Coil To Window systems for rolling shutters: efficient, fast and automatic
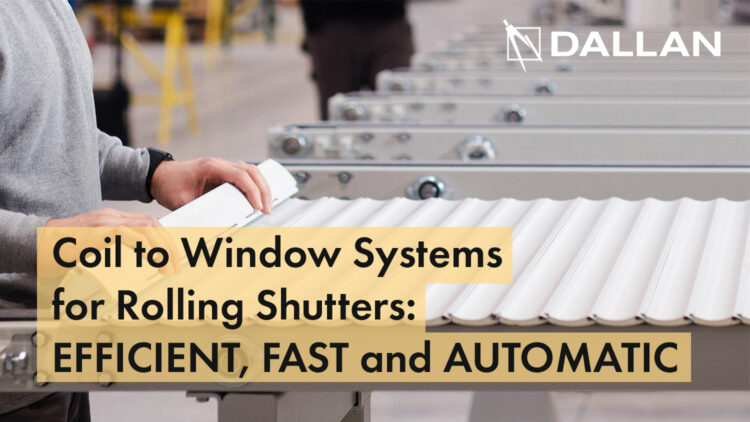
Since the first fully automatic production line was installed in Piacenza in 1999, automatic systems for the production of aluminum rolling shutters and outdoor venetian blinds have become increasingly popular, with systems requiring a single operator to manufacture finished products of the highest quality, starting from an aluminum roll and greatly reducing material waste during the processes.
There are two large families of “Coil To Window” systems:
• “Coil To Window” for rolling shutters
• “Coil To Window” for external Venetian blinds
This part of the book will focus on rolling shutters.
In the 3 minutes it took to read this page, a “Coil To Window” production line can produce a curtain complete with rolling shutter, starting from a coil, without generating waste and using a single operator.
So, imagine making a top-quality rolling shutter curtain in less than three minutes using just a single operator, without material waste.
From an aluminum coil, to a complete, assembled rolling shutter. That’s the secret of “Coil To Window” technology, an extraordinary step forward for highly profitable and sustainable production.
Material waste: a problem in traditional production systems that use bars… becomes a great opportunity!
Rolling shutters are traditionally produced from packs of 6 meter long profiles. These bars have to be purchased, stored (which takes up a lot of space), transported internally, and handled many times so that they can be moved to the cutting and assembly phase.
That is both laborious and inefficient. During cutting operations, 5 to 12% of the material is usually wasted and is not transformed into the final product! This is essentially a waste of aluminum and polyurethane composite material, which is generally expensive to dispose of.
The “Coil To Window” system not only transforms aluminum and polyurethane directly into the final product, it does so quickly, automatically, and ensuring the highest quality finished rolling shutter, in which the operator simply receives the finished curtain from the machine’s exit bench!
These material savings translate directly into profit and positive cash-flow for your business.
Sign up for our Masterclass to access our exclusive video content and find out in detail how these extraordinary systems work!
SIGN UP HERE!
Producing rolling shutters from bars: the problem of having a warehouse of semi-finished products, the handling of profiles and the high incidence of labor
Lean production teaches us to search for and reduce waste and unnecessary processing stages as much as possible, so, that we can focus on the value we provide to the end customer.
One thing is certain. The production of rolling shutter curtains using bars is far from this ideal scenario! First of all, you need to have and manage a stock of bars for the various profiles.
These profiles are particularly long, they require sturdy, specific containers. Automatic storage systems are bulky and expensive machines, and they encourage you to store a large quantity of semi-finished profiles which represent an enormous capital investment.
When they are handled inside the company, they require wide corridors and handling is anything but easy. When handling such long bars, you need to be very careful not to damage the profiles. This would result in a finished product (the assembled rolling shutter) of questionable quality.
Furthermore, we consider the incidence of labor required for the movement, processing of the bars on packaging machines, and the management of the finished product: a problem not only for labor costs, but also because reducing labor incidence makes production safer, even in situations of health emergencies where automatic production is strongly recommended.
Coil To Window production: a single operator to go from coil to finished product, with no material waste.
All these problems (material waste and high labor incidence) find an extraordinary solution in Coil To Window production systems.
First of all, the line produces starting from coils. The raw material warehouse consists of pre-painted aluminum coils for different colors and the polyol and isocyanate needed to produce polyurethane foam, instead of an automatic warehouse with large quantities of semi-finished products, which are inherently more expensive.
The coils include thousands of meters of profiles in a very small space, which are directly transformed into roller blind sheets by the production line.
The Coil To Window system cuts the bars to size, practically eliminating waste (which will total less than 2%): the raw material is almost entirely transformed into the finished product! There are no more boxes of profile waste (a combination of polyurethane and aluminum) to dispose of, and the process becomes automatically more environmentally sustainable and profitable for your company.
Moreover, in the process, only one operator is sufficient to supervise the process, load the raw material, check and receive the finished sheets at the exit.
One operator, instead of approximately four operators required with the traditional process, for the same production amount!
Fewer product manipulations mean much higher production quality: the risks due to operator errors are eliminated, and by reducing the necessary labor, production becomes inherently safer and much more profitable for your company!
Benefits of invaluable value, as we have seen during the recent 2020 pandemic: contact our specialists immediately and enroll in Dallan Masterclasses to access our exclusive video content!
SIGN UP HERE!
Andrea Dallan
CEO – Dallan Spa