ONE-PIECE-FLOW production of metal profiles: can machine programming time be completely eliminated?
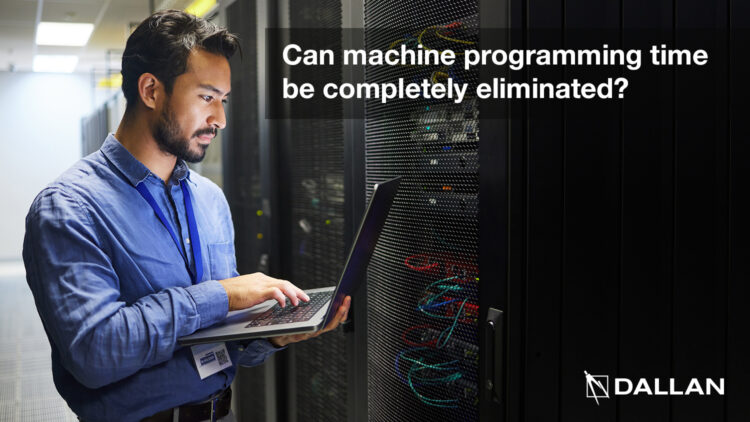
The programming time of a machine and the time to send and enter work orders is time that costs the company a lot.
First of all, programming a machine tool, a punching machine or a laser requires a technician with process and product skills; that represents a cost for the company.
Secondly, every programming operation is subject to errors, which in turn generate expensive production waste and incorrect production.
Clearly, in some cases, the cost of programming cannot be eliminated – this might apply to companies making one-off pieces.
Taken from the book “The Revolution of Efficiency”
REQUEST THE BOOK FOR FREE
However, parametric programming can quite often resolve all these issues.
The Pareto principle that I described at the beginning of the book comes in handy here. When we look at production, products are often grouped into families and these families have common traits, such as the width of the coil, certain groupings of processes, notches and so on.
In general, only one drawing of the products in a family can be created in which the dimensions are defined by parameters and the various types of processing are correlated by mathematical rules.
Below are a few examples of parametric products:
- Door and window panels
- Door and window frames
- Frames and structures for air machines
- Air dampers and fire dampers
- Shelving and shelves
- Rolling shutter curtains
- Venetian blinds
- Structures for industrial constructions (C, Z and Sigma profiles)
- Structures and paneling for elevators and much more
When we work on one of these markets, there is a tremendous opportunity to completely eliminate programming time, as well as the risk of entering incorrect order information.
Indeed, when production and products are defined by rules, systems such as parametric punching allow data transfer and programs to be generated directly from orders loaded into the company’s ERP system – provided said orders include the information required to define:
- Product family
- Parameters
- Quantity to be produced
Many roll forming companies have parametric products. In fact, when working from coils, profiles often have the same width, but can have variable lengths and be machined differently.
Parametric punching machines and roll forming systems make it possible to produce a “batch of one”, meaning mass production of products that are all different from one another, customized for each customer.
This is the philosophy that Giovanni Maffei named “Zero Standard”.
The line operator already finds all the programs and the JobList loaded onto the machine.
Consequently, the operator only needs to check the machine’s equipment – i.e. that the correct tools and Combi groups are on board – and mount the correct coil for the processing required.
The operator doesn’t have to perform any data entry, which can lead to production errors, but only has to check the equipment, perform quality controls, load the raw material and unload the finished products.
The result can be seen in the video below, which shows a production system of filter frames, using a parametric punching machine and duplex roll forming machine for profiles of various widths:
Taken from the book “The Revolution of Efficiency”
REQUEST THE BOOK FOR FREE
Andrea Dallan
CEO – Dallan Spa