Roll forming: how to get the most out of thin materials
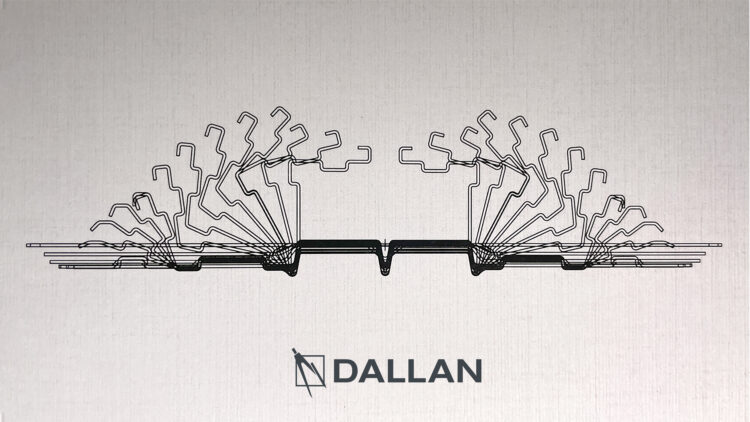
The processing of thin materials in roll forming requires very different calculation and adjustment tools compared to thick materials. In particular, the thinner the material, the more difficult it is to evaluate the spring back for open profiles, as well as for closed profiles.
At Dallan, we have been developing specific calculation tools and algorithms for thin metal sheets since 1978. This has driven the development of our company and has become the distinctive factor of Dallan machines and equipment.
The image here shows the accuracy of Dallan roll forming machines in a comparison between the theoretical design and the final result of a rolling shutter profile with a thickness of 0.20mm plus paint. The rolling shutter profile is one of the most technical made by Dallan systems. Since it is not a static profile, the hook needs to work correctly during winding and unwinding for the entire lifetime of the product.
Watch the video here below: you will be able to see an amazing application of construction modules made using thin sheet metal!
The original 1974 study of thin materials
In 2019, 45 years after its publication, we published the thesis written in Italian. It was written by our founder, Sergio Dallan, for his university degree. The subject was the cold forming of thin metal sheets. Starting from this study, entitled “The design of rollers for light profiles”, published in its original version and complete with all its formulas, our company gradually began to develop, first as a design studio, then as a manufacturer of roll forming machines on the Italian market and subsequently on the international market as well.
The formulas were included in the original Dallan roller development software, which we still use today. It has been updated with the experience accumulated in forty years of work.
You will not find this book on newsstands or on Amazon: to request a copy, write to [email protected]
Characteristics of coatings for roll forming and bending radii
In addition to the development of special techniques for thin materials, from the very beginning we started working in sectors such as metal suspended ceilings and rolling shutters, where many profiles are made of pre-painted material.
When forming an aesthetic profile with a pre-finished surface, particular care needs to be paid to the design in order to guarantee product quality.
Indeed, as the profile is being formed, the rollers have different peripheral speeds with respect to the neutral speed line of the profile.
Nowadays, organic coatings display excellent resistance to scratches and abrasions, nevertheless the forming of a profile has to minimize the differences between peripheral speeds.
The reference standard for resistance to the abrasion of coatings is, for example, UNI EN 13523-12.
As for all production lines in roll forming, the quality of the finished product largely depends on the quality of the initial design.
In fact, when studying the product and the flower of the profile, the elasticity of the paint must always be taken into consideration. When we bend a sheet metal product with a certain radius and imagine a neutral line about halfway through the thickness, the material inside the radius will be compressed and the material outside will be stretched.
Obviously the paint on the outside of the material will also be stretched more than on the neutral line. We need the coating to have good levels of elasticity to perform the bend, especially when small bending radii are involved.
In fact, coatings are classified according to their ability to be bent using small internal radii without changing color and without cracks appearing in the coating. The reference standard, for example, is EN 1396.
The procedure is simple, we take a small pre-painted square of metal frame sheet and fold one edge on itself at 180° with an internal radius equal to zero.
If no cracks or lines showing the underlying material appear in the coating, we classify the material as T0.
This means that the coating has maximum elasticity.
There are only a few materials with this characteristic. So, if we see cracks, lines, or color changes, we fold the material on itself once again, leaving the material inside so that we obtain a fold with an internal radius equal to half the thickness.
If the surface of the folded area remains intact, the material is classified as T0.5. Otherwise, the folding process is repeated until the outer surface looks perfect.
A good rule of thumb for thin sheets is to design profiles with an internal radius equal to the thickness of the material.
Dallan’s initial specialization in thin materials: this led to an increasing number of companies that process pre-painted and pre-finished materials to contact Dallan to develop new products. Indeed, the first big leap in the development of the company was in the field of suspended ceilings and interior finishes, then rolling shutters, sun protection, and cladding.
Lots of materials, especially aluminum, reach base thicknesses even less than 0.20mm. The thickness of the paint (in the case of liquid painting) varies from 0.02 to 0.03mm, hence up to 15% of the total thickness of the material!
Therefore, the characteristics of the paint influence the forming process from a mechanical standpoint and experience is essential to take these variations into account so that the profiles produced are of the highest quality.
It is also necessary to consider certain characteristics of the paint, in particular elasticity. This is to ensure that the paint adheres to folds with the smallest bending radii.
Taken from the book “The Revolution of Efficiency”
REQUEST THE BOOK FOR FREE
Andrea Dallan
CEO – Dallan Spa