Coil fed laser and punching: how to generate 197.400 Euro in profits per year
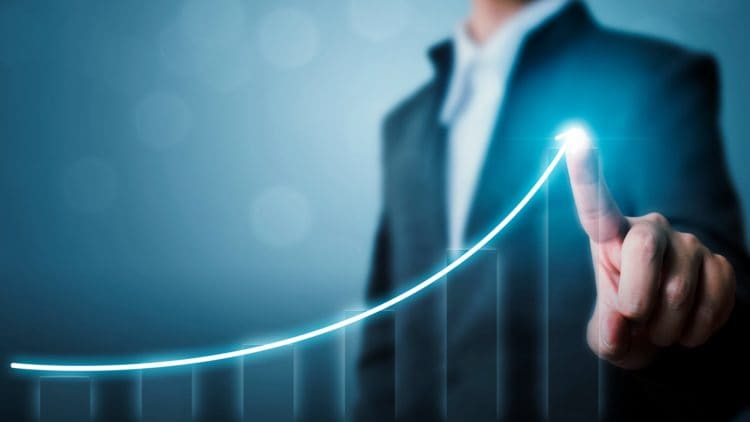
New and innovative technologies can increase the competitiveness and profits for OEMs and sheet metal fabricators. In my previous article, I showed how the material savings can reach as much as 15,9% when moving to modern coil fed punching and laser cutting lines.
The second great advantage of coil fed lines is the higher production speed. In particular, today’s punching and fiber laser cutting machines are combined in production lines that execute the punching and laser cutting operation simultaneously. In many cases the cycle time is reduced by more than 50% compared to traditional punch/laser lines, where the parts are first punched, and then laser cut.
As promised, this article completes the case history of company Elleci: I will show how the company is taking advantage of the high production speed of its coil fed punch/laser line, generating additional 102.200 Euro in savings per year which when added to the saving in raw material, totals 197.400 Euros.
Find out more information on coil fed punching and simultaneous laser cutting lines.
Coil fed punching and simultaneous laser cutting: structure of the line
Here is the layout of a typical coil fed punching and laser cutting line. The line is divided in three main modules: decoiler, punching unit and laser cutting unit.
The punching unit and the laser cutting unit work independently.
First, the punching machine processes the punching and embossing operations on the coil and then shears the punched blank.
Then, the product is delivered to the laser cutting unit through the roller bench; the laser unit uses a vision system to identify the position of the panel and to set the laser cutting operation to the pre-cut holes.
The high speed of the process is due to:
- The continuous process from coil eliminates the loading and unloading time (present in all traditional sheet fed machines)
- Laser cutting and punching operation take place simultaneously and in parallel
This short documentary explains in detail the operation of coil fed punch and laser cutting lines.
Cycle time: comparison table between coil fed and traditional process
The following data is courtesy of Elleci company, taken from the payback calculation for the investment in a coil fed punch/laser line.
On the third column, there is the actual process time in minutes per part with traditional punch/laser from sheet. In the fifth column, the time in coil fed punch/laser line.
The production time on a sheet fed machine requires two full shifts (almost 4000 hours), wheras the coil fed process requires less than one shift operation on the same quantities.
2266 hours are saved by the coil fed production process, and Elleci calculated conservatively a saving of 51100 Euro (based only on Manpower and electricity).
To cover the total production, the coil fed machine will work on two shifts and this gets their total saving on machine working hours to 102.200,- Euro.
Three important notes:
- The cycle time is calculated including loading and unloading of the sheet (it’s the total production time)
- 51000 Euro is a very conservative calculation: in fact the 22 Euro per hour include just electricity and manpower. Elleci has excluded the payback calculation, repartition of fixed costs, and maintenance, which would multiply this figure by two to three times.
- To cover the total production, Elleci would have needed a second traditional punch/laser introducing an additional payback calculation
Total savings generated by the coil fed process
As I showed in my previous article, Elleci calculates the profits generated by the raw material saving in 95200 Euro.
Now, by adding the saving on the operational cost, we get to a total of 197.400,- Euro per year – even not considering the need of a second traditional punch/laser to cover the production requirements.
Efficiency and sustainability of the coil fed process
Let me finally focus on two of the main advantages of the coil fed punching and simultaneous laser cutting system: material efficiency and production speed.
- Material efficiency means: less material to purchase to manufacture the same amount of goods, with also less scrap that needs to be disposed of.
- Higher production speed means: less energy and company resources (manpower, assistance gas, etc.) used to manufacture the same amount of goods.
Leaving aside the other advantages of the combination punching and laser technology, it is clear that being extremely efficient and effective, the coil fed process is also far more sustainable and eco-friendly.
This to me is a simple way to show how profitability and sustainability can go hand in hand, and take advantages from each other.
Conclusions
In order to increase efficiency, process engineers need to look at production methods from a broader perspective.
There are products and industries that, because of their production mix and batches size, can take great advantage of innovative and automated solutions to feed their production lines and reduce the impact of variable and fixed costs.
Looking at how one company analyzed the investment in a new coil fed production line is a very effective way to show how the choice of the right production process can generate significant profits for the metal fabricator, as well as improve the process automation and logistic.
Credits: Thanks to Giorgio Tomasella, Elleci general manager, for sharing and authorizing the use of the information used in this article.