Plant Obsolescence: The Three Steps to Ensure Productivity and Support
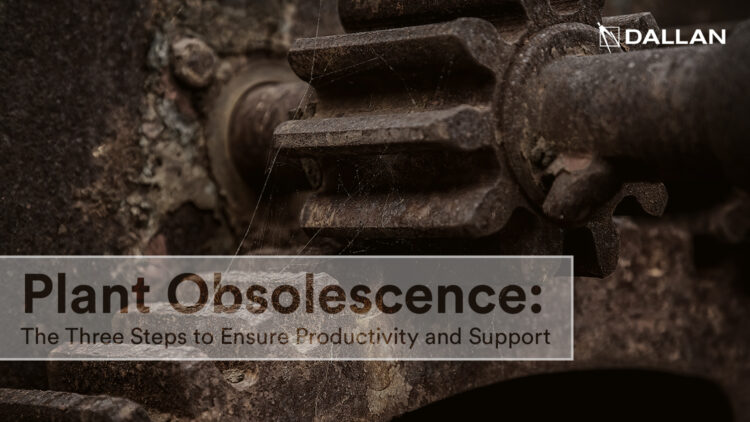
Many companies tend to believe that their Dallan plants are eternal. This is very gratifying for us, but when machines exceed twenty years of life, it exposes you to certain risks.
I’ll give you the example of a client who between 1990 and 2000 bought from us five roll formers that contributed to his company’s fortune, which grew immensely until 2005 when, unfortunately, the owner passed away.
The new management found a company with functional and still perfect machines and, I have to say unfortunately, took the performance of its production system for granted. They stopped investing in maintenance and, in recent years, in spare parts as well. As we’ve seen, this inevitably leads to a deterioration of plant performance.
Needless to say, like a car, production plants need to be “serviced”!
Unfortunately, in the last five years, another problem has arisen: the electronic components used at the time, such as PLCs, drives, and boards, are no longer in production. Many of the machines were powered with direct current motors, with very inefficient circuits.
Once the client started having failures in these devices, we were already in an unrecoverable situation, so we are proceeding with the replacement of all plants.
Luckily, all machines are combi type and we’ve been able to reuse most of the equipment!
A more continuous investment over the years would certainly have given these machines a longer life horizon, and above all, it would have been possible to intervene with targeted revamping to resolve the critical issues as they arose.
So, if you have plants between twenty and thirty years old, mechanically still robust and usable, you know that the critical point is almost certainly the electrical and electronic parts. Here’s what we advise you to do.
First, contact our service for an inspection.
The inspection is essential to check the state of the machines, the type of electronics still on board, the level of safety, and to verify if there have been undocumented interventions by third parties.
At this point, our technicians will draft a report and the scenarios that open up are, clearly, many.
Let’s look at three examples.
Scenario 1: the line is substantially in order, and the most critical spare parts have availability of at least 10 years.
In this case, we prepare a list of activities for each of your machines concerning:
- Safety part
- Mechanical, pneumatic, and hydraulic part
- Electrical part
- Electronic part As for preventive maintenance, you will also receive an offer for the recommended spare parts to keep in-house or to use for the actual maintenance intervention, which will be carried out shortly thereafter.
Scenario 2: the line is in order, and the most critical spare parts have a 5-year availability
In this case, in addition to the above interventions, it is evaluated whether to rebuild part of the electrical panel and replace the motors, without changing the logic of the line’s operation.
Scenario 3: the line is in a state of abandonment, and the spare parts are no longer in production
This is the most critical scenario in which, unfortunately, we have had to work with the client I was telling you about. In this case, unfortunately, you are at the mercy of fortune.
Transitory emergency interventions can be evaluated, but the recommended course of action is to replace the plant’s base with a new generation one.
If, as in my client’s case, your machine already has the combi system, you are in luck! We will only have to reproduce the base, since all existing combis are reusable on the new machines! If, on the other hand, as in another case, your machine is built without the combi system, we will propose replacing the machine with a new generation plant.
And indeed, after 20 years, your company deserves it!
CONTACT US
Andrea Dallan
CEO – Dallan Spa