Flexibility in Profiling Processes: The Solution of Parametric Punching and Flexible Profiling Systems
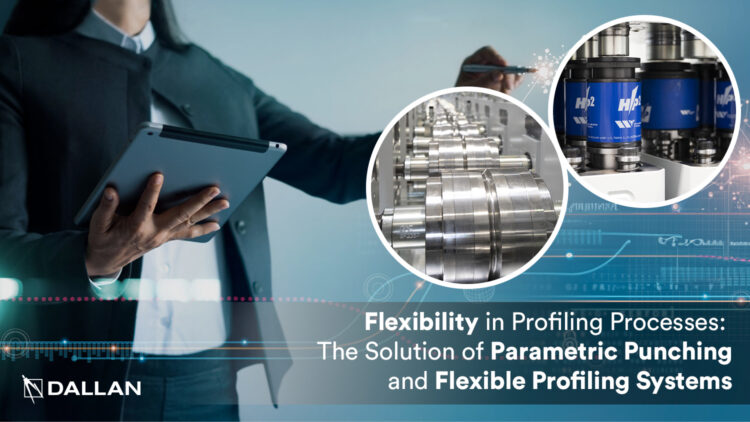
Filter frames are a very particular profile: they are U or C shaped profiles with different base sizes, depending on the thickness of the filter material.
They also vary in size depending on the frame dimensions.
For such profiles (and there are many, like C, Z, and Sigma construction profiles, shelving profiles, and those for poultry systems), the combination of parametric punching with a flexible profiler with moving heads is the ultimate solution.
Starting with punching: these profiles clearly belong to families, featuring notches and head processes that allow for bending and frame closing.
In a sheet punching machine, we would need to create a DXF of the open profile, then process it with a Cad Cam program.
The parametric coil punching machine, however, allows for quickly and graphically creating one or more Master programs, which include all the rules defining the product.
The parametric program provided with Dallan lines then works from simple Excel or CSV tables as shown below:
Parameters can be dimensions, whether to activate punching or printing codes on the piece.
This table is loaded into the office program, which immediately generates two types of files: the JobList file (or work list), which includes quantities and production orders, and several .Job files, which are practically the part programs already adapted with the correct dimensions for each piece.
There are also other file formats, however, the concept is clear: save programming time for the plant and transmit all parameters electronically to the machine to start production.
Then, the strip is punched with the numerical control system and produces, without waste, all the frames with the same width, one after another.
This punching machine moves the strip in the X direction, while the punches (of standard type) move on a turret in the Y direction.
Pre-punched strips then enter the profiler, which has moving heads to adapt to the different widths of the strips.
Following this LINK, you will see a punching and profiling line with an asymmetrical double head, which allows it to create frames from 8mm up to 100mm in width.
At the end of the profiling, the final punching and cutting unit identifies a pilot hole and performs all those operations in the correct position, which cannot be done before profiling: in this case, the cutting and 90° bending of one of the terminals.
The products coming out of the line can therefore have slightly different dimensions, but are ultimately similar.
At this point, a problem arises: how does the operator recognize them?
When working with products parametrically, it’s common to associate the line with an inkjet or laser printer, which identifies each piece with a unique code and the dimensions written with alphanumeric code or barcode.
With these tools, there is no need for an experienced operator or programmer to produce perfect, punched, bent, and properly divided products without waste.
Other parametric products include door frames, metal furniture, and reticular structures for construction.
The punching and profiling system like the one just seen solves all these productions without wasting programming time.
Contact our experts to learn more!
CONTACT US
Andrea Dallan
CEO – Dallan Spa