can be performed in two ways.
The first is the most common and also the most inefficient: simply repairing a fault when it occurs.
Do we know how much downtime costs in this case?
Of course we do. There’s the cost of the service engineer, who has to be called out for an urgent visit. Also spare parts may need to be purchased, which need to be ordered and delivered.
Again, it is quite possible, as in the case of electronic components for old machines, that the faulty component is no longer available on the market, and in this case, the manufacturer will need time to procure a compatible replacement.
Look at the graph above. From the moment the fault occurs, the system begins to reduce its productivity until, in the case in the figure, it stops. Machine downtime depends on many factors: type of problem, availability of spare parts, and skills of the engineers. In more difficult cases, it can be a matter of days or even weeks.
So, how much does machine downtime cost you due to lost productivity?
Not only that, when the system finally resumes production, normal levels of production are achieved gradually. Usually not because of the system itself, but because of what happened around the system.This causes orders to pile up, dissatisfied customers calling, and a saturated and stressed production program, as well as, tension involving the production departments.
If we then add the hours spent by operators, foremen, managers, and salespersons to manage customers, it’s estimated that the value of a single week’s loss of production is seven to ten times the cost of the repair itself.
(Internal cost of machine downtime) = (Value of lost production) + (hours spent by internal staff on repair and management) = (OEE x productivity x sales value) + (hours spent by internal staff on repair and management)
If plant maintenance is not performed on a regular basis, this is the result: expensive repairs, frustration, and anger. Not to mention customer dissatisfaction, which as we know, can cost a lot more!
The second way to manage maintenance is much more interesting: we’re talking about preventive maintenance programs (PMPs)
Preventive maintenance consists of organizing inspection visits on the system, which are scheduled for periods of lower productivity or when the line does not need to operate. Since these inspections are on systems that are in operation, these visits are usually quick and effective.
The service engineer can analyze the system from a mechanical, electrical, electronic and safety point of view, and check if there are any anomalies or components that need to be replaced. This phase is called Assessment (i.e. the assessment of the state of the system).
Once the evaluation has been completed and the most immediate repairs have been carried out, a work plan is drawn up which usually includes the offer of original spare parts, which we recommend keeping in stock (a classic example is ball screws, which you should preferably keep in stock so that you can replace them, if necessary, without having to wait for them to be sourced).
Based on the type and number of systems, a work plan will include monthly checks, which are carried out by your company’s internal staff, and visits at regular intervals (usually every year or every two years).
During these visits, in addition to the checks and adjustments on the machine, some of the spare parts stocked in the warehouse are installed and a new list of recommended spare parts is drawn up so that you always remain fully operational.
What are the benefits of this maintenance method?
Clear-cut: you work preventively, thereby avoiding machines coming to a complete stop. Any faults are identified in advance, in the phase of decreasing performance! In addition, obsolete components are procured and adapted in advance.
Furthermore, the repair can be scheduled during specific periods, without needing to change the processing program!
Good preventive maintenance work is insurance against downtime and that is exactly what we offer with our customized Dallan PMP Preventive Maintenance programs.
This service is customized and tailored to the type and number of your Dallan systems. Companies with five, ten, and more than fifteen systems necessarily require different execution times, engineers, and components.
This kind of approach means you can always count on your systems to produce profiles of the highest quality, which will distinguish your company for literally decades.
Contact our specialists at [email protected] to find out more about all the packages in our service!
Andrea Dallan
CEO – Dallan Spa