Lean Production and thin sheet metal processing
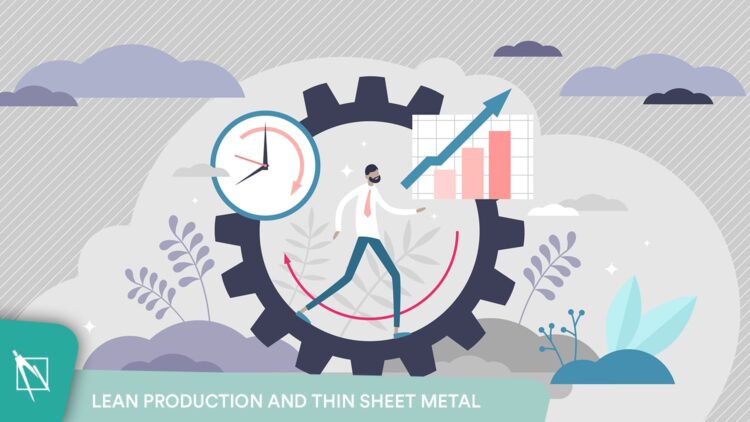
Lean production origins
Lean production was born in Japan, in Toyota company. Its founding father Taiichi Ohno (1912-1990) described it in the book “Toyota Production System”. Japan at that time was a proven country due to the defeat in World War II; it was a land with poor resources and it was a geographically small country.
What is Lean Production?
Lean Production analyzes the flow of production and data through the company, from the Customer’s order to the delivery, and it identifies which operations add value and all operations that do not add value.
Similarly, in the data flow, there are information adding value to the product for the customer and others that do not.
Operations and data that DO NOT add value are identified as “muda”. This Japanese this word is translated as “waste”, but its meaning is more similar to “mortal sin”. From this point of view every muda uses resources that not only do not generate value for customers, but are a cost reducing the sales margin on the final price.
For this reason it’s a mortal sin, because it is identified as something to be eliminated at all costs (if possible).
No more waste
Lean production identifies seven kind of waste:
- Incorrect processes, such as:
- space waste
- raw material waste
- energy waste
- Overproduction (warehouse)
- Unnecessary handling
- Operator routes (logistic efficiency)
- Material handling (Efficiency)
- Waiting times (Productivity)
- Material research
- For set-up
- Defects (Quality)
- Stocks (Warehouse and middle warehouses)
It’s immediately clear that this part of analysis is focused on Efficiency issue.
Each situation and company are different and must be analyzed in a specific way. Each company has, in fact, different products and often even having the same type of product, they sell it packaged in a different way, or in different related services.
Therefore, when studying a production system it is important to organize the flow material input and output in order to:
- Eliminate waste
- Of material
- Of time
- Optimize material routes
- Optimize the size of production batches
- Minimize the intervention of manpower
- Minimize production changeover time
- Arrive to “batch one” when there’s no tools or material change
- Minimize times when there is ta change of tools or material
In Andrea Dallan’s book “The Revolution of Efficiency”, Mr. Höckele, production manager of RIDI Leuchten GmbH company, explains a very interesting application of these principles.
The Revolution of Efficiency is available in the Amazon catalog: follow the link below to see
Buy The Revolution of Efficiency at Amazon!
Lean Production applied to thin sheet metal processings
Every entrepreneur’s work is to generate results by optimizing the use of resources. Referring to thin sheet metal processing, these resources are: raw material, energy, time and labor.
For example, we can produce the same quantity of product using less raw material and energy, or increase the production in the same amount of time. It is also possible to use smarter machines and logistic systems, to work with less manpower or less skilled manpower. Systems that allow very quick setup and production changing, to produce the right quantity without stock.
If you have experienced Lean Manufacturing, you can right notice how analyzing all these aspects it is possible to identify different kinds of waste – called also Muda in Japanese with the meaning of “mortal sin”.
According to Lean Production, all waste must be identified and reduced – if possible eliminated.
Production system for Lean Manufacturing
With over 20 years of experience in the field of thin sheet metal production systems, I realized that very often the systems we produce, such as Coil to Window, Coil to Pack, Coil to Box, Coil to Laser, introduce the principle of Lean Production in a natural way, with immediate benefits.
We constantly invest in developing more and more efficient technologies, integrated with the entire production system. This allows us to offer fully automatic production lines which reduce the waste of resources (raw material and energy), eliminating unnecessary operations (production and labor waste of time), and integrate all the necessary operations in the production cycle in order to guarantee the best final product quality.
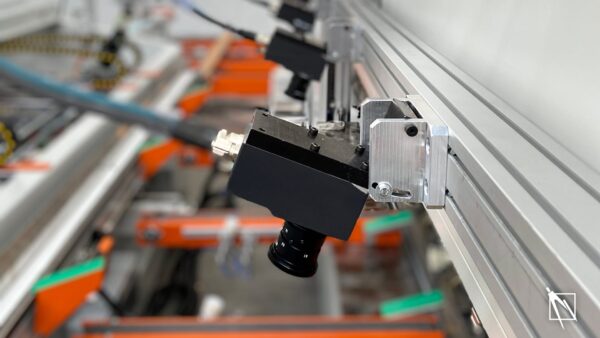
The experience gained over these years let me to meet a lot of companies with different requests, with the aim to improve their production processes, the quality of their products and the efficiency of their business.
In my book I have collected the testimonials of twenty of our customers: the principles of Efficiency, Productivity, Flexibility and Automation are introduced as practical samples and the book clearly shows how all these principles become extraordinary production systems.
If you want to know more about lean production or to stay updated about systems and thin sheet metal working tips, follow our exclusive Masterclass!
Register at www.masterclass.dallan.com
Andrea Dallan
CEO – Dallan Spa